Timber portal frames are one of the most favoured structural applications for commercial and industrial buildings whose functions necessitate long spans and open interiors. As a material choice, timber offers designers simplicity, speed and economy in fabrication and erection.
Timber portal frames offer a strong, sound and superior structure. Structural action is achieved through rigid connections between column and rafter at the knees, and between the individual rafter members at the ridge. These rigid joints are generally constructed using nailed plywood gussets and on occasion, with steel gussets.
From material selection to finishing, this application guide provides a comprehensive overview of the process of using timber in the specification, fabrication and erection of portal frame structures.
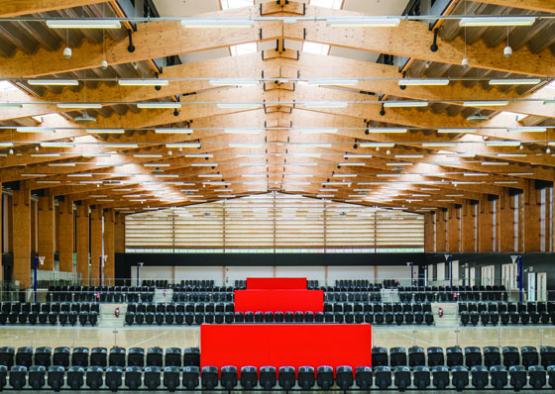
Timber portal frames are one of the most favoured structural applications for commercial and industrial buildings whose functions necessitate long spans and open interiors. As a material choice, timber offers designers simplicity, speed and economy in fabrication and erection.
Timber portal frames offer a strong, sound and superior structure. Structural action is achieved through rigid connections between column and rafter at the knees, and between the individual rafter members at the ridge. These rigid joints are generally constructed using nailed plywood gussets and on occasion, with steel gussets.
From material selection to finishing, this application guide provides a comprehensive overview of the process of using timber in the specification, fabrication and erection of portal frame structures.
The absence of internal columns, large spans and low profiles makes portal frame construction particularly popular in industrial and commercial building applications. The use of timber and timber components in such buildings is both economic and aesthetically pleasing and, combined with the other inherent advantages of timber construction, have been responsible for ensuring timber remains the preferred material choice in this mode of construction.
Timber portals may be clad with other timber products such as plywood and weatherboards. For large-scale factories and warehouses, conventional metal or fibre cement cladding is common and for the more commercial type applications, cavity brick and brick veneer. Internally, purlins can be exposed as cathedral ceilings or sheeted on the underside with conventional ceiling lining materials, alternatively the frame may remain ‘raw' and natural.
Portal frames have the primary objective of resisting lateral loads caused by wind acting on the walls. They distribute the wind loading from the end walls into a wind truss or roof bracing and from there into bracing elements located at convenient positions in the sides of walls.
Structural action for timber portal frames is achieved through rigid connections between column and rafter at the knees, and between the individual rafter members at the ridge. These rigid joints are constructed using a substantial number of nails with gussets of either steel or plywood, creating a connection that is simple yet highly efficient. Various layouts, that balance cost and appearance, can be used to achieve the moment restraint.
Timber portal frames are usually designed with pinned bases as there is little structural benefit in making the base joint fixed. Tudor arches (3 pinned portals) are effective with pitches about 20° to 50°, with spans to 40m. Two pinned portals are generally effective up to 12m for solid timber, 35m for glue laminated structural timber and to 40m for plywood box beams. Where gussets are used, pitches should be kept above 10° as it is difficult to design plywood ridge gussets for low-pitched frames.
The deflections predicted during analyses by using the Short Duration Modulus of Elasticity 'E' must be modified by 'j2', the Duration of Load Factor for Deflection relevant to loads that act for 5 months or more. This means that dead load deflections need to be increased by a factor of 2 and 3 for members of seasoned and unseasoned timber respectively, with the internal forces remaining virtually unchanged.
For average circumstances of geometry and loadings, the dead load + live load combination often governs member design. Eave displacements may be more critical where design wind velocities are in excess of 40 m/s. The NZS3615, predicts the relaxation caused by the joint moment and this may be used if a more exact analysis is appropriate.
Low pitch portal frame design is governed by bending stresses, with the critical areas being the knee, ridge and mid-rafter length. It is usual to rely on purlins and girts to provide lateral restraint to members and so the slenderness coefficient 'S' is based on a discrete restraint system.
Fly braces are required where secondary members are not deep enough to provide sufficient torsion restraint to the frame. The fly braces may be simple hoop iron angle bracing, prefabricated 'K' bracing or substantial moment generating cleats that double for the primary purlin fixings. AS1720 gives guidance on the magnitude of the loads that the connection has to resist.
Timber has a low modulus of elasticity compared to steel, and so for the relatively shallow sections used in portal frames, deflections are more significant. If relaxed serviceability criteria (more flexible frames) is adopted for more economical design, then the pitch has to be increased above the roofing manufacturers minimum recommendations.
Vertical movement of the ridge should be calculated to ensure that differential movements between the end wall and the adjacent frame are not excessive. The allowable limits are related to the member stiffness and their connection detailing. The horizontal movement of the eave must be compatible with the cladding in the end wall and other elements such as windows, doors and gantry beams. Additionally the allowable deflection must be compatible with any heavy weight cladding on side walls. For such materials a limiting movement of eaves height/300 is recommended.
The most significant movements of the structure occur in response to the maintenance load (downward at mid-rafter span and ridge) and wind to the side of the building resulting in positive pressure acting on the windward roof (horizontal movement at the eave).
The full gusset is a simple triangle cut from a plywood sheet with a length limitation of 2400mm or 2700mm depending on the plywood manufacturer. Similarly 1200mm is the sheet limitation to the gusset depth. The full gusset provides more nailing area for a smaller gusset depth and so may be an advantage when used with higher strength members. For the full advantage to be realised, the plywood should be both a high stress grade and a joint group similar to the main members.
Once the length limitation is reached, the truncated shape has to be used. For a most efficient nail group, the nails should be located around the periphery of the gusset as this increases the effective polar movement of the area more rapidly.
AS1720 specifies edge and end stances that must be adhered to in order to maintain fastener performance. Practical experience has indicated that smaller and larger spacings will be required, depending upon species and moisture content.
For plantation softwoods an increased nailing density leads to a more compact group. Where nailing is laid out around the periphery of the gusset it may be reduced. There is a correlation between joint strength and timber density and so timbers of a low density such as fast grown Radiata Pine from New Zealand would be relegated to JD5 while the Australian grown timber of the same species is allocated JD4 in AS1720.
Experience has shown that the stress distribution resulting from the applied moment is non-linear. Plywood is laid up in odd numbers of veneers so that the external veneers run in the same direction. In the design of the gusset, it is more efficient to use a plywood with a more pronounced strength in one direction. This is known as the 'equal ply' lay out, with all plies of relatively the same thickness. When the gusset has to resist bending, only those fibres running parallel to the indirect tension can be effective.
The plywood gusset must be designed to resist the axial compression (and tension) that again is resisted by the parallel plies only. The unstiffened part of the gusset is able to buckle and can be designed to resist this as a diaphragm. Here it can be seen that the diaphragm is acted upon by compression shear and moment and logically is governed by an interaction equation. The only unusual concept is that shear is resisted by all plies, while moment and axial load is taken only by the parallel veneers.
Steel gussets are designed according to AS1250, Steel Structures Code and for economy are kept as thick as possible. Buckling is a problem, so the nail groups have to be effective in withdrawal to prevent it. It is normal practice for the plates to be aligned on the members centrelines and a welded 'L' is generally more efficient than cutting to the plate shape.
Base plate types are varied but preference should be given to simple connections that will minimise steel fabrication costs. The loads to be resisted include axial load (both tension and compression) and shear load. The function of the base is to cater for these combinations as well as providing a minimal moment restraint as an aid to erection of the columns.
Consideration must then be given as to whether the connection should be cast into the concrete slab or pier. Alternatively hold-down bolts may be cast in to receive base plates. A third alternative for smaller structures, is for hold down bolts to be epoxy grouted into the concrete.
All connections should separate the timber from the concrete. Either bearing plates can be used or a damp proof course installed. For economy, the timber connection should be a single bolt or, if absolutely necessary, two bolts. Bearing failure of bolt to steel is generally the determinant for the steel thickness.
Buildings typically contain bracing elements that transmit the wind from the end walls to the ground. The racking forces are carried from the mullions into the roof place and are transmitted to the purlins and roof diagonals and then to the bracing walls. The purlin-rafter connection has to transmit tension to counteract wind suction acting on the end wall. Bracing elements are usually crossed so that wind loading at each end wall is resisted at its end rather than transmitting it via the eaves tie to a single bracing element. This results in less load on the connections and as a result, cheaper solutions can be used.
Purlins may be:
- Solid timber (approx 6m limit)
- Nail plated built-up sections
- Glued laminated structural timber (generally only used for appearance purposes)
- L V L
- Plywood webbed beams (Light, stiff and easily fabricated. Often appear as either nailed 'C' sections or glued 'I' beams. The former will require more lateral restraint.)
- Parallel chord trusses. (Similar advantages to plywood webbed beams with the added facility to accommodate services.)
The purlins are designed to resist maintenance and wind loads and, in the vicinity of the roof bracing, carry some compression. They can be simply designed by using published tables, bearing in mind, AS1720.
Purlins are usually set between the frames, rather than across the top, to provide stability for the purlin ends as well as intermediate restraint for the rafter.
For unseasoned timber, fabrication should not commence until the moisture content of the timber is lower than 20%. Trial fabrication is also highly recommended to check the timber performance and suitability of equipment before major fabrication commences.
It has become common practice to fabricate rafters, purlins and roof bracing on the ground, and then lift the roof (in sections or fully) onto the columns. The through-rafter method facilitates this method of erection better than the mitre joint.
The rafters are erected on the floor and adjusted to the correct pitch. To avoid interference during lifting ensure the whole roof is laid out approximately 500mm along the building from its designed position.
The ridge gussets should be nailed off and the purlins installed with the exception of those in the immediate vicinity of the columns, which should be fitted after erection.
Mark the set out on to the floor to ensure that the pre-fabricated roof is as specified. Hoop iron crossed bracing is installed to preserve a square structure while lifting and this may also be effective as the final roof bracing. The purlins should have all connections installed at this stage.
Knee gussets are first nailed completely to the columns erected onto their base plates. If the base plate is capable of providing some fixity in both directions then that will be sufficient, if not temporary bracing must support each column.
- Each frame must be supported during lifting, as the purlins are generally discontinuous. When multiple bays are erected, lifting beams or strongbacks must be used.
- The frames can be quickly erected with the knee gussets wedged apart to facilitate rafter entry and the columns readily swayed to accommodate any inaccuracies of fabrication.
- Longitudinal bracing elements can then be installed and note that the rod and turnbuckle type facilitate plumbing of the end columns. The columns have to be plumbed across the building by props or by a jemmy bar and then the knee gussets are ready for nailing.
- As cranes support the frame the entire time, it is worthwhile investing in suitable equipment to facilitate quick completion of the column and nailing phase to reduce hire costs. As the full load is not acting at this stage, not all nails have to be driven; but all gussets must be nailed before releasing the load from the crane.
- After crane removal, remaining nailing can be completed, together with installation of the eaves, purlins and girts. The mullions and the end wall girts can then be installed together with any additional roof wind bracing. Apart from the treatment of the openings the structure is now ready to be clad.
Erection of box-beam frames are similar with the only notable difference being the steel plates are not as flexible as ply gussets and hand nailing is more time consuming. The lighter frame may result in reduced crane hire costs.
Buildings with a strong visual focus, such as glue laminated commercial constructions should be finished and (where possible) covered with building paper prior to erection. If any elements are to be painted or treated this should also be carried out prior to erection. Steel gussets should receive their finished coat after all nails have been driven. Throughout the assembly process it is wise to provide all fabricated components with temporary protection from the weather.
Glue laminated timber (Glulam), laminated veneer lumber (LVL), sawn timber and plywood webbed beams are all common materials used for portal framing.
Glue laminated structural timber may be considered a solid timber and is well suited to portal frame production. With no restrictions on nails being driven on or near the glue lines, it provides freedom in the location of moment joints as well as the secondary member arrangements. The material is ideal for carrying gantry cranes and being a solid section it has fire resistance that can reliably predict the survival of the frame.
Laminated Veneer Lumber (LVL) is essentially a vertically laminated glued beam comprised of soft veneers. The product is manufactured using thick plywood technology and is supplied to a maximum size of 1200 mm deep and 63mm thick. Lengths are limited only by handling and transport, although 15 metres is the recommended upper bound.
Design procedures are identical to glue laminated structural timber with the exception of the lamination factor not needing to be applied to the allowable design stress. Note that the butt joined internal joints of LVL are suitable for portal framing.
LVL manufacturers should be consulted for specific design properties.
For applications involving above average portal frame spans, a more efficient section is provided by a fabrication comprising of timber flanges, (solid timber, glued laminated structural timber or L.V.L.) connected with plywood webs. Typically these are arranged as box-beams, which due to good bonding strength about the ‘YY' axis, have increased buckling resistance. Design procedures have also been formulated for 'l' and double 'I' beams. Typically construction is nailed, however note that nailed construction results in some slip and so an equivalent member has to be larger than the rigid glued product. Where the forces require it, it is common practice to reinforce the flange by adding extra flanges resulting in an efficient and light product. An alternative construction method to nailing is gluing (resorcinol adhesive factory fabrication only) with nails providing temporary clamping during curing.
Splices in the flanges are usually mechanically jointed using steel nailplates or lapped timber. Splices in the plywood webs can be nailed or glued. Common design procedures call for internal stiffeners to provide a base for fixings. These are best located at web splices and where purlins and girts are to be connected.
The most common gusset materials are plywood and steel. Plywood should comply with AS2269 and be branded under the Plywood Association of Australian Quality Control Program. Steel should comply with AS1204.
Due to limitations of available sawn sections with low shrinkage, 12m is the practical span limitation for sawn timber. All sawn structural timber should comply with the relevant Australian Standard.
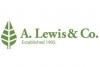
A. Lewis & Co. PTY LTD
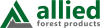
Allied Forest Products
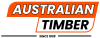
Australian Timber

Bakers Joinery
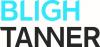
Bligh Tanner
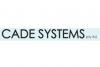
CADE Systems Pty. Ltd.
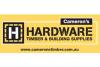
Cameron's H Hardware
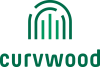
Curvwood
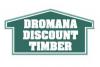
Dromana Discount Timber
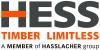
HESS TIMBER GmbH
L.A. COST SRL
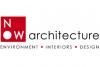
NOWarchitecture
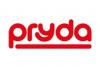
Pryda
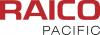
RAICO Pacific Pty Ltd
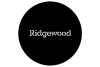
Ridgewood Timber Pty Ltd
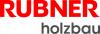
RUBNER HOLZBAU Srl
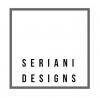
Seriani Designs
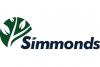
Simmonds
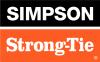
Simpson Strong-Tie
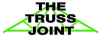
The Truss Joint
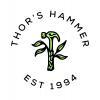