Architects, engineers, developers, builders and everyone else involved in a project from start to finish all play a critical role in shaping our built environment, and their decisions have a profound impact on people's lives and the planet. Building with wood is not a new concept, but it's gaining momentum as we seek sustainable, healthy, and cost-effective solutions for our cities. In this article, we summarise a presentation given by WoodSolutions expert Paolo Lavisci at the Green Building Council of Australia's TRANSFORM event on March 23, 2023, about how a Triple Bottom Line (TBL) approach can be achieved with timber structures.
The Triple Bottom Line is an accounting framework that consists of three parts: social, environmental and economic. It's a useful tool to evaluate a building project's performance and create greater business value. By measuring the three criteria, we can optimize the overall result by finding the balance or "sweet spot." In other words, a project that achieves a Triple Bottom Line is sustainable, healthy, and profitable.
Paolo Lavisci explains that the built environment plays a significant role in achieving Australia's decarbonisation objectives. While energy efficiency measures and renewable energy sources help to address operating emissions, the embodied carbon in the materials used in construction is becoming an increasingly important component of the carbon emissions profile.
To measure and consolidate the benefits from carbon capture and storage, Environmental Product Declarations (EPDs) are the preferred source of data because they are based on a standardized and consistent set of rules. EPDs make comparisons possible and objective both between alternative materials, and within material typologies.
Product-specific EPDs are preferable when available, but in early-stage design and feasibility analyses, when a supplier hasn't been chosen yet, industry-wide EPDs like the ones you can freely download from WoodSolutions, are necessary.
EPDs also help track the evolution of a product or sector over time. For example, for Australian sawn softwood, there was a 12% improvement in 2020 with respect to 2015, primarily due to optimized drying efficiencies.
Maximizing the effects of carbon sequestration requires the industry to consider future disassembly options that will allow for reuse and recycle, which is now made safe and easy by the amazing evolution of connectors.
Using Engineered Wood Products (EWPs) is a smart way to achieve a Triple Bottom Line. Trees are an efficient decarbonizing machine, and using more wood from both plantations and sustainably managed forests helps landowners justify their investments and risks, supports rural communities, and enables construction industry professionals to achieve better results. Wood is also an element in biophilic design which has wellness benefits for those who inhabit the spaces. Additionally, wood has lower emissions and higher carbon sequestration, making it a valuable material for reducing embodied carbon.
One example of the value proposition of wood-based products within the Triple Bottom Line logic is the AUD 300 million Timber Building Program launched by the Clean Energy Finance Corporation (CEFC) in 2022. The program's parameters are multi-faceted: CEFC's investments are made at commercial returns, and financing packages are structured to optimize sustainability outcomes on a risk-adjusted basis. The program is part of CEFC's broader strategic focus on reducing embodied carbon as an essential component of a low emissions economy.
To illustrate how timber structures allow investors, developers, their consultants, and suppliers to achieve positive Triple Bottom Line results, Lavisci chose six recent projects in Australia on which he had an advisory role. The projects demonstrate that building with wood can be bearable, equitable, and viable.
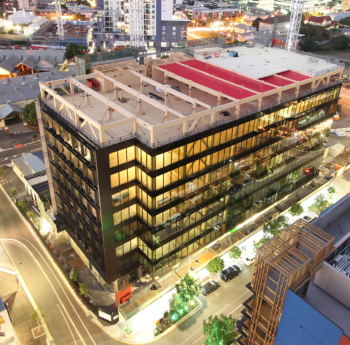
For example, the 25 King Street project showed 74% less embodied carbon and 81% less waste in the landfill than an equivalent RC structure.
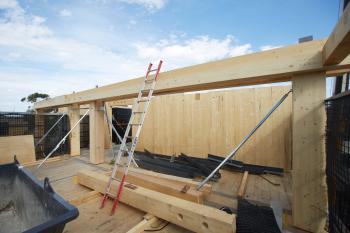
The LaTrobe Uni Student Accommodation project had 75% less embodied carbon than an equivalent RC structure and was 2.5 days/level faster cycles than for an equivalent RC structure. These projects are outstanding examples of future-proof real estate investments that provide much more value than described.
Building with wood is a smart way to achieve a Triple Bottom Line. It's sustainable, healthy, and profitable. The Triple Bottom Line is a beneficial place to start when evaluating a building project's performance. By measuring the social, environmental, and economic criteria, we can optimize the overall outcome. The future is looking bright for the timber industry, and we have an opportunity to shape our built environment in a sustainable and innovative way.
Download the full presentation now.