Balgowlah NSW 2093
Australia
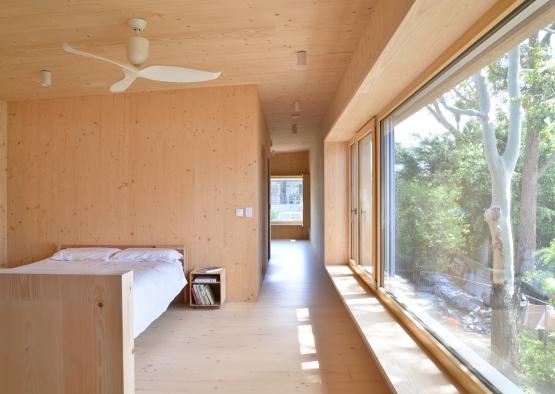
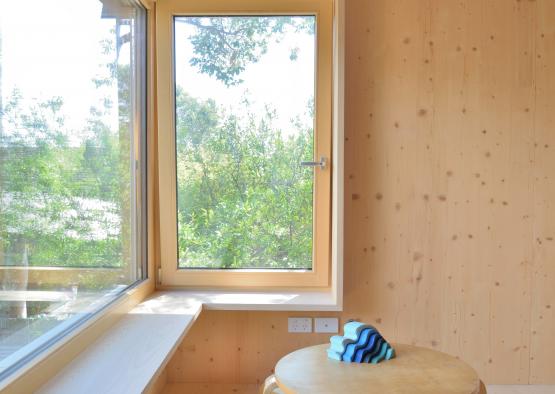
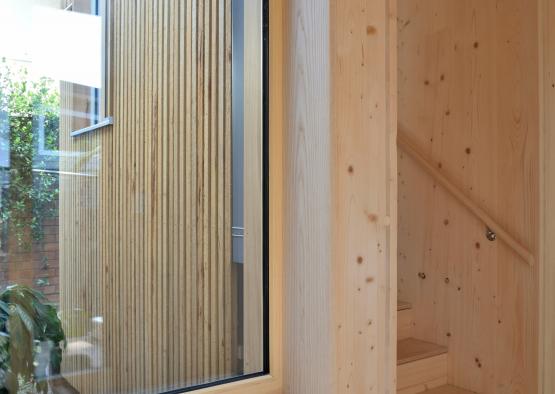
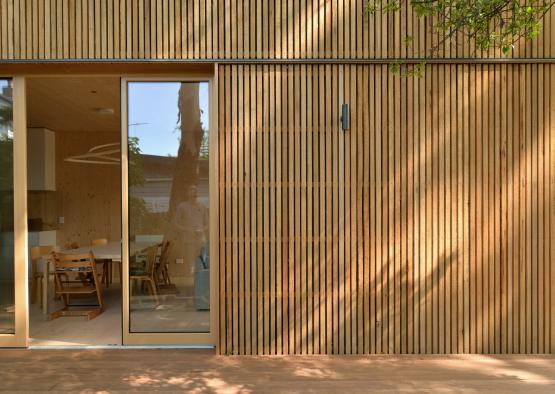
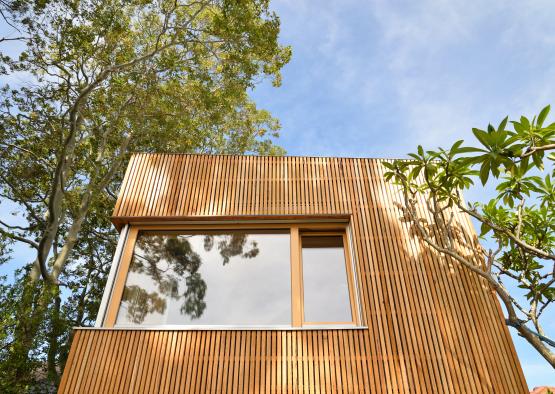
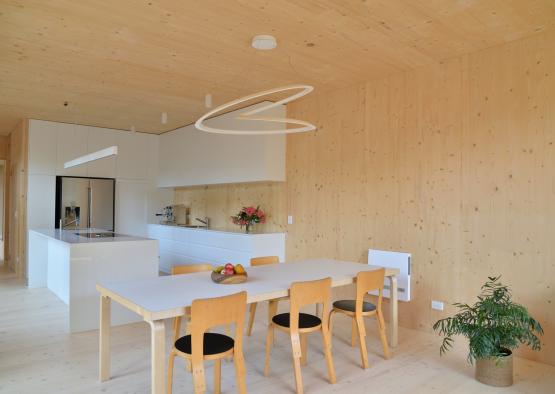
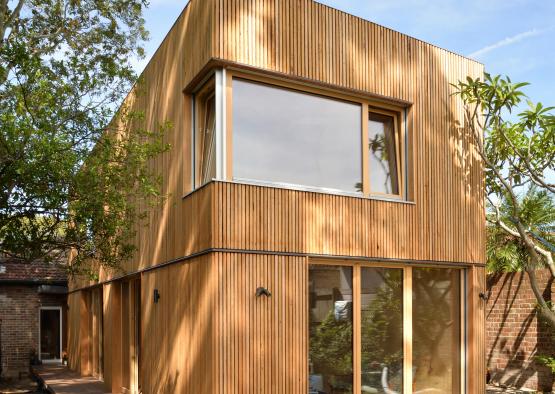
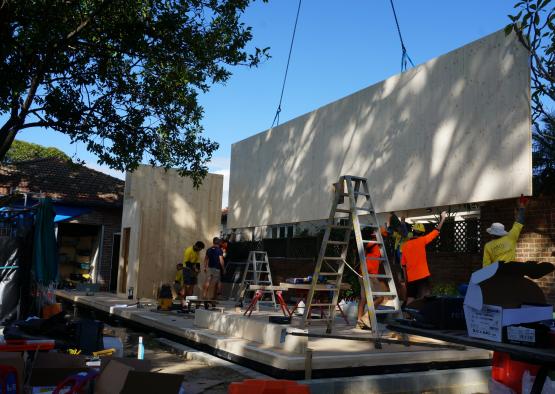
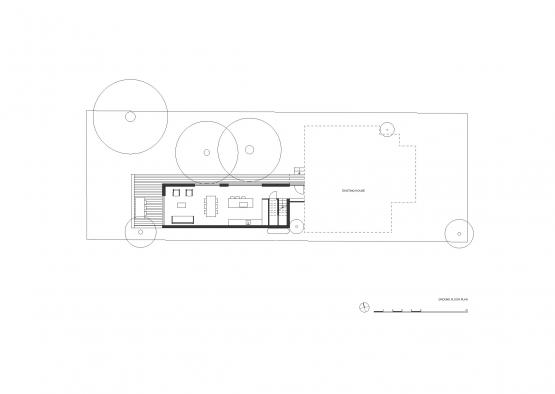
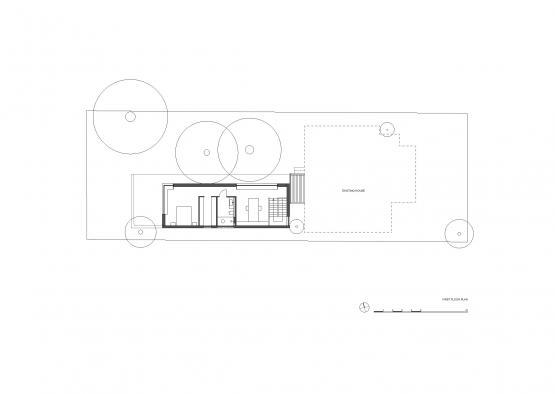
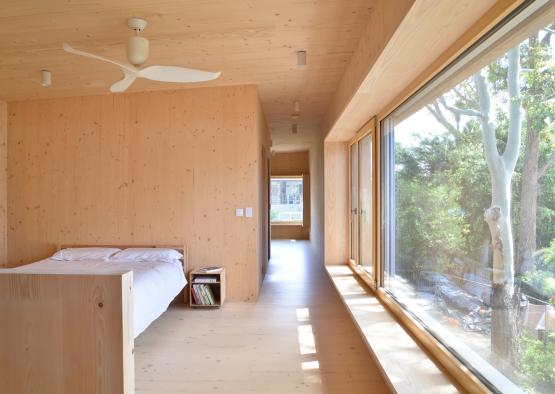
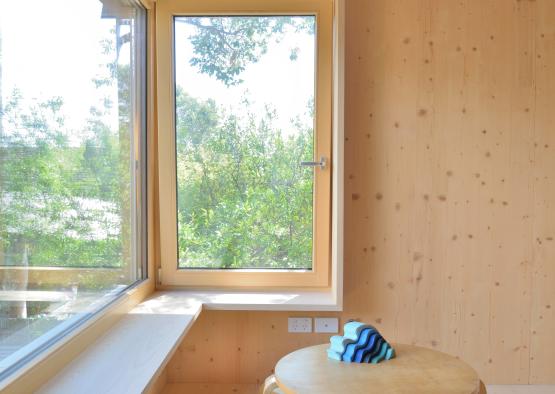
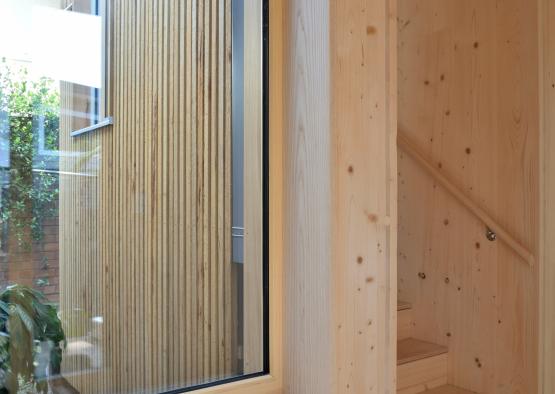
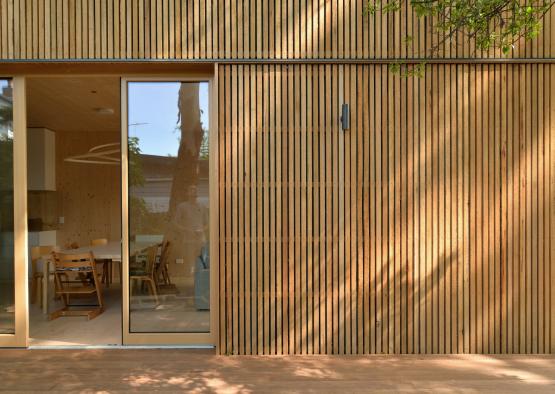
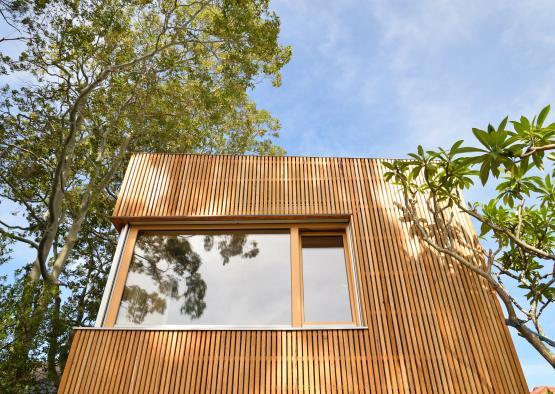
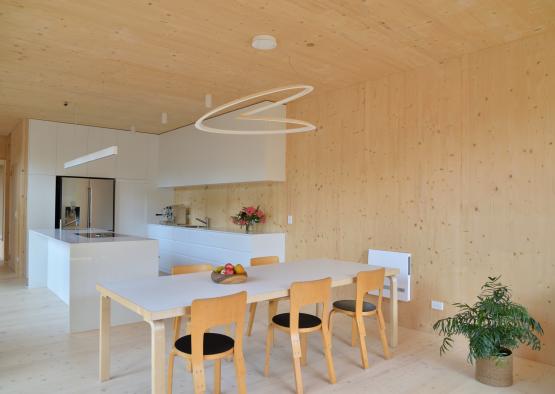
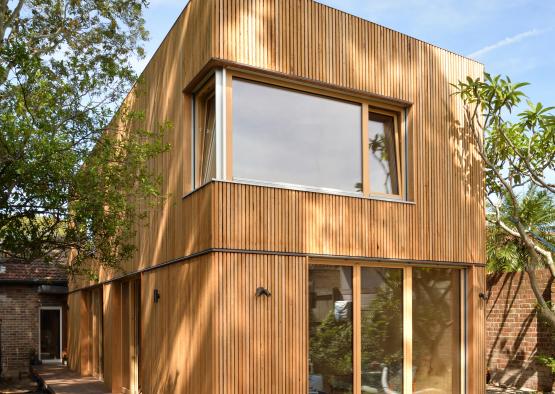
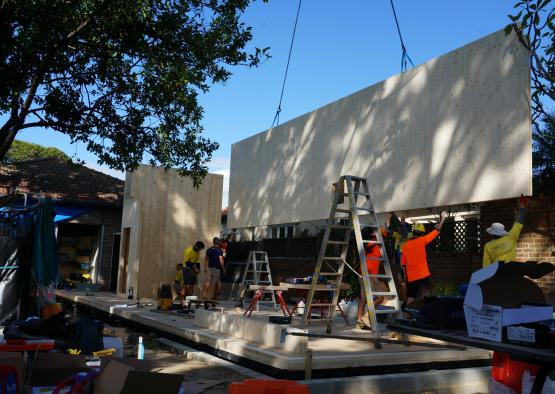
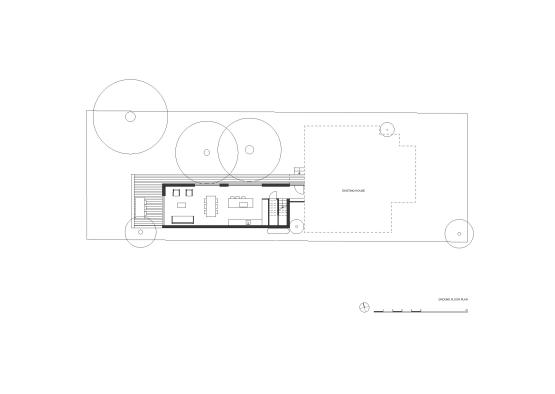
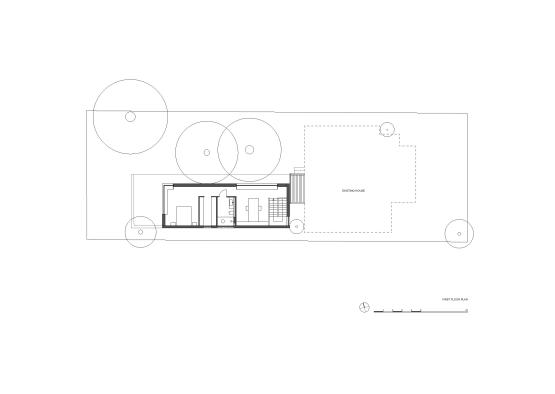
Overview
The project site was located at the back of an extremely tight site with little access. On top of this, the clients were still occupying the existing house. A prefabricated structural system was decided upon to create minimal impact on their lives.
-33.794418, 151.264853
Structure
The cross-laminated timber (CLT) structure was prefabricated offsite, including the stair and cut-outs for lighting, power and equipment, and installed in just 15 hours. Within 10 days the building envelope was airtight, insulated and waterproof, so all other trades could continue internally without being exposed to the weather.
Spruce timber was used for the manufacturing of the CLT panels. All walls and ceilings were left untreated, whilst the floor was treated with a hardwax oil as it was the most used surface.
The precision inherent in the assembly of the cross-laminated timber walls and floors achieved a building envelope airtightness without the need for a further membrane. Simply taping the joints was enough to seal them.
Sandwiched between the structure and the buildings cladding system are batts of wood fibre insulation, in keeping with the all timber materiality, and for its great insulating properties.
Due to the benefits of a prefabricated structural system, all services within the slab had been pre-drilled in the factory. This not only made installing services incredibly fast and accurate, but it ensured superior visual quality to both the top and bottom of the slabs. Electrical conduits and cutouts for built-in downlights were integrated in the slabs/roof, as well as external walls.
Exterior
Blackbutt battens (40x40 mm) were used as the cladding, built over a batten and counter batten substructure. This creates an open cavity behind the cladding to ensure optimal ventilation of the facade.
Unfnished, rough sawn timber has been used to allow the facade to turn grey over time and not require any maintenance. The rough sawn timber maintains a rustic and natural aesthetic.
Timber cladding was chosen for its low carbon footprint, renewability, and the aesthetics of a naturally well ageing material with low maintenance.
Timber cladding also allowed the architecture to express externally what is the essence of this project. The cladding not only references the structural and internal materials, but also the exterior environment, surrounded by eucalyptus.
Tilt & turn timber windows were used, along with side hung and french timber glass doors. Spruce timber was used for external doors and windows, American white ash and Victorian ash were used for internal doors.
Triple glazed windows for all doors/windows to achieve best energy efficiency (U-value window 0.9)
Interior
The interior of the building features exposed CLT timber walls, floors and ceilings. In combination with the heat recovery ventilation system, this will ensure a healthy natural indoor environment.