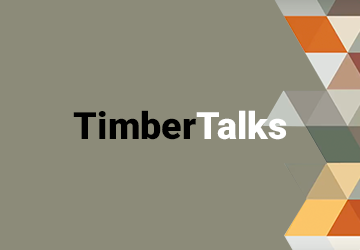
Upfront carbon is increasingly in the spotlight, as operational efficiency increases. Environmental Product Declarations (EPDs) are vital in measuring the impacts of the materials we use to arrive at the best design outcomes. Today we are speaking with Stephen Mitchell, Principal Consultant at thinkstep ANZ and Chair of EPD Australasia. In this episode we discuss:
• The exciting developments in materials on the road to carbon neutrality
• The life cycle of a timber product
• The opportunities that designers and the supply chain have for improved sustainability in design.
An environmental product declaration (EPD) is a standardised and verified way of quantifying the environmental impacts of a product based on a consistent set of rules that have been developed through an extensive stakeholder consultation process.
WoodSolutions EPDs can be downloaded free here
Timber Talks Series 3
Timber Talks is brought to you by Wood Solutions. Stay up to date with the latest in timber. The building material that is strong, safe, and sustainable. Here is your host Adam Jones.
Adam Jones
Upfront carbon is increasingly in the spotlight as operational efficiency increases. Environmental product declarations, ('EPDs'), are vital in measuring the impacts of the materials we use to arrive at the best design outcomes.
Today we're speaking with Steven Mitchell, who's the principal consultant at thinkstep-anz and chair of EPD Australasia. In this episode we discuss the exciting developments of materials on the road to carbon neutrality, the lifecycle of a timber product, and the opportunities that designers and the supply chain have for improved sustainability in design. I hope you enjoy listening to this as much as I did speaking to Steve. Without any further ado, we'll get into the first podcast of season three of Timber Talks.
Steven Mitchell
Up until recently, carbon emissions from heating, cooling, and running buildings, they're called operational emissions, they've been under the spotlight for 10, 15 years. That's mainly because a lot of data was showing operational emissions from heating and cooling a building are pretty high and they're quite easy to address. But as buildings became more energy efficient, a lot of work being done on installation, on LED lighting, and efficient air conditioning and heating, those emissions are coming down and it's all hands on deck when it comes to emissions.
Embodied emissions is the new frontier. There's a lot of data to show that as buildings become more energy efficient, and operational emissions come down, the proportion of emissions from building materials, or the upfront, or embodied carbon emissions, they get higher as a proportion of a building's carbon footprint.
The World Green Building Council released a report a few months ago on upfront carbon emissions. The Green Building Council of Australia have signalled they're going to recall our green rated buildings to reduce their upfront carbon emissions. It's a bit of a hot topic at the moment and I think it needs to be.
Adam Jones
In all of this I guess measuring is going to be one of the most important things going forward. Steve, can you tell us a little bit about what environmental product declarations are, better known as EPDs?
Steven Mitchell
EPDs is an acronym for environmental product declarations. They provide independently verified data about the environmental impact embodied in a product across its life cycle. That data includes the product's carbon footprint. In our whole building context, if the product's intending to be used have EPDs, and they meet that same standard, you can use the data, the quantifiable data, in those EPDs to evaluate a product's relative contribution to your building, or fill out project's total embodied carbon footprint. Much like strength properties, or stressed stress properties of structural pieces of timber, or data about durability, data about fire resistance, environmental or carbon footprint should be no different. You can use those numbers provided in an EPD to quantifiably come up with a carbon footprint of your building or project. That's where infrastructure people, people doing railways, people doing railway stations, train lines, services as well as whole buildings from housing and hospitals that can take all that data from an EPD and can suck it in. Using appropriate software, they can make those comparisons in a design sense to reduce the carbon impact of their building.
Adam Jones
Being a podcast on timber, we're inevitably going to look at the EPDs of a range of timber products. But before we go there, I'd love you to just touch on some of the other environments or developments that are happening with other structural products currently.
Steven Mitchell
My company thinkstep does all sorts of building materials. Obviously we worked on timber and we'll talk a bit more about that in a second, but we also do EPDs for steel, cement, aluminium fit-out products, wool. We've done a railway carriage. There's some really exciting developments in other materials. Everyone's on board with this carbon footprint message, and some of these other sectors are really making some good gains in this space. The world uses a lot of steel, a lot of cement and, aluminium. It's estimated that they admit about 15% of the world's carbon emissions from producing those materials and they have a huge impact.
It's steel. They're trying to reduce their carbon footprint. Making new steel from iron or with hydrogen instead of coking coal. Swedish and German companies are using a renewably sourced hydrogen instead of coal to provide the heat for that process. CSIRO, we've got a whole research and development project on using coal sourced from renewably sourced wood in place of coking coal. If and when they're successful, they'd better reduce the carbon footprint enormously. Also, making new steel from recovered scrap with electricity sourced from renewable energy. There are plants opening up in the States now where that's the sole source of electricity. Melting the scrap is from a solar and wind and battery combinations. Mr. Gupta in South Australia, that's his plan for the steel that he'll be making in South Australia as well.
The cement industry there got a huge technical challenge in making Portland cement, which inherently the process of making that emits a lot of carbon dioxide, but also other gases. Other gases makes it a bit hard to separate the CO2 from the process, but there's an Australian company, Calex. They're trialling a CO2 separation channel acknowledging the European union project which looks very promising, separating the CO2 from the other gases. What you do with the CO2 after it's isolated, it'll have to be buried and sequestered somehow, but that's a step that they are betting on will take place. Then the other big story in cement and concrete is the use of alternative cementitious materials such as coal, lash, and slag. That's a residue from steel manufacturing displacing the use of Portland cement in concrete products with these other cementitious materials. That can really result in lower carbon emissions for concrete. The EPDs we see on the Australasian EPD programme website for concrete and cement products, it makes a huge difference using those alternative cementitious materials instead of Portland cement to your building's carbon footprint.
Adam Jones
Let's look at the life cycle of an item or product. It begins with the forestry side of things. Can you start by telling us what happens here from a CO2 point of view at the very start of the life cycle?
Steven Mitchell
There's a great cartoon out there, which I'll send you a link to, but it illustrates that trees grow from the air, which is just a really mind bending thing, but there's plenty of science behind that. Those trees in the forest, or in the plantation, they're taking the CO2 in the air and they're combining that with water, and photosynthesis, obviously energy from the sun. They absorb the carbon dioxide. They converted it into carbon and they admit that oxygen, which goes back to into the air. They're storing that carbon they've taken from the CO2 in the wood itself. They're growing over 30, 40, 50 years. Softwood grows faster than hardwood. A forest or plantation, they're big carbon storers. Australia has got a pretty good handle on how much carbon is stored in these forests and plantations.
There's been a lot of research being done on that. The recent bush fires, it was a lot of science behind how much carbon was admitted from the forests that were burning, which is unfortunate. Very unfortunate. There is as much carbon stored in Australian timber plantations as is stored in Australian housing, if you can get your head around that. That carbon that's stored in the wood in a tree, we've got the equivalent or if not more of, a whole of Australia's plantation estate stored in Australian housing and building in the wood that's in these buildings. The amount of carbon stored in Australian native forests, only a small part of that is timber production area. It's 100,000 fold of the amount of carbon that's stored in Australia's native forest. Only a small amount of that is used in timber production. Obviously that goes in a warehouse or a building, and that's stored for a very long period of time. For most of its life it's very safe and protected from fires. It's in a very safe place.
Adam Jones
Tell us, Steve, a little bit about certification, and the importance of it being certified, and what this actually means. Then also some of the risks if you don't have a certified product.
Steven Mitchell
The word sustainability is actually an English translation of a German word, which I cannot pronounce. Sustainable forestry actually started in, strictly speaking, in Germany in the 1600s. There was a regional inspector of mines there. He was also responsible for forestry. He was responsible for the province's silver mines, which used a lot of timber. He wanted to make sure that he drew up some principles of sustainable forest management so he can ensure there was always going to be enough timber to supply the silver mines.
But sustainable certification itself didn't start in a broader sense until the Earth summit in Rio. I'm old enough to remember that back in 1992. It might be before your time Adam, I'm not sure.
Adam Jones
I was two years old, Steve.
Steven Mitchell
Two years old. Okay. I'm sure you were hanging by the TV at that stage. Watching Sesame Street switching over to the Earth summit.
That Earth summit back in 1990, there was a big push to protect, to stop deforestation. I think there was a huge push to stop deforestation that governments around the world said, "no, we're not doing anything because it will take away from our land. It's got nothing to do with you." So a group of people got together and they started a voluntary market based approach to improve forestry practises worldwide. From that developed the forest stewardship council or FSC. Just shortly after that, a European's game called Pan European Forest Certifications came and started PFC that's become now. Those voluntary market based approaches started up to certify the forests were managed sustainably and the forest and civil cultural practises were best practised. They took into consideration not just environmental issues but social issues and indigenous people's rights as well. That's the forest certification.
Then the other part of certification that developed was the chain of custody. How do you know that the wood you're buying is from a certified sustainably managed forest? That's where chain of custody certification came about. It's certifying each part of the supply chain like the forest, the saw mill, the wholesaler, the final product manufacturer. They have to be certified to those standards. Just saying they pass on the claim from the forest all the way to the end consumer. I'm an FSC and PFC China custody auditor. I go into these businesses and check their management systems and they're passing on a valid claim. Most Australian sourced software to native hardwood timber available on the market today is sourced from forests certified to FSC or the local PFC scheme called Responsible Wood. Most Australian producers and many importers are also chain of custody certified so they can supply your certified product on request.
When the trees grow in the forest or plantation, the CO2 is absorbed and carbon stored like we were saying. When they mature in say, thirty years in the case of Australian software plantations, the wood's harvested. A lot of that goes into long lived sawn timber products. Some of it gets emitted cause it gets burnt or used in short term products. After the harvest, the plantation is replanted. The next rotation of trees stores more carbon. This can go on indefinitely. If you've got a sustainably managed forest, you can indefinitely store bits of carbon. Sure some gets released when it gets harvested, but it grows again. You're storing that carbon in housing and buildings and back at the forest, that rotation can go on indefinitely. If you're wanting to invent a carbon sequestration machine, this is exactly what you'd do. No question here. Just add water. That's just mind-bending.
Adam Jones
So we've spoken a little bit about the forestry side. Moving now into the product phase, what happens here in the manufacturing of a timber product and where do most of the greenhouse gas emissions come from?
Steven Mitchell
When we develop the environmental product declarations, we looked at the whole life cycle from the forestry to the production phase. Those EPDs for sawn timber, sawn softwoods or hardwood, they're very similar sort of life cycle in the production of timber. Mostly the carbon emissions come from the kiln drying process. Your log comes in, it gets broken down, you sort into green timber, and then load it into a kiln pretty quickly if it's a soft wood. The hardwood might go out through a bit of air drying before it goes into a cure for drying. Then it gets dressed and then packaged for sale. Most of the carbon emissions come from that kiln drying process.That's what thinkstep found. That was the relatively big side. Emissions come from the kiln drying in the production side, drying the timber.
Probably not surprisingly, if you know anything about how factories run, but it's associated dust extraction and the electricity consumption there that can produce, that uses a fair bit of electricity and the missions associated with that, and that's obviously used to protect workers' health and safety, but about 70% of the thermal energy needed to dry Australian software, for example, comes from burning the sawdust. It's an efficient use of that resource. You're going to a handy fuel on hand and so 70% of our thermal engineering needs are from throwing that sawdust and they use a bit of natural gas to, if they're close to a source of natural gas. Soaring and dust, dust extraction, they use a lot of electricity and Australia's got such a dirty energy mix that that can be a significant emission from that process.
Adam Jones
Do you think there's an opportunity now for the supply chain to improve the environmental performance in the product phase so it's an even better environmental product?
Steven Mitchell
Absolutely. Following our study, that definitely helps focus people's attention to the people who contributed data on where their hotspots are, and that's a good thing about EPDs. You've got to do a life cycle assessment of the process and you come up with a hotspot. Where are the bigger energy users in your process? Manufacturers can use that information to improve their process. A lot of softwood manufacturers at the moment, they're investing a fair bit of money and better kiln technology. More efficient drying processes, high rotation sort of processes just to minimise transport, moving stuff in and out with forklifts. It's very energy intensive. That's really where a lot of gains can be made. People are putting on solar panels on their roofs using battery technology so that they're using more renewable energy in the sawmills and the Terras.
If you go out that way in the far North coast and new South Wales, you'll see the Terra Simba. Well, I don't know if the bypass goes past that now, but if you go into town you'll see the big solar panels all over his roof. People are becoming more sophisticated about reducing their energy needs and also making sure that their energy needs are met by renewable energy. When you actually measure the carbon footprint, you've got the forestry stage, your one cubic metre of softwood will store about 900 kilos of carbon dioxide, forestry pricing, kiln drying, and dressing. They consume about 200 kilos. If you add those two together, you get a negative 700 kilogrammes of carbon dioxide when the timbers are leaving the sawmill gate. You've got no other building product that can really boast that better than carbon neutral footprint. Having those numbers around there and having them independently verified gives people a lot of, well not only helps the manufacturer understand where the hotspots are, but it helps the end user understand what they've got.
Adam Jones
And the EPDs we're talking about can be found on the Wood Solutions website. There has been a lot of work into industry-wide EPDs so a standard understanding of what the environmental impacts are and looking at why made is cubed of kiln dried soft wood for example, like you were saying, there's minus 900 kilogrammes of a two sequestered per metres cubed in the forestry stage and then there is a number for haulage processing, kiln drawing being the highest at 87.3 kilogrammes, and planning and packaging. Finally, when we get to this point, there's four different choices or four different routes we can go down in terms of our environmental impacts and that is at the end of life phase. Can you tell us a little bit about what happens at the end of life phase and how design is my best approach? This part of the lifecycle?
Steven Mitchell
Those EPDs do include a few different options and that's an area of timber use that all end of life. That's an area of timber lifecycle that I think there's been a bit of misinformation about and new information. There's some new peer reviewed research which we refer to in those EPDs. When it comes to end of life, you've got reuse, recycling, renewable energy, or burial in a well managed landfill. Those are your options for your timber and often end of life options, are very locally based, which is why we've included each scenario. It can, because timbers hasn't used much energy to make, doesn't mean that end of life timber is not generally internationally traded. You've got to have a local solution because in terms of reuse or using salvage or recycled timber, you're prolonging the amount of time that the carbon stored in it is at above ground and not back in the air, so think longer term usage, the better.
Another option is shipping and recycling lower quality salvage timber. That can be a good option, particularly if it can be resolvable in a new particle board products. I'm helping aboard Polytech with doing that in Oberon in New South Wales and Dana Henderson. They make particle wall product in Victoria. They've been doing that for a few years with Polytech and just starting out on that. You can use very low quality recovered wood for thermal energy and electricity generation so you can burn it in place of fossil fuels and Laminex up in Queensland, they just received a half a million dollar grant to investigate the visibility of that. If you're not using coal or gas, you're not putting fossil fuel emissions into the air. But even burial in a well-managed landfill can have substantial benefits. That peer reviewed research I referred to earlier, that's found that the carbon in Australian wood and many other woods can just sit there in a well managed landfill over a very long period of time.
That's why when thinkstep did the EPDs, we included all those options, not just for Australian wood products, but for New Zealand wood products and Manufacturers Association. I've talked a lot about Australian timber products, but some of this can apply equally to some of our imported products.
Adam Jones
What about the designers? What can they do to minimise the impacts in their design?
Steven Mitchell
Ther'e a lot designers can do to minimise their impacts. There's design and structural optimization techniques. Like I was saying in the beginning, I think you asked me where are the impacts. We'll pay particular attention to the floor and flooring structure and what sort of materials you're using there and design for a structural optimization. That floor and floor structure actually that can be a really carbon intensive area and that's where big savings can be made. Using designing prefabrication can save a lot of waste and save a lot of time on site and you can really ramp up using low embodied materials in that sort of situation.
But one thing is knowing and measuring your building impact. Thinkstep works with Lendlease and other developers to do just that. We help them in a pre-designed stage, understand where the impacts are, and use the software to minimise the embodied contact, the embodied footprint of of a building. That's one of the reasons Lendlease is such a big supporter of timber and wood products, by the way, because they've done the numbers, they've used the EPDs to run the numbers for their structures. Sourcing sustainably harvested wood, we talked about FSC, PFC, Responsible Wood. Not all wood is good wood. Wood from land cleared to make agricultural land. Not all water is good. That's where the certifications of the source material can really help give comfort to you that you're doing the right thing, sourcing it from the right place.
One really important thing is ask for an EPD. By asking for an EPD and using that for products that you're supplied or potentially being supplied with your really driving that process of lifecycle assessment for a manufacturer and a supplier. They have to look at their supply chain and how they can minimise their impact. An EPD is just a summary of the impact of their material. But what really drives that improvement stage at the supplier's end is often they actually don't realise themselves what the impact is of their product at different stages. They don't measure it necessarily, but an LCA and an EPD makes them measure where it is. As a designer and a specifier, one thing that people can do is ask for an EPD. Might be a little thing, it's not going to cost you anything itself, but that can be a big signal to the market to drive improvements and induce change in the carbon footprint of building materials. You can look for those EPDs on the EPDs Australasia website or the thinkEPD.com website that things are just set up or get in touch with me if you want to know more detail.
Adam Jones
An environmental product declaration, EPD, is a standardised and verified way of quantifying the environmental impacts of our product base on a consistent set of rules that have been developed through an extensive stakeholder consultation process. What solutions have conducted industry-wide EPDs, and you'll be able to find these on the website at woodsolutions.com.AU/articles/environmental-product-declarations.