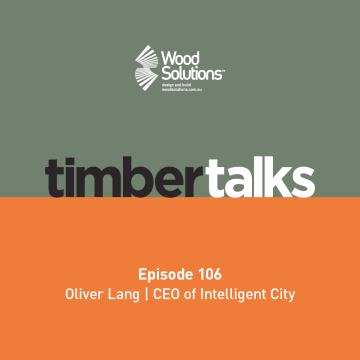
In this episode of Timber Talks, we're speaking with Oliver Lang CEO of Intelligent City about the future of construction and building. We'll be discussing the vision behind Oliver's work, the key technological advances being used today with a focus on robotics, the process of construction and how it differs from conventional methods, the hurdles to adoption of this new way of doing things, the balance between standardisation and flexibility. Finally, we dive into where Oliver sees the industry heading in the next 5 years and Oliver will share his knowledge and insights on these critical topics and provide a unique perspective on the future of construction and building. This is a must-listen for anyone interested in the future of sustainable construction and building.
Timber Talks Series 6
Series six of WoodSolutions Timber Talks, provides the latest informative and entertaining information about the best design practices, latest innovations and interesting case studies and interviews with world leading experts in timber design, specification and construction.
Adam Jones (00:07):
Today we're speaking with Oliver Lang, CEO of Intelligent City, about the future of construction and building. We'll be discussing the vision behind Oliver's work, the key technological advances being used today with a special focus on robotics, the process of construction and how it differs from conventional methods and also the hurdles to adoption of this new way of doing things only. We're going to see Oliver's vision for where the hell things are heading in the next five years and get his unique perspective on the future of construction and building. Now, this is a must-listen for anyone in this space with the evolving future, what we have around productization and standardization and the general future of timber construction. So without any further ado, here is my conversation with Oliver.
(01:02):
Thanks for coming on the podcast. Oliver, can you start by telling us a little bit about yourself intelligent city and what your overall vision is and what you're trying to work on?
Oliver Lang (01:11):
Yeah, thanks so much for having me on your podcast. So my name is Oliver Lang. I'm the co-founder and CEO of Intelligent City. We're based in Vancouver, Canada. We grew out of an architectural firm that we started almost 25 years ago realizing a need in our industry to come up with an integrated approach to really rethink how we deliver, how we design, engineer, and deliver buildings to get to a product that we think really addresses some major issues and problems in our industry and hopefully provides a path to just much better way of urban living. That was the vision when we started. We wanted to, from the beginning when we initiated the thinking, that's about 15 years ago, very much focused on making sure that our product that we can deliver is all about environmental issues and really get us to solutions that can be carbon neutral and have a model and a repeatable and scalable model to address the major housing issues that are in the world around choice, supply, quality, affordability.
(02:29):
So really bringing these two things together, trying to address housing issues and getting us towards a path of carbon neutrality that motivated us and we realized that what was missing in the industry was a path towards deep integration of design, engineering and use of advanced technologies. So we've been pioneering the use of advanced software technology of robotics, but also of the use of mass timber technology that we can apply for midrise urban housing, which is really our target. So how do we densify cities smartly for resilient communities using a product that comes from a renewable resource and then apply advanced technologies to that product so that we can have at an end product that people could really wholeheartedly embrace and it works well to smartly densify urban environments. So that's the motivation. So that set, we're really, by definition we're a housing technology company that takes a product and platform-based approach and we're seamlessly integrated, as I mentioned, like advanced software robotics and mass timber building systems for quality or run housing that can be built faster, more affordably and consistently carbon neutral. So that's sort of in a nutshell the vision.
Adam Jones (03:53):
Yeah, well that's phenomenal. That's so exciting. I mean there's a lot of layers to everything you said there, but it might just pick one of them. Firstly, on software. So what sort of software are you using in your I guess, end-to-end solution that you've come up with?
Oliver Lang (04:08):
Yeah, so we have basically in the entrance solution, we have different aspects of software that we've developed on the front end. The software allows us to go quickly through iterations of design, but always on the basis of and full understanding of the entire systems that are underlying it. So the software has co-evolved with the design of building system of the manufacturing systems, building databases around everything. So when we go through a front-end modeling with the client in the early stages of a building, we can immediately have a live read-out around environmental performance data about carbon footprint and energy needs. We can get a read-out about the number of homes, the mix of homes that you can have in a building, the overall size, the density yield on a building, but also qualitative aspects about livability, access to daylight ventilation issues, and so forth. So all of this has been basically parametrized to inform buildings from the front-end so you can rapidly iterate through the design versions and sweet spot this so that clients don't run through this risky process and not knowing what they might get, but rather actually show them and demonstrate to them what the kind of the right response would be for their building, for their objectives on that particular site based on the use and the knowledge that we have through our componentry.
(05:37):
So the software is can't be thought of not existing directly in correlation with everything else. So that's the front end. Then we have this sort of the mid-section of the software. It's all about having a software reporting out and being collaborative in the industry. So, and that software is completely proprietary. We built that in-house, but it can link into what people do. So we collaborate with structural engineers trades manufacturers and so forth of other parts that we don't manufacture ourselves. And so the BIM compliance issues and being able to connect and collaborate with partners in the industry is very important. And then we have the back-end of the software sorry, and it's the main of software has also a deep level of database integration so that we can control everything. We always know quantities and carbon and all these things energy performance. And then the back end of the software is then we take that model and we can read it out directly into the manufacturing automation. So the software generates the robot code so that we can manufacture our systems that we have.
Adam Jones (06:47):
I feel like that does sound quite different because there has been others plays in the past who've tried an end-to-end solution. How is it different to other plays in the past? And it might sound like you're an emergent sort of strategy you're playing where you're connecting with others. So can you tell us a little bit about that, how you're going to evolve with this ecosystem?
Oliver Lang (07:07):
Yeah, so I mean the key thing for us was we didn't want to build a piece of software that's sort of like a black box for broadest usage. We used to set, we want to have something that's extremely streamlined around the kind of buildings that we want to do and we want to enable all the integration that is necessary. So we're constantly asking ourselves how can we make things simpler, more efficient, less complex, while having access to all the critically important data and make that data really robust. So as I said, I think what's really different is that we are not a software company. Our software is just part of a technology ecosystem that is constantly integrated over and over again. We're recycling back and forth from design, engineering to building systems to manufacturing automation into software back through the process and so forth. So all these technology parts co-evolved with each other and couldn't in fact exist without each other.
Adam Jones (08:09):
Yeah, that's so cool. So you've the end-to-end got robotics, and I've people listening right now, audio only, I've seen a presentation of yours and it's insanely impressive and exciting, the robotics and the manufacturing. Can you tell us about that end to the solution and how might that be different with the advantages that you've got because you're one step below the supply chain compared to say suppliers, which is supplying the material only and how you're doing that side differently.
Oliver Lang (08:37):
So we chose or we decided we would go on the side of robotics for some obvious reasons, which is that you know, you can have repeatable processes execute fast. So it's definitely again on time there, that's very, very important. Equally important is the possibility of quality control that you need to do when you come up with your own building systems. And we have, so our building systems are now certified for North American markets to have fire resistance. We're like the first that have basically a robotically assembled building system that you can build up to 18-storeys tall and it'll be fire resistant to get there. You can't just think that you take a few pieces of mass timber and nail and glue them together. You have to put them together in ways that are completely controllable. And that's where the robotics come in, where we basically run the protocols in such way that we know that the fryer resistance is always insured, that the acoustic performance always insured.
(09:43):
We also maybe just to digress for a moment. We are manufacture, for understanding, we manufacture the superstructure of the building. So all the floor slaps, it's a hollow core cassette system that we can make in really large proportions and a building envelope system also based on mass timber that always meets passive house requirements. So we have two robotic cells in the factory, one makes building envelope and makes super structured components. And then we have a robotic milling center that takes basically raw CLT that we can buy off the global market and mills it to complete our specification and precision just in time for then the assembly of the manufacturing of these large scale components. So speed matters, quality control to an even enable the half systems of this kind that can perform this consistently matters. And thirdly, adaptability matters because the beauty of a robotic execution code is that it can vary. So within a certain parameter space and design space it's not rigid as a jig. It actually can execute the same path, let's say, but to create a different underlying geometry or feature set. So that gives us really the fundamentals that we need is repeatability, robustness, quality control, adaptability, and speed. So that's what mattered for us when we decide on robotics. And so now we spent many, many years to develop all the surrounding technologies to make sure it's functional.
Adam Jones (11:20):
What are the sort of hurdles to adoption or non-negotiables in your way of designing data in traditional construction to make this workflow work? Or just maybe it is a slightly different question, but what are the sort of hurdles to adoption right now of what you're going through?
Oliver Lang (11:38):
Yeah, there are many, right? I mean when you really change the model, and we are right, I mean just to be clear, we're going from a service-based industry to a product-based industry. And when you really take that to heart, it means we're not doing the typical design build process. But we're rather saying people can come to us and they can order a building from us and we integrate with our clients and their needs as much as we can. But the net effect is that you can't delay questions about component design and procurement until the very end and see the lowest bidder is that just doesn't work when you productize and industrialize our industry, which is when you use something like mass timber, you almost have no choice. But because it's not a material that's very forgiving to change it on site, you have large scale components that need to be precision manufactured and essentially just as assembled.
(12:33):
So that means you're brave to bring the team together from the beginning. And so one of the big hurdles is in the way how the industry right now works is the procurement processes everywhere are still in the old model that you do basically a late tender to a lower spitter and that just needs to change where you basically have an early tender and qualify the participating parties as a team that can deliver buildings. And that's a massive hurdle because our industry is deeply entrenched in its ways and it changes the way how even the players participate, architect structural engineers, builders, et cetera. So everybody around us needs to, that want to participate with us, need to also change and adapt their business models because yes, we can provide them with far more scale in what they want to do, but their typical ways also don't work anymore.
(13:30):
So you have to change the mentality, you have to change the business models and that takes time and it's a significant effort to do so. Secondly, it's the regulatory framework of course, fortunately in North America that's come around finally. So we're allowed now to do mid and high-rise up to 18-storey timber buildings in North America and there's a regulatory framework. So that gives us a lot of certainty in a way that we actually never had before which is great that you have sort of almost a unified building code around high-rise mass timber and a building science. So that's definitely gone from a major hurdle to an enabler, which is great. And I think it's sort of mindset like risk tolerance, it's new, it's different. And so people think, okay, is it more risky because haven't seen a lot of mass timber buildings, they haven't seen buildings that come out of factory of parts that are assembled by robotics and they need to get comfortable with it. So whenever you introduce a change, a technological change, a design change in an industry that's truly disruptive, obviously everybody says how many buildings have you built? And our answer to that is we've built a few, but really we spent most of the time right now to get everything to ramp up the factory, to get the testing done, to get the component definitions done, to make through a that we have a really robust solution. So these are hurdles. It's typical for I think when you have introduce a change into an very entrenched industry.
Adam Jones (15:10):
Well it sounds like because you've gone the product route, it's like the Honda of the manufacturer of the first car. There's a lot more effort and time that goes into the product, which can be scaled up millions of times. And it sounds like you've done that process and now you're at the position potentially where you can scale it out, the productization you've done to a lot of buildings. Is that the way you see it?
Oliver Lang (15:32):
Yeah, that's I, there are other industries that you could cite where that's happening, where you see a fundamental shift in how products are designed, see designed and manufactured and then delivered out in the market. And it just takes a few years to get everything ready for it.
Adam Jones (15:55):
Yeah, that's so cool. One of the issues in construction, of course, is the changing costs and the uncertainty around that and it blows out and everyone starts pointing fingers. Do you offer or is a plan to offer cost certainty from the very start to like a buy now with certainty in delivery and costs and everything like that?
Oliver Lang (16:12):
Yeah, totally. I think that's the advance that we have is because, through our software for example, we can quantify within a matter of days or weeks where others may take month and month. We can come back to a client saying this is exactly how much timbers in the building, this is how much insulation in the buildings is how many windows and so forth. So not only get when you have a good definition of geometry and physics of a building, you get good quantity that reads out in carbon, that reads out in cost and so forth. And so you can apply rates to it. And so we can provide much more certainty to this. I think the realization that we have is really that we have to even go further because with what's happening in the world right now with inflation and so forth, the remaining part of onsite construction is still seeing a lot of inflation. But what our parts have been, at least our components have been very cost stable even over the last two, three years. So to answer your question, yes, you can provide far more guidance and cost certainty from the get-go because of the level of integration that we can offer.
Adam Jones (17:27):
One of the things that seems critical is the standardization and the benefits of that, but then you've, for the devil's advocate had, it's around the maintaining architectural flexibility and some sort of creativity in design and like that. So how do you see managing those two could arguably competing interests or how do you handle that?
Oliver Lang (17:49):
No, I think it's an excellent question because when we started out, we looked of course into the history of prefabrication and what's been done and prefabrication is not new. People have done modular buildings over a hundred years ago, but they never really took hold. And I think from our analysis, what's shown is we have an industry right now that builds predominantly bespoke buildings. It's a one-off, right? And it's a complete custom and that has all, its maybe, somewhat benefits, but really mostly disadvantages in cost escalation and all. Basically, every building is a prototype that's really mind-numbing to some extent that we really not haven't learned. On the other end, we have seen prefabrication and it became sort of like the one-fits-all right and complete normative in a way, like stacking boxes, volumetric, prefab and so forth. That works for some projects but the vast majority doesn't work for, because the demographic needs are different.
(18:53):
The needs on a particular location and a particular site in cities in Melbourne might be different from Vancouver, but they're also equally similarities. Housing is housing, we all have something that we call home. We like connection to the outdoors and so forth. So we identified where there are similarities and where we need a degree of flexibility that allowed to a creation of resilient communities and something that people can really identify with and that works within the scale of development. And that creates sort of the design space in which we have to have required flexibility. So, you know, we want to be simple and efficient and create a beautiful product, but we also need enough adaptability. And so we went back and forth, and this is sort of where this combination of technology is very powerful because in software you can design everything parametrically, which we've done. So we can go in and saying, let's change the unit mix, the depth exchange, the window ratios, exchange the widths of a home that the livability issues the right, the adaptability over time, the connection into outdoor and so forth, parametize all that while always ensuring it's manufacturable.
(20:06):
And on the other end, you've got the robotics, and as I previously mentioned, when you manufacture something that I've tested and okay, I know what my structural spans are that I can maximum achieve, but I can make it a little narrow, I can make it a little longer. I can have a longer span, a lesser span, so forth. I can set systems here and there. I have a design space in which I can flex and there's enough there that you can now manufacture or we can manufacture basically a whole range of buildings from four to 18 stores, from rental to condominiums, from commercial users all the way through office users to residential users, all from the same manufacturing lines based on fully tested and certified components. So the flexibility, the adaptability, or the mass customizability has been built into the technology ecosystem from day one.
Adam Jones (21:00):
That's so cool. Where do you see the puck going in the next five years with all these new technologies, and not just intelligent city, but the whole ecosystem in general?
Oliver Lang (21:09):
Great question. I would say what we recognize or what we realize in, at least in Canada right now we have a major housing crisis right now. We have a major global crisis in financing, inflation cost and so forth. And we have a climate change, major climate change issue in the world. So when you put them all together what's happening is that maybe five years ago, responses have been, let's say aspirational at best. What's happening now is that regulation is changing very rapidly, that in many jurisdictions in Canada, basically you have to now demonstrate that buildings are lifecycle carbon neutral. And that's very, very difficult to achieve with the typical forms of concrete construction and low-performing buildings with a lot of thermal bridging and low insulation values and so forth. So the performance requirements, the environmental issues are required to really improve substantially while at the same time, where's the funding come right now housing needs to be built, the cities have no choice.
(22:15):
So a lot of it is now funded through federal funding, provincial fundings, et cetera, and housing programs into rental. So I think a lot will go into buildings that are about rental that have a really good life cycle performance, that have to demonstrate far more longevity with low maintenance costs, low operating costs, not buildings that last 30 years need to get demolished. You have a massive loss of capital if you have to rebuild your buildings every 30 years. So buildings need to be flexible. They need to ensure resilient communities, they need to be carbon neutral and at the same time cost-effective. And I think that's the driver right now, not just for what we do and what we got ourselves ready for, but I think we're where our industry sort of inevitably has to go because these are the problems that we need to solve collectively.
Adam Jones (23:03):
Yeah, that's a phenomenal answer. Well, it's been great being able to speak to you. All of those people want to find out more about yourself and what you've been working on. Where should I go?
Oliver Lang (23:12):
Well, you can come to our website at intelligence-city.com and there's a lot of information there. And of course, by all means always, if anybody's interested you've got an interesting project to work with or you want to collaborate with us in any forum then yeah, please reach out to us. It's all the information on our website and we're looking forward to being active in many parts of the world. And if there is a great project somebody wants to realize in Melbourne, we'd love to participate.
Adam Jones (23:46):
Fantastic. Thank you so much, Oliver. I'll leave it there.
Oliver Lang (23:48):
Okay. Thank you very much for having me.