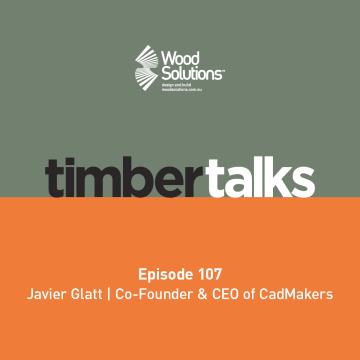
In this episode of Timber Talks, we're speaking with Javier Glatt, the founder of Cadmakers about the future of construction documentation. We delve into the issues with traditional documentation processes and how software can offer a solution. We also discuss the evolution of the digital ecosystem in construction and how new technologies are changing the game. Javier will share his thoughts on what can be automated in the construction process, the future of BIM modeling and its impact on offsite construction, and much more. Get ready for an informative and engaging conversation on the future of construction documentation.
Timber Talks Series 6
Series six of WoodSolutions Timber Talks, provides the latest informative and entertaining information about the best design practices, latest innovations and interesting case studies and interviews with world leading experts in timber design, specification and construction.
Adam Jones (00:11):
Gotcha. Well thanks so much for coming on the podcast, Javier. Can you start by telling us a little bit about yourself and what you do at CAD Makers?
Javier Glatt (00:20):
Sure. So, I'm a co-founder here at CAD Maker. So we started the company friend of mine from business school nine years ago. And so at first we started doing digital construction and then services bringing scripting and automation and kind high-end model modeling to construction. So we recruited heavily outside of construction, brought them into construction ecosystem, worked on construction projects and then we've kind of grown and evolved over the years from there. And about four years ago we started reinvesting every penny we could get out of the company into building a product suite which has evolved into basically one main product we're focused on at the moment, cmBuilder.io. So cmBuilder.io is a web-based construction planning and simulation product. So the idea is it's really making it very easy for, so non-software technical folks like project planners, site managers, preconstruction, and of course the BIM, VDC folks to be able to do 3D site logistics and 40 simulation in a much simpler, faster way.
(01:26):
So, we work a lot on that. So we have a service business that's working on a number of projects around the world and we learn a lot from those projects. And then we try to do it best to take those learnings and turn 'em into tools, automation, templates, processes that we can continue to get better each day. And then also learning on how we can build specific products like SaaS products that can solve other problems for our customers. It's all the same target customer construction industry but just the way we go about solving the problem for the customer may change from a service versus a product depending on what the customer needs. So that's the high level. We're based in Vancouver, Canada and do projects all over the world and a Mass Timber podcast. We do a lot of mass timber work. It's one of our big focus areas at the moment or I guess through the last four or five years. And we're really excited about mass timber in general and kind of turning construction sites into manufacturing problems to be solved which is really exciting. So yeah, that's the short cause notes on us.
Adam Jones (02:27):
Yeah, no, that's really cool. So what are some of the problems, you mentioned before traditional construction problems that you've already been able to solve through some of your SaaS products and what are the other sort of problems around that space, which are you're currently solving on and are most exciting for you?
Javier Glatt (02:44):
Yeah, so I guess I'll just highlight a couple for our services business and when it comes to mass timber specifically it's a fairly new thing in the world in terms of just like, you know, mentioned even with what you're working on, there's not a lot of historical data that you can leverage like a concrete and steel structure system. Structural systems architects need to design in different ways. They're used to maybe designing till the last possible second. And even the joke is build design, not design build. You're still, you're building and you're still designing as you go. And when you work on a mass never project, you know, have to freeze those things a lot earlier which I know you know well, you're well aware, I'm sure your audience is well aware of. So that introduces some challenges, this understanding, what kind of systems are being selected earlier, what's the design and manufacturing assembly type of considerations that need to be taken into when you're designing these things.
(03:37):
For example, we worked on a 26-storey mass timber project where the every structural system, every floor as you go up the tower, the column sizes changed and at first you're like it, doesn't seem like that big of a deal, but because the column sizes were changing every time, the connections are changing on every single floor almost, right? And because of that, it just adds way more machining operations, more typical, not the typical details explode. So you need to have smart parametric automated ways to manage those types of changes in the information and data and manufacturing, the end manufactured product. So those are things that we're pretty good at just understanding how to model those things, how to model them in an automated way, how to give information that can be fabricated from and that's coordinated and works with the rest of the building systems. So we have a kind of team of engineers that just do this all day long.
(04:30):
So that's a big area we focus on. So, things like airports and big complicated projects. Typically we work on large projects where they need larger teams to be able to spun up in a short period of time and deliver a lot of work in a short period of time. High complexity. So yeah, that's what we focus on there. And then on our product side, some problems are like 98% of the world when it comes to site logistics and planning projects is in 2D still. There may be some nice-looking animations as part of a pursuit, but generally speaking, the actual planning is more even the best companies in the world that are most BIM and VDC focused. This piece, this site logistics piece is kind of over here because it requires a lot of knowledge and know-how from the folks who build the project in real life it's kind of standalone crane location, location, traffic management.
(05:18):
Do you have to retain trees? Are you going to remove trees? Are you going to replant trees? How are you getting access to the site? Are you going to have to have occupancy phasing structures? So you have to build over here, while there's people over there, and there's safety considerations. So all those things are pretty much there's not great technology being used to solve them. There is some legacy products in the market, but generally they're quite expensive and quite complicated. So, people default back to 2D. So we make I mean zoom builder to make it really simple for people to give up to model those things in 3D drag and drop fully parametric to see really easy to do and running on the web. They can work from anywhere, they can work on their data anywhere and share work multiplayer mode, all these kind of things that drive collaboration at a higher level. So there's a few problems we come across over the years and we try to build solutions for them and that's kind of how we scaled out the business.
Adam Jones (06:10):
Yeah, great. So, were you referring to the ascent building? Was that the 24-storey?
Javier Glatt (06:15):
Yes, yes.
Adam Jones (06:17):
Yeah. Great. So what sort of design automation can you assist within a project like that? So what sort of ways did you get involved?
Javier Glatt (06:26):
So we don't typically get that much involved in design. We are kind of really, we do fabrication design assistance but typically don't other than coordination and overall constructability, we don't really comment or get too involved in design per se. We're trying to take the design information, which often in these projects back to a problem is design intent. This is typically an intent and then a lot of the challenges of how to build it gets put onto to say the sub subtrades or the A fabricator which comes in much later. So there's a gap there between the two. And so things that we'll do is somewhat soft, some software related register, smart ways to manage changes and complexity of models and trying to pretty very precise with how we work and using a lot of code to generate things as opposed to manually modeling things as much as possible.
(07:18):
So that's helpful. But also some of it's just over the years it's learning knowledge, understanding. Where work with a lot of the major suppliers around the world who understand what kind of data they need and what format and how they're going to nest panels from billet are they're going to nest through the transportation nesting to send material around the world. Worked on a project in Singapore, really large project where we hag was sending stuff from Europe and understanding how to pack the containers and glam and these things is pretty complicated. So we built a number of genetic algorithms that help solve for those things since we can embed those in our services to help add value to projects. So those types of things, it's mostly like what's the problem, what's an appropriate way to solve that problem? Can we leverage some stuff we've done in the past already? We call it back some background IP that we have, that's great. If not, we might have to build something new to solve this problem depending on what it is that we're trying to accomplish.
Adam Jones (08:13):
And to be honest, it's actually for people listening to podcast for a while now, that'd probably, there's a couple of things that come up all the time. One is around moisture and site and all that sort of stuff. The other is exactly what you're talking about there. It's that gap between what the structural engineer documentation process is usually like and then what the supplier and the manufacturer needs. And then there's a big gap and a scope gap and even and turns out to be the critical path for projects and where all the issues come is, is getting to that, the design side of a structural engineer to the point of nesting and building. So yeah, can you elaborate a bit further on how that process, what it is now and how that can be improved?
Javier Glatt (08:57):
Yeah, so I mean, what I've kind of come to learn is there's these amazing, especially mass timber, there's these amazing master builder long-term carpenters that are experts in their field, especially in Europe you have a lot of these kinds of ecosystem of folks that work. Carpenters that go do their master's in structural engineering, they have practical knowledge, they understand would they understand timber and then they typically either go on the structural engineering consulting side or they go work for the fabricator. And there's just specifically because of procurement models and how projects are actually delivered, there's often kind of a conflict between the two. You have a structural engineer that's tasked with design and making sure it doesn't fall over and it's solving for some of those wind loads and moisture. Actually, moisture is a big one where we are in Vancouver, Canada because it rains a lot and for example there's, there's a lot of, we had a project, the first ever big project we did was called Brock Commons here in Vancouver where it was pretty amazing project to be a part of.
(09:55):
And there's a joint architect named Herman Kaufman, he's out of Austria I believe. And he was in our office, we're having this talk and he was going through the model, he was just pointing out where all the areas, the water's going to pool based on the system, the assemblies and how things come together. And he is like, that's where the risk is. Mold and moisture, content of wood and understanding, okay well if that's the case then what's the manufacturing constraints that can go into this edge gluing versus non edge gluing for example of panels. So some of the European providers will edge glue the CLT panels and then press the panels. Some North American won't, right? So if they're not, then the way the moisture is either going to get through the panels or not is a consideration. And all that knowledge that goes into that is often in the heads of a few specialists that are out there swinging around in the world and they're usually getting involved in some of these projects and sometimes they're not.
(10:51):
What we're trying to do is say, well how can we embed as much as we can of that inside code, inside templates, inside in a more scalable way to learn from those things and then be able to apply them on the next incremental project without having to have one or two people will be relied on to know everything. So yeah, those are just some examples but CNC time, pre-print, like pre-cutting holes for piping let's say. Right? So you got a panel, do you see and see all the openings on the panel before they come to site? Or do you try to cut it on site? Well that's a big, actually, Kai in our team could probably give you all the calculations. It's usually yes but it's a depends question actually. It depends. If it's three-ply CLT and you can actually cut it decently, there's a lot of upfront coordination and work that goes into making sure that you can print pre-CNC panels with all the openings for shafts for duct work and piping and stuff like that.
(11:47):
And there's more time on the tools. You have more CNC time, which is generally the bottleneck of every factory for CNC, for mass timbers, the CNC. So you're trying to remove the amount of time you need per panel on the CNC, so you're adding more time so you better make sure you're saving a lot on-site when you do these things. So there's all these kind of things that you got to consider when you're in that kind of design to fabrication, manufacturing, assembly, kind of dfma discussion that can be done by software. It's also just done by experience and understanding where it's the best place to apply these kind of tools and templates.
Adam Jones (12:22):
Yeah. Cause I used to work for a CLT manufacturer and the pricing model's pretty difficult because you're trying to balance a lot of things. You got the material feedstock price and then it's hard to model exactly how a panel's going to go through a factory and how to price it properly. And because there's uncertainty there probably increases going forward, but if you've got that solved from the very start, exactly how fast it's going to flow through and what a volume per shift can be pumped out of a factory. I mean that can really drive the cost down I'd imagine. What do you reckon?
Javier Glatt (12:55):
Yeah, so that's a great insight and what I've learned, and I'm not on involved in every project anymore, but one thing I'll say is, so you work for fabricator, how does a fabricator make money? They make money by ship and panels like turning raw materials into finished products and sending them, maybe not even installing them, they might just be producing panels and generally speaking their utilization rate drives their business. How utilized are their fixed assets? So can, as you're an owner, if you're an architect and you want to work with some of these big players, they're quite happy to be delivered a very accurate detailed model with bill materials and information to be able to just produce because that shop drawing time, that modeling time, they're going to make some money from that. But it's typically not the core business. It's typically not what keeps the lights on.
(13:45):
And to your point, it's an extremely volatile risky business. A couple years ago here in North America, there's a massive spike in timber prices and all of a sudden, you know, you need raw lumber, you need lumber to go into be panels. And so how do you hedge that? And that's beyond my pay grade. I'm sure there's futures contracts and different things to understand, but generally speaking with all that, how do you de-risk things, right? De-risking means better information, the ability to convert machine code run on the machine, CNC parts that make sense that are shipped and packed in a container in the most efficient way. Maybe there's the lifting of those panels is into consideration. One project, we had a script that would calculate the center of gravity of each panel and just put a little code in the inside of the G code. They add a little bit where the grooves would be for the lifting logs, lifting and where they could just lift the panels flat.
(14:36):
So, depending on what the panel looked like, if it's an edge panel, it's cornered, it's got an opening for a duct, the center of gravity could dramatically change. So the idea of just being able to rig that panel quickly and safely, fly it up flat and bring it in is super valuable. So those types of things, especially if they're on the installation side of that whole equation, it's going to save them labor, it's going to save them time, it's going to allow them to make little more projects. So generally speaking, these are very difficult businesses to run and better information that can be delivered faster and more efficiently is going to be a big driver in terms of keeping that CNC running and keeping that raw material being turning into panels and shipped out the door.
Adam Jones (15:15):
Yeah. Oh, that's so good. What are the overall new technologies that you see coming in which is going to, you know, might be jumping on the back of but it sort of moving the industry forward in this direction?
Javier Glatt (15:26):
I see lots of interesting, seems like everyone's working on kind of a kit of parts based dfma based, generative design solutions that can say, hey, based on a standard kit of parts here, let's generate a bunch of different options that an architect designer can choose from. And I think that's all very helpful to work through the early phases of the design phase. I think downstream there's a lot of work that needs to be done in the industry at large to standardize things, which is hard. This is a really hard problem to solve. And what we see a lot is a design team who are amazing and they've done a pretty good job to rationalize the design down to something that's fairly optimized and they had, oh, it's only going to be 10 types. And then you start working on it, you're like, well there's a bulkhead over here and there's a notch in the panel now that's another type and over here you're going to need to have use a pre-engineered, we changed the pre-engineered connection so we're going to change the way of the end style of that PA beam's going to be.
(16:34):
So, there's a new type. So it's just so hard to have only a few types really when you get into manufacturing terms. And so I think anything that can help streamline the design phase into detail, the schematic into detailed design phase with machine operations and different types of machine code type of implications built into it nesting and these types of optimization things and they can go from design to fabrication in a seamless way is really valuable. Seeing a lot of people try it both on the software side or the process side criteria as famously tried to carbonate integrate to do some of these things. And I think without seeing a little bit of that close up front, it's just extremely hard. It's extremely hard to completely verticalize the whole building process and I'm not even sure necessarily it's the right thing to do. I think most people have come where, okay, well that maybe that's not the right thing to do.
(17:27):
I think there's a lot of amazing people there trying to build stuff that know, knock on that. I think it's just extremely difficult to do what they were trying to do. So then you see what I've seen is the pendulum swung way over here was like, okay, we're just going to have different parts and we're just going to click them together from a supply chain and everyone's going to have their own parts and it's going to come together. Also extremely difficult to do <laugh>, so somewhere in the middle it's probably where we're going to land. And I've seen some really interesting stuff lately with using CLT for vertical here walls. I'm not a structural engineer like yourself, so I'm not going to speak too much out of school here, but before I was always panels, okay, maybe a core you might do in CLT or maybe you do some other solution for the core.
(18:10):
Now we're starting to see a lot of vertical walls, shear walls being CLT as well or panelized as well. If you see the exterior facade, CLT panels is some people have been working on that obviously lot has its own challenges and generally speaking, I can see incrementally that we're marching towards the middle ground between let's do everything in one place versus let's have everyone do their own things and magically it's all going to click together. And somewhere in the middle where you have, let's automate the systems that make sense to be automated and vertically integrate the systems that make sense to be vertically integrated and then have a middle ground solution where you say maybe the MAP contractors got racks and they got different types of prefabricated solutions, maybe running things through corridors and stuff like that which there's a lot of great people in this market.
(19:00):
Pit meadows plumbing is doing a lot of interesting stuff. So I think it's software, it's process, it's understanding of mass timber just generally speaking, getting better. When we started five years, it was only five years ago. I mean the owner would be like oh, we're doing a five-storey rental building, let's just turn it to mass timber. Yeah. And the structure, the early the OGs of structural engineering for mass timber in this market, it's the fast and eps and the equilibriums and those folks were kind of like you can't just change the whole thing. This is not how it works. You have to design the building from scratch to think this way. And I think people are starting to understand that it's its own thing. It needs to be treated like differently than your normal cast in place, concrete project or in your neck of the woods.
(19:49):
There's a lot of precast. It's going to, I guess closer to pre-cast actually in terms of lots of planning upfront, freezing design and advance, getting your supply chain in check, understand. We had a project in California, it was massive project at the time, it was the biggest in the world. I think it's now been built by a few others that we were involved with luckily. But they had to prefabricate six months in advance the CLT panels to store them on site just because once the assembly process started kicking in, they couldn't keep up the production couldn't keep up with the assembly process because it's so fast once on site. So, this takes a tremendous amount of plan. So you got to freeze the whole thing. You're in advance, right? Yeah. Know this is not normally what people do in construction. So I think I've seen a lot of really interesting steps taken by the industry to understand what mass timber is different.
(20:36):
The owners need to understand that it's different, the economics are different, everything's different about it. And you can't just put a square peg in a round hole and say like, oh, we were going to do a concrete tower building, we'll just turn it to timber. Should just be, you can do that, right? Oh, you're good space and changes now what type of build? There's things that make the project work. And so technology process and understanding I think are the big, I know you're working on some knowledge-based type stuff. That's another thing. There's just people getting a good understanding, knowledge-based reports coming out as PhD reports that are publishing data on what people are learning. These things are critical to streaming port.
Adam Jones (21:12):
Yeah. I didn't realize, have you, you've mentioned, so I didn't real, you've been part of Brock Commons NTU Ascent and was same before this episode. You're part of the early Lendlease projects as well. Is that right?
Javier Glatt (21:24):
Yeah, we've been fortunate. One of the coolest ones is the Portland PDX airport. It was, it's more recent ones, pretty incredible engineering feat how encourage everyone to go look that up. They basically built like a football fields, American football field size cassettes, they called them that were basically the whole roof assemblies and they just, there's like 20 of them and they moved them in the night with these massive mobile cranes. And actually, so we did all the modeling and detailing for that for fabrication, but also helped with the kinematic simulation of how we were going to actually move these things safely. Pretty incredible. So, we fortunate to be involved with that. So some of the high profile projects, but also lots of many, not high profile, but still equally impressive projects that are five stories that are mixed use projects that are being built in mass timber.
(22:19):
And why I say that is that economically, from a performer perspective, I used to work on the owner's side past my past life. These projects didn't pencil before, they just didn't make sense. And they're starting to make more sense where people are making, hey, I think we can build this in mass timber, get a lot of the benefits of the prefabrication process and time, the time value of money of delivering a project quicker with higher quality, more precision. People like to live in these buildings more probably because of the wood and stuff like that. So it's also a big step I think. So a lot, we worked on a lot of smaller projects that don't get all the accolades and stuff that are equally as impressive because they're being delivered typically by the standard trades or subies as you call 'em, that are not fancy and they're not timber-focused subies and they're just delivering these projects because they ecosystems getting bit better at being able to say, well, if you're a carpenter, you're doing form work, you probably could install some panel as well. Some CLT panels with some training and some coaching.
Adam Jones (23:18):
Yeah, that's so good. And it sounds like every time you, you're working on another project because you are using code based solutions, that's infrastructure and you've got a starting point and it's evolving and everyone's doing it in different places. Do you see this driving down the cost of solutions like this as we go forward?
Javier Glatt (23:35):
I hope so. I think so. I definitely, I think it's controversial because I don't want to, there's a lot of evangelism in the mass timber space. People are like, it's just going to change everything you'll ever, I'm not sure we're there yet. I think that there's some issues that need to be flushed out. I think there's some early adopt. I think we're getting through the early adopter phase. And again, I'm not going to pretend like I'm an expert on all things mass timber in the world. I have been fortunate to be involved with quite a few and I've learned from a lot of amazing architects, construction engineers, just being in the room with them and
Adam Jones (24:09):
I'm got to say are probably the only person who's been on the most high profile projects around the world. So, I've got to going to call you out on your humility to continue.
Javier Glatt (24:17):
Oh, well that's nice of you. But I think as you do more, I think you learn how a little you know. And these things are so complicated and I think a lot, it's easy to just make wide sweeping statements and owners have a perspective and then the supply chain has a perspective and the design team has a perspective and there's environmental cases to be made, which I'm hearing changes all the time. When I first started, it was very clear that environmental positive aspects of mass timber, and lately I've been hearing some studies coming up that challenge that a little bit. I don't think I'm here to say that it's not good for the environment, but there are considerations about chopping down trees and putting on buildings and yet, and just understanding of what all that means for the industry. But I think also cost, you mentioned cost.
(25:14):
Cost is just still a major factor. And I don't know. What I think it is we're trying to apply again, our company has struggled with this, quite frankly. We're trying to apply a repeatable manufacturing process like they did in cars. Everyone says, oh, it's like cars. This aren't, these aren't cars. We're not building cars. The project's different every time. You're a structural engineer, even if you have the exact same design, it's going to be different if you're in a different market. It just is because the structural code and different things you have to do. We're in a high seismic region, so the seismic constraints just make up big. It adds a lot of complexity, it adds a lot of complexity to the whole thing. And you can't just say, here's a template, run with it. Just build, make the same thing every single time.
(26:00):
Just in theory it looks, sounds great and a PowerPoint, it looks fantastic, but in practice it falls apart. And I think it's not like these problems can't be solved. I think they can be solved, but it's like what's the right structure to deliver a project to solve it? Is it an owner having a stake in that and being shared equity? Perhaps is it better for rental where you can have a long term revenue stream from that asset and you can amortize some of those additional costs over longer period of time if you're just going to build it and sell it and try to get your money back day one. You know, have a lot of risk volatility in the lumber market supply constraints. If you look in the market in North America, I mean if all of a sudden all these projects that are being designed actually all went to production at same time, the market couldn't serve it right then.
(26:45):
Now you go overseas to Europe can handle it. But then a lot of the reasons why this project got designed in the first place kind of start to fall down because you got a lot when you're sending the panels all the way from Austria, there's definitely a bigger footprint to that and there's a different cost. And then you look at Austria, I'm kind of rambling now, but I think it's really interesting to talk about how some of our teams have done quite a few visits to the various factories in Europe and stuff like that. And it's truly incredible how automated, they're running massive factories with just a few people. It's very impressive process. Say, well, why can't we do this here? Well, it took them years and years and years and years to develop that. And the culture's different in Switzerland where I was lucky enough to see some amazing factories in Switzerland.
(27:35):
Goodell is one of them, a few other companies are, and they just have a culture there as well. This is many, many decades and generations of how they build in Switzerland. And you can see that in how they set up their factory. This is a cultural thing as well as a technology and process thing and a quality thing. It's not so easy to just replicate that everywhere in the world that don't have the same culture. So yeah, it's a fascinating thing. I think there's a lot of opportunities and we'll see. Hopefully, we can get, I think we're out of that early adopter phase now we're into the scale up phase. You're in a startup. This is the hardest part. I mean, making it repeatedly work is a challenging thing and we're trying to do our part in the ecosystem to help with that as well.
Adam Jones (28:21):
Yeah. Well, how exciting. If people want to find out more about yourself, Javier, and what you guys are up to, where should everyone go?
Javier Glatt (28:29):
Yeah, so cadmakers.com is our company. CMBuilder.io is our product, main product that we focus on. We have some other stuff there too. And then we do a lot on LinkedIn, so we try to post on LinkedIn and try to have some fun with it too. So yeah, that's where can find us.
Adam Jones (28:47):
Well, thanks so much for coming on the podcast. That was phenomenal. I really enjoyed that discussion and we'll catch up with you no doubt, sometime in the future when at a conference or something like that.
Javier Glatt (28:57):
That'd be great. Thanks Adam. Appreciate it.
Adam Jones (29:00):
Thanks mate.