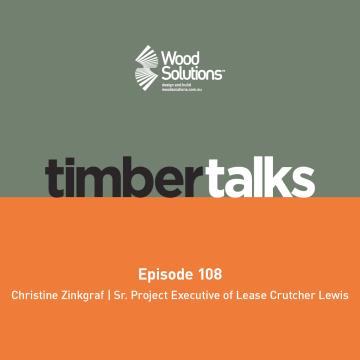
In this episode of Timber Talks, we had a conversation with Christine Zinkgraf from Lewis Builds about the growth of mass timber buildings and the advantages of this construction method. We discussed topics such as the increase in interest, the speed of construction, the risks involved, and the level of prefabrication that makes sense. Christine also shared her thoughts on the challenges of using old versus new wood and the innovations in the industry, as well as where she sees the industry moving in the next five years.
Timber Talks Series 6
Series six of WoodSolutions Timber Talks, provides the latest informative and entertaining information about the best design practices, latest innovations and interesting case studies and interviews with world leading experts in timber design, specification and construction.
Adam Jones (00:07):
So thanks so much for coming on the podcast. Christine, can you start by telling us a little bit about yourself and what you do?
Christine Zinkgraf (00:14):
Sure, yeah. Thank you so much for having me. I'm Christine Zinkgraf. I am a senior project executive for Lease Crutcher Lewis based in the Portland office and I touch on a number of market sectors. More recently have had a chance to work on some mass timber buildings, but of course in the Pacific Northwest it's pretty popular up here. So glad to be talking with you about it today.
Adam Jones (00:34):
Yeah, fantastic. And can you tell us a little bit about the recent drivers and the recent interests that you are having in mass timber construction in your part of the world? So in Portland I think you said, is that right?
Christine Zinkgraf (00:45):
Yes. Right. So northwest part of the United States and yes, a couple years back, they actually changed the codes in both Oregon and Washington to allow for more mass timber construction, specifically some of the assemblies that weren't previously able to be permitted. So that definitely has been the impetus behind a lot of the new construction in this area where we're seeing a lot more mass timber being implemented. But in general, I think it's still a buzzword. It continues to be a buzzword, both public and private developers around here. And we're a bunch of tree huggers anyways, so we might as well fully embrace it. At least that's the general opinion from the world around us. But I think anymore, I find that if you're, say a structural engineer for example, and you don't have a mass timber expert on your team, you're potentially missing out on a really big part of the market share. It's just something that's become a lot more prevalent. And there's even around here, there's certain contractors that have specialized work groups that, or even a fully fledged subsidiary that they focus solely on mass timber construction. So I think the key really is just having the right people on your team and help the developers decide from both a cost standpoint and maybe a design standpoint whether mass timber's the right solution for their building.
Adam Jones (02:02):
So one of the drivers everyone speaks about and is well aware of is sustainability, which might be more of a gateway sort of thing to get into some of the other advantages. So what have you seen as the major drivers from your perspective for new developers getting into this space?
Christine Zinkgraf (02:18):
Definitely, sustainability and whether we like it or not, that's marketable and I think that that's really important for development. Biophilic properties, that's something the architects love to talk about. Who doesn't want to walk into a building with beautiful exposed timber overhead? There's absolutely something to be said for the fact that people prefer to work there. It's good for, I think, recruitment and retention. We've talked to a lot of folks who live and work in those buildings and they say that people tend to generally be happier, there's higher employee satisfaction, so that's a huge focus. One of the things that we probably don't talk about enough as an advantage is the fact that CLT is pre-fabrication, and that's something that all contractors always talking about. We're always trying to take different building components out of the job site in a controlled environment offsite where you can focus on quality and labor's less expensive sometimes. CLT is prefab. And the fact that when we bring that concept up, people usually think equipment skids or large piping systems. This is such a simple and beautiful solution to dropping an entire slab on a building in less than a day and you have the ability to precut all of your penetrations. It's really plug and play.
Adam Jones (03:30):
One of the drivers you mentioned then was around exposed timber and by Ophelia, I'm interested to know Christine, because in our country with a national construction code, there's a lot of plasterboards in terms of from a fire protection point of view, and I believe the international building code is quite a bit different to us. So can you just touch on the amount of exposed timber and what height of buildings can you allow for exposed timber just at a really general level in some of the projects you've been a part of?
Christine Zinkgraf (04:01):
Sure, and I don't have everything memorized, so I can't tell you exactly but I can say I think in Portland right now, one of the tallest mass timber buildings that is in planning is eight stories and we always see a topping slab. I'm guessing that that's probably the same case throughout the world but just you can't get the same fire rating without a topping slab. So that always happens. I've seen, it's interesting, some of the other kind of combinations that are coming out of the woodwork that an architect called me a couple weeks ago just asking about feedback on, they wanted to put slab on metal deck with exposed timber columns and flu lamps, which I thought is an interesting combination. So people really are experimenting more now that we have the ability to push the envelope with some of the code limitations that are lifted.
Adam Jones (04:46):
Yeah. Well the other benefit you mentioned around was prefabrication. Can you tell us a little more on speed and how to, overall, what are the key ways to optimize and make sure we're maximizing the speed of construction?
Christine Zinkgraf (05:00):
Yeah, that's the biggest selling point for me whenever I'm talking to a developer about whether mass timber is the right option for them, speed to market, because there's still the perception and there's some truth to it that it can be more expensive but time is money. So that's certainly a consideration. And I think a couple of the things you can do to make sure that you get that speed out of your project is your schedule and your sequence have be dialed, and that has to be prepare for the worst case but also the best case at the same time if you can. Yeah, that's tough. There's trucking limitations. You can't always control when your material arrives on site, but all that means is if you're able to be more productive than you thought you were, jump on immediately, get all that stopping finished and all your fasteners and everything else then.
Adam Jones (05:48):
And does that go to the follow-on trades and things like that? Does that cross your mind when you're in sequencing?
Christine Zinkgraf (05:54):
Definitely it. So team structure's important too. I think one of the things that we've been able to do in the past is if we set our CLT faster than expected, immediately you're up there putting your temp protection and railings up, you're getting if you have offsite, pre-fabricated wall panels, they can be staged nearby and you can start getting those in place. All of that really leads to I think a more efficient job site as a whole.
Adam Jones (06:19):
Yep. And you mentioned on team there as well. I mean is that this is a critical advantage we're talking about now. Is this something you bring up on early and who in the team would you sort of be really critical to enable this speed as well?
Christine Zinkgraf (06:34):
Yes, absolutely. When your superintendent's planning the work, you have to know who's going to be executing. And I think the fact that you know have however many carpenters you need, you have certain folks unloading, prepping the panels, you've got people receiving off of the hook, you've got other people that are installing your hardware or your slimes. So really thoughtful consideration for where they're staged and how many people you have. And I mean, team goes out to your design team as well, even before you purchase the material, you can work with the design team, the structural engineer on what fasteners are you going to be using, how many per strap, get extra eye hooks from the manufacturer. That's another thing. There's things come for free, they'll just throw another kit in there. You can be setting your hooks on one panel while the other one's coming off of the crane and just get your production speed up a little bit.
Adam Jones (07:22):
Yeah, great. And do you have any thoughts on just general de-risking of the project? So speed is one thing, but being something new, especially that you've got a lot of experience also here that someone coming in fresh it's a bit, seems to be risky. So how do we solve for that?
Christine Zinkgraf (07:40):
I would definitely say, again, start with the design team. You can vet a lot before you even get out of the drawing stage. So I think one area that you should spend some time and tension on, especially with your structural engineer is all of your connections. Timber to timber, timber to steel, whatever happens to be, if you get out to the field and it's not something that can be easily put in place or your trade partners had made an assumption and it doesn't pencil out, you can be stopped in your tracks, not unable to stand any columns. So I think that's that part of the design definitely. We talked about topping slabs, that's something else. Think through all aspects of it. Is there a waterproofing membrane? How do you apply that membrane? When do you apply it? Do you need to have specific pore stops that aren't accounted for because you've just got this open CLT slab? Are you sloping your topping slabs? All those things, constructability-wise, you can get those flushed out before you're fabricating.
Adam Jones (08:36):
Yeah. In terms of fabrication, what do you think makes the most sense? You've got like 1D, well 2D I guess is your panelization, and within 2D you've got a single CLT panel maybe, or then you've got maybe windows and doorframes and all that sort of stuff. And then you've got 3D, which is like a modular. So in your perspective, what do you think makes the most sense for a project and what is some of the thinking behind that?
Christine Zinkgraf (09:02):
2D versus 3d? I think most fabricators are using 3D these days. I don't know that any of 'em are doing 2D. Their equipment's so sophisticated that they're using to cut the panels off the line anyways. You might as well go 3D unless there's a huge cost associated with it. I can't imagine there is. But any more architects are designing in 3D, everyone's building in Revit these days. So if you can just pop your CLT 3D into your combined model, that makes it that much easier to coordinate, especially when you're doing your penetrations in the factory.
Adam Jones (09:35):
Yeah, yeah. Makes sense. And I know one of our pre-podcast discussions, you mentioned how you've got experience working on buildings that are sort of existing timber structures. And what are some of the unique challenges of, say, working on retrofitting existing buildings compared to what we're talking about now, which is all about new timber buildings.
Christine Zinkgraf (09:56):
Nothing's plumbing square. No. One of the things that surprised me, and I guess it shouldn't have, but it did. I'm not a structural engineer, I'm a mechanical engineer, so I can't speak to this year intention and all that for old growth wood, but I can tell you it is a lot more dense and so much so that the engineer should and can account for that into their calculations. There's different factors that can be used. The one we were talking about previously, there's an adaptive reuse project I worked on in southeast Portland called the Factor Building. And it's beautiful old, old growth timber existing old factory. We were putting new seismic reinforcing on it, heavy thick steel plates. It was taking maybe a half hour to get through just a single three quarter inch hole through a 10-inch beam. That's insane. It's totally, it's a huge labor suck. We were going through $50 drill bits by water, so just in general, incredibly expensive. We went back to the structural engineer and said, Hey, is there anything else we can do? And he went back and recalculated and found we didn't even need to use half of those plates because of the fact that it was as old timber. So there's certainly I think, benefits to it, but you just have to be prepared when you're getting ready to work with it and know what you're getting into.
Adam Jones (11:11):
Yeah. Awesome. Well, it's been great change here, Christine. One of my final questions is just your thoughts and general innovations in this space and where do you think things are evolving and sort of a blue sky of where you see things maybe in the next five years or so?
Christine Zinkgraf (11:27):
I hope that the codes continue to open up and that we can explore new assembly, let's say being a renewable resource. That's absolutely the way I think that most of the world wants to go. And the fact that we're seeing it also, again in new markets it's pretty popular these days as an office. We see it a lot in even multi-family now in single-family homes. But I even talked to a developer the other week about they wanted something to differentiate them from their competition and it's a data center developer, which is tech technically or traditionally just robust kind of square concrete buildings. Well, they were thinking about using this in their lobby space because it would be something to again draw people in, bio affiliate, all of that. So the fact that we're seeing it in different markets, and I hope we'll see different applications in terms of assemblies, the more we test it out, the more we try it, the more we'll find out.
Adam Jones (12:25):
Fantastic. Thank you so much. If people want to find out more about yourself or your company, where do you want to take them or where should I go?
Christine Zinkgraf (12:33):
Oh, www.lewisbuilds.com.
Adam Jones (12:37):
Thank you so much, Christine. I'll leave it there.
Christine Zinkgraf (12:40):
Thanks.