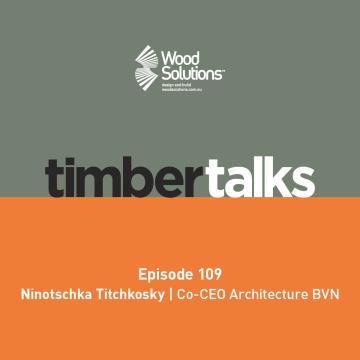
In this episode of WoodSolutions Timber Talks, we sit down with Ninotschka Titchkosky, co-CEO of BVN, to discuss the groundbreaking Atlassian Tower. As the world's tallest timber building, the Atlassian Tower in Sydney, Australia, will stand as a testament to the potential of sustainable construction and design. Join us as we delve into the journey of creating this remarkable structure.
Throughout our conversation, we explore the intricate process of designing the world's tallest timber building, from conception to completion, and the critical components that must be in place from the very beginning, including team dynamics, Building Information Modeling (BIM), and more. We discuss the sustainable design principles incorporated into the Atlassian Tower, and how they contribute to its eco-friendly footprint, as well as the major challenges faced during the design and construction phases and how the team overcame them.
Timber Talks Series 6
Series six of WoodSolutions Timber Talks, provides the latest informative and entertaining information about the best design practices, latest innovations and interesting case studies and interviews with world leading experts in timber design, specification and construction.
Adam Jones (00:14):
Thanks so much for coming on the podcast Ninotschka. can you start by telling us a little bit about yourself and what you do before we start getting into the project?
Ninotschka Titchkosky (00:24):
Sure. So my name's n Ninotschka Titchkosky I'm the Co CEO of BVN. We're an architectural practice and we have about 360 people. Our two sort of main studios are in Sydney and Brisbane and we also have footprints in New York and London. And as a practice, we really do all kinds of projects from incredibly little ones to very big ones over the billion dollar sort of scaler project. And we do kind of work across almost all sectors and in a way that's something that we really value because we do a lot of cross-pollinating between our knowledge of sectors. And I'm an architect as well. Probably been an architect for nearly 30 years.
Adam Jones (01:17):
Yeah. Fantastic. So we're talking about the Atlassian Tower today and perhaps one of the coolest, well it is the coolest mass timber project in the world and I'm sure just in more generally across buildings. So what was your reaction when this brief came in and tell us from the beginning about the brief and the process when something like this lands on your desk?
Ninotschka Titchkosky (01:37):
Yeah, well I mean guess this actually started what, nearly seven years ago. So the competition was actually in 2016, which seems a long time ago now, doesn't it? And at that time, Atlassian was sort of really gaining strength in the market as one of Australia's kind of leading tech companies that were very much in that growth period and certainly kind of a bit risk-taking, which is awesome. But they had been working with government New South Wales government for a little while around bringing this whole new precinct to life in Sydney, which is called the tech precinct. And the intent of the tech precinct as to sort of create a hub for technology-driven businesses that's close to the universities close to, very close to central station that would help drive the economy as well. So it was very much a kind of government backed initiative and they saw Atlassian as the key anchor tenant in that or sort of key anchor for the precinct that would bring others to it.
(02:46):
And so they set us a set about creating a very ambitious vision for the project, which was pretty rare that you get a brief where the ambition is so high. And actually they'd done a fair bit of pre-work on it to just ensure that that vision was actually going to be deliverable, at least in concept. So the brief was to create essentially a 40 story hybrid timber tower. And one of the key things that they needed to do to make sure that was actually achievable even in a competition mode was to do some background work on the structural engineering and some of the fire engineering solutions and some of the climatic solutions. So there was a fair bit of pre-work actually done, which is very unusual in a brief that we could then take and build from. And so we joined forces with shop architects from New York and sort of came at the competition as a combined team and that was in yeah, 2016. Sure.
Adam Jones (03:55):
Fantastic. That's so cool. So what are the things at the very start to get right? You mentioned it's an ambition that's perhaps a bit unusual in construction, so there are things that's slightly a little bit different. What are the things from the very beginning that you need to get when you're doing a project of innovation of this scale?
Ninotschka Titchkosky (04:13):
Well I think that probably the most fundamental is a client that's willing to put the hard yards in and actually stay courageous through the project. Cause I think that's in the end that is, there's always reasons why to give up along the way as the project gets harder and harder and you're trying to jump the hurdles. So that's probably number one. I think number two is just getting the best people around you and the best team around you. And we really had an incredible global team and we have people from all over the world kind of working on the project. Whether it was the climatic engineers or the fire engineers or the structural engineers. We've got architects in Australia, architects in New York. It was this really multidisciplinary very large team. And we actually ended up having to do most of the design work online, collaborating online together.
(05:14):
Cause it happened all through covid. So once the competition was one and we actually started the project proper, we actually only had one full team meeting together in New York. And then we were online for two years doing most of the design work together. So that was certainly a bit of a challenge. The other things to set up I guess are yes a good, really good collaborative environment, super important. And then obviously we set up a lot of methods because we were working online together and we were this kind of global team. We did set up some pretty good methodologies of how we were going to share documents and shared design information. So we got very good at setting up all our design presentations through Google Slides and doing shared decks, doing sort of 24 hour cycles of turnaround of design time. The whole project's all obviously set up in BIM 360. So we've got full three shared 3D models and so on. Yeah, the whole, they're setting up the right framework for the project is super important just in the sort of more the day-to-day doing. But then it's equally really important to just have that client with the conviction of what they're trying to achieve. And then everyone absolutely bought into the vision. And so being guided by that shared vision was very important.
Adam Jones (06:51):
I might drill down a little bit further on that. So most projects in the past you could maybe have design meetings where you catch up once a week. Imagine if you did it the old way, you'd have a huge, so many people in the room to sort of BIM 360 enable sort of a lot more ease between disciplines and everyone just working on their unknown unknowns and then coming together compared to what it used to be.
Ninotschka Titchkosky (07:16):
Yeah, I mean we were really kind of on almost a daily cycle of collaboration. It was quite intense to be honest. And there was, I think by the end of the couple of years it was pretty exhaustive. I was quite exhausted cause we were all also trying to match time zones and things like that was really hard. I mean the other piece in the puzzle, which came a little later but is just a collaboration with the contractor as well, which is also really important in how the whole process roles. And so we are working with built Obii and they've, they've been really important as well. And it came on quite early to help us kind of work through a lot of the risk issues and things like that. But also the other part of the collaboration process that was really important was the cost planner and also tracking some of the key brief issues.
(08:21):
So we had a few of the key brief things that we're looking to target is 50% less embodied carbon, 50% less operational energy and a hundred percent renewables. And in terms of the embodied carbon, we were actually sort of real time tracking that through the design process. And so we, we'd often have the cost planner who was actually doing some of that work in collaboration with the sustainability gang. And so the way that everyone was pitching into the design process, it wasn't just an architecturally driven thing, it was really everyone was continuing to add their pieces to the puzzle as we were developing the overall design.
Adam Jones (09:12):
And I believe, can you let me know if the embodied carbon side, was that including offsets or not including offsets? And maybe can you just drill down on that? We don't have to talk only about timber but across everything embodied carbon more generally and how that can be achieved.
Ninotschka Titchkosky (09:27):
Yeah, sure. So those targets were actually set up in the brief. So 50% less embodied carbon and it's 50%, 50% less embodied carbon of a similar building type built on that site. And the reason for that is that there are some particular anomalies about the site itself, which we can go into a little bit later. But that mean that you couldn't just sort of say, oh well it was just the equivalent of a greenfield building that's 40 stories high. But what it actually is, it doesn't target every aspect of the project. What it really looks to is structure facades and groundworks basically. So in order to achieve that, the things that we need, well first of all I guess the idea of the hybrid timber tower gives us a concrete core, a steel exoskeleton. And then essentially the way the building works is it's sort of divided up into habitats, which are four stories high.
(10:38):
And every fourth story is a steel and concrete floor, but in between that is a little mass timber village. So everything in between that is made of mass timber and then every fourth floor is a structural floor, which is also our fire compartmentation. So we were obviously going to get some great outcomes within embodied carbon for the mass timber. For the concrete we are working, we had to really look carefully for the mix of the concrete and look for a low geo polymer mix. And then for the steel, we're effectively manufacturing the steel offshore so that we can use a low embodied carbon steel. So we can't buy green steel in Australia and we, there's really no sort of at the moment there's no kind of great alternatives for that. So we had to, we're getting the steel from overseas so that, but even with all of that and with the transport, it still was giving us a still better outcome. But it's also about scrutinizing how you optimize the materials, what don't you need? So do more with less. We are really looking at the sort of gauges of steel, the extent of concrete works, all that kind of stuff played into the picture.
Adam Jones (12:05):
So what are some of the major challenges that you've faced so far or currently been faced that you've had to overcome on this project?
Ninotschka Titchkosky (12:13):
Well, I think there are so many, it's kind of crazy but one of the realities in, I guess, so it's hard enough to build what's currently sort of musher to be the world's tallest hybrid timber tower, even if it was just on a very simple site. But we're actually doing this on the very edge of Australia's busiest rail corridor and we're actually having to build on a site which has an existing small heritage building. So it's kind of like could we make it any more complicated? And we're in a heritage precinct, so it's just in levels of complexity, it's kind of like the crazy order of level of complexity. So that was set, that's certainly been a massive challenge and that's just meant that there's lots and lots of stakeholders that are involved in the project. There's lots of eccentricities about being building on a rail corridor, which means there's all the kind of particular things that transport's looking to achieve the amount of people that are going to be moving through the site.
(13:25):
That's certainly been a huge challenge just dealing with the site, the actual site issues. The other ones probably are also the fact that it's something that hasn't really been done before globally. So the level of rigor that you have to go through to ensure that the risk profiles not too high is pretty significant. And then particularly one of the big ones is really fire issues. So ensuring that we're meeting all the fire codes and that's why we've got the sort of four story habitat model which helps us deliver on that. They, they're some of big ones but yeah, there's sort of thousand little ones as well.
Adam Jones (15:19):
Well that leads to my next question you not showing that's around the building approvals process. Of course everyone's mind goes to fire at a building of this height. How did you bring everyone along the journey and actually get everything approved and reduce the risk in the appropriate ways?
Ninotschka Titchkosky (15:38):
Yeah, well the approval process was really, is actually really complex and it in fact is sort of an ongoing process that we continue to participate in as the design keeps evolving. But where we, just to clarify where we are with the project at the moment. So the hole's been dug and we're actually on site, which is great. So that's pretty exciting. So things are really kind of heating up now. But the approvals process was very complicated. This project is what we call a state significant approval process. And it means that we had to have the city of Sydney, we have to have transport heritage, the designing with country overlays, government actually. It's like we have a very kind of large group of authorities that we have to meet requirements on. And then so that process was very much a constant process of presentation and so on as we were developing the design.
(16:42):
And then they provide feedback and then we would continue to evolve. Now we're in the period of, we're pretty much just, there might be some minor changes and we are just circling back through those with them. But in terms of authorities like fire and so on, also that has been complex as well. But the main thing is with these projects is that you stay really transparent and open that you can't sort of hold everything to you and then all of a sudden launch it on everyone and think that you're going to get the answer you're looking for. So I think that understanding the key issues from all the different kind of authorities perspective and then trying to ensure that we are meeting those, but also bringing them into the design process a bit so they understand where we are in the process and what we're trying to achieve. Of course with a project like this one, the fact that the government is actually backing the precinct and it's something that looking, they really want to drive as part of the kind of economy and the success of New South Wales, that does help us a bit, but it certainly doesn't relinquish us from having to meet all of those stringent requirements.
Adam Jones (18:01):
Fantastic. And in a second I'm going to ask you a few more generic questions about the industry going forward. So is probably my final question on this building. So I'd like to just know how does this building reflect your values and your mission and just your overall pride about what's being built forward and how it's going to change things in Australia?
Ninotschka Titchkosky (18:20):
Yeah, I mean Atlassian's such a interesting project cause it does really, I think a real, really reset globally what we can expect from commercial buildings and new buildings. And not just in terms of our environmental goals, but also just the way that we create communities within tall buildings and also the way that we think about how we optimize the unique conditions of place wherever we're working. So I mean we have a very sort of clear goal as B V N in terms of working towards a net positive outcome for projects. And so Atlassian is definitely in the sweet spot of aligning to our sort of bigger practice goals. And I think when we are faced with an industry that's contributing 40% carbon emissions to the planet through construction, it's really all of our imperatives to start to think differently about how we design, how we build, how we start to pull waste out of projects and things like that. So yeah, Atlassian, I really hope it is sort of part of a reset and that it actually provides a bit of a north star for other developers and other clients who are like, oh, I can see that I can actually achieve this. I can set ambitious targets and it does pay off. And yes, it's hard to do but in the long run it actually gives us a future-proofed outcome and we set our standards a whole lot higher than what they are at the moment.
Adam Jones (20:02):
And forever Timber Timber's been using that low rise one to two stories and maybe the last 10 to 15 years it's pushed three to eight and now has seen 40 stories. What do you say is the feasibility from now going forward of mass timber in the high rise space?
Ninotschka Titchkosky (20:16):
Yeah, it's super interesting actually. And it's, I mean there's some really nice projects happening all over the place that are starting to, it's a bit like an arms race I feel like too. Let's ratchet it up. Come on. How high can we go? Obviously we'll hit a tipping point where 40 stories in timber makes no sense cause you're going to have huge sections and things like that, which is hence the hybrid. But for sure there's a building actually the ascent tower that's just been finished in Wisconsin in the US and I think that gets up to 25 stories. It's about 86 meters high and there's another one I know on the books for Switzerland, which is looking to be a hundred meters high. So people are really starting to push the boundaries and a bit more, I guess there's some more work being done around thinking about slightly hybridizing or augmenting some of the timber so that it can actually increase its strength, grades and so on, which is giving us some new opportunities to get the hide up.
(21:24):
I think actually interestingly, our studio in the UK has just moved into what they say is the tallest timber building in London and it's significantly lower than those two. So I think there's a bit more work to do in the UK. They're not quite as courageous maybe as some of the rest of us, but in Australia pretty, we're pretty good. I think there's a sort of absolutely level of willingness to just go for it a little bit. And I think it's paying off for us, which is really nice. So I do think mass timber will continue to grow and it'll become more and more, less and less if you like, scary for people. And I think also what's important is that particularly cost planners, project managers, those are those people that are directly advising the clients getting more across the procurement process and the costing and the fact that it's actually not a really high profile risk option.
(22:35):
So quite often we found in the beginning, sort of six or seven years ago when we were doing our first mass timber projects, that was a real barrier for the industry where even though the architects would be trying to get the projects up, they'd get stopped at that point. And it was particularly because to some extent, if not familiar with something, you kind of attach a lot of risk to it. Actual fact, our experience has been working with timber, it's like the cleanest site that you can work on. You can reduce your labor by 60% or more sometimes compared to a conventional build. It's pretty extraordinary. And then obviously you've got the kind of beautiful biophilic and sort of human aspects of occupying timber buildings, which people just always love.
Adam Jones (23:30):
Absolutely. So tell us about what you see as the future of construction in the next five, five to 10 years. Doesn't have to be specific on Tim, again, just more generic where things are going. Do you think?
Ninotschka Titchkosky (23:41):
Well, this is a bit of a hot topic for me and I guess what I'd like to talk about is where I'd like it to go. Whether we get there or not I think is another matter, but at the moment construction is one of the lowest one of the industries that has the least productivity out of any of the major industries that make up the GDP of countries. And that really hasn't changed, which is incredibly woeful when industries like manufacturing have sort of rocketed nearly to the top. And part of the issue is that we are just not changing the way that we're doing things. And so my hope is that if we want to decarbonize the construction industry and we want to take out time, we want to reduce time, take out the cost of wastage, reduce the cost generally, and also just sort of reduce the amount of resources required, we really need to think differently.
(24:43):
And I don't think it's just incremental change. I think it's radical transformation that we need to do. And a large part of that in my mind will come from integrating digital technologies, robotics, advanced ways of building where we're actually getting away from just sticks and sheets and we're starting to think differently about how we build. And also the way that the process works, which is time intensive. There's a lot of waste in it if we can just do so much better. So my sort of hope is that we can genuinely start to think differently about how we do things as an industry and in doing so we'll solve a lot of the challenges that currently exist as well, which are the margins are low for cons, contractors, the lab, there's labor shortages, productivity's low, there's a lot of wastage, clients are paying a lot. So there's a range of different factors which should drive us to change. And my hope is that by doing all of that, we'll actually be able to create those positive outcomes and also sort of push the boundaries of the materials that we're also using and make sure that we are being much more robust around material selections and embodied carbon in materials.
Adam Jones (26:13):
That's great note ended on, thanks so much for coming on the podcast in Notch Car. If people want to find out more about yourself or BVN or they got a project and they want to build another Atlassian tower or anything like that, where should they go?
Ninotschka Titchkosky (26:26):
Oh, thanks Adam. Yeah, you can come to me, but you can check us out on bvn.com.au and you can find our contact details on our website, but anyone that wants another one of these crazy ambitious buildings, bring it in.
Adam Jones (26:47):
I'm sure that's the dream of every architect getting things like that. So thanks so much for that. That was awesome.
Ninotschka Titchkosky (26:53):
No problem. Thanks Adam. Thanks for having me.