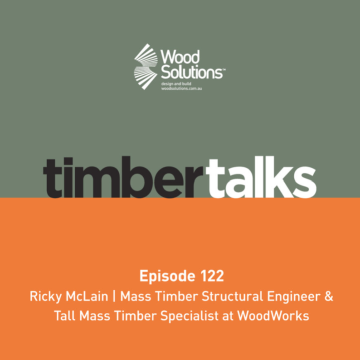
In this episode of Timber Talks, we're joined by industry expert Ricky McLain. We explore the upward surge of timber in the architectural landscape. Ricky sheds light on its rising adoption and the evolving cost dynamics. Beyond the traditional uses of timber, we dive into its potential in high-rise constructions and envision the transformative future of timber-infused skylines. Prepare for an enlightening discussion that bridges the gap between ancient material and modern innovation.
Timber Talks Series 6
Series six of WoodSolutions Timber Talks, provides the latest informative and entertaining information about the best design practices, latest innovations and interesting case studies and interviews with world leading experts in timber design, specification and construction.
Adam Jones (00:00):
Well, thanks so much for coming on the podcast. Ricky, can you start by telling us a little bit about yourself, who you are and what you do, and then we'll get into it?
Ricky McLain (00:12):
Yeah, for sure. Adam, great to be with you here today and happy to be talking with your audience as well. So my name is Ricky McLean. I am a structural engineer. I work for a US-based nonprofit organization called WoodWorks. And my background comes from studying engineering in college and then right out of college I grew up in Maine, moved to the state of Vermont and took a position at a small consulting structural engineering firm in Vermont. We did both civil and structural work and didn't specialize in any type of building or use of material. We certainly did some heavy timber and light wood frame construction as well as other materials. We did a lot of police stations, fire stations, higher educational facilities as well as custom single family homes. So it was a good introduction to a variety of use types with the different types of projects that you would see from a structural engineering side of things.
(01:15):
And then about seven and a half years into that career, this opportunity with WoodWorks came up. And so I've been with WoodWorks now for just over nine years. And what we do is, like I mentioned, a nonprofit that provides free one-on-one design assistance or project support to primarily architects, structural engineers, developers and contractors. And it's basically any type of project that's using wood, so light wood frame construction as well as heavy timber and mass timber construction in a project that's anything other than a single family home. So the vast majority of that is multifamily apartments and some hospitality as well as commercial retail, mixed use educational. But basically we're working with those people on a day-to-day basis or really just to answer any questions that they have to remove a lot of the hurdles or barriers associated with using wood in construction. So it could be very high level.
(02:16):
Does the code allow us to build this type of building out of wood or it could be much more in the weeds of we're designing for a floor assembly that has to meet a certain fire rating and acoustics performance and span structural design. So that's the primary thing that we do. We have a team of regional directors throughout the US so that there's always somebody close by no matter where in the US you are. And then we also do a lot of education, a lot of presentations at conferences, hosting our own events, participating in others events. We're a co-producer of the International Mass Timber Conference as well as a few other regional events throughout the country. So that's kind of in a nutshell what WoodWorks does. And my role is kind of across a number of different aspects of that, but a lot of it's focused on mass timber and specifically tall mass timber project assistance.
Adam Jones (03:10):
Excellent. So you've been there for nine years now and I'm sure you've seen a lot of change. So tell us about the trajectories. How has it evolved over that time and what are the things driving it? What are the things driving change in the adoption of mass timber?
Ricky McLain (03:27):
Yeah, it's interesting to think back about nine years ago when I first, well, when I was going through the interview process to get to work for WoodWorks, and I remember leading into that interview, well first of all I had seen, there was an article in the us there's a structural engineering magazine called Structure Magazine and it's a trade publication and it has kind of articles from practicing engineers. And one of the articles, this was probably like three months before I joined WoodWorks, I remember seeing an article about cross laminated timber CLT. And so this was 2014 and in the US at the time, there was maybe a dozen, maybe 15 projects total that had used mass timber. And so it was this very novel idea. And so I had not participated in any of those projects. I had no practical design experience. So I went into that interview that having done some homework basically saying, I don't know really much of anything about CLT, but I understand this is probably going to be a big area of growth opportunity.
(04:27):
And the answer from those I was interviewing with was very much like, well come along board because we don't know much about it either. We're all going to learn along the way. It was very much early in the process. And so over the next nine years, kind of fast forward where we're now, it's been very interesting to follow, I would say very parallel trajectories with light wood frame construction and mass timber construction because when I first joined in 2014, most of the, like I mentioned that one-on-one project support that we do, most of that was on light wood frame projects. So very common four story or five story, apartment building, condo, hotel, those types of affordable housing projects. And the questions starting out were a lot based on how does the code allow this to be done? What are the allowable building sizes and scales and how to maximize density on the site that we have to.
(05:24):
Then a couple of years later, as more and more people were doing that, the questions became much more in depth, very specific questions about how do I design this exterior wall to floor intersection detail to make sure that we don't have passage of fire from one floor to the next, and how do we detail the shaft walls where the intersect with floors and firewall detailing? So again, this increase in adoption really led to from our perspective, much more in depth questions, which was exciting because it allows us all and me personally, to grow and to learn to be able to develop resources to answer those questions. So mass timber followed a very similar trajectory. It was just several years beyond that point. So several years into when I started with WoodWorks was a lot of those initial questions of what is mass timber? Why would I use it?
(06:14):
How can it be used in commercial construction? Fast forward to where we are now, there's still some of those questions, but there's a lot more of the in depth questions of how do I design my CLT diaphragm connection detail to accommodate tolerance in the field and expansion and shrinkage or panels? Do we have to have, can it be used in seismic systems, CLT share wall design, timber brace frames? There's a lot more in-depth questions now. So again, it's this acceleration of the industry in general, which leads to more in-depth questions as more people use it, which leads to our involvement more and more in those types of questions. And I think that a one of your questions was like, what's been the cause for that uptick in use? It's been a combination of things and unique kind of confluence of the fact that we kind of think about the green building movement, which is a very umbrella term, basically how can we build better in a more sustainable way?
(07:11):
And going back a decade or so ago, a lot of the focus was on the operational energy, right? Doing existing buildings, deep energy retrofits for new construction, things like passive house style of construction and really drawing down the requirements to heat and cool and condition of building over its lifecycle such that we can minimize the amount of energy that's required to do those things through practices with the building envelope for example. So that was a lot of the focus. And then as those practices were more and more adopted, people started to realize there's also something else that we can do to build more sustainably, and that is understand the environmental impact of the materials that we're using because operational energy really takes some time to get that payout right. It might cost more upfront, but over the next 15, 20, 25 years of the building's life, we get the payback in terms of the cost to install those systems and the savings on the operational energy.
(08:06):
Whereas with the materials we put into the construction project from day one, those all have some type of what we call embodied carbon, which means the amount of carbon that it takes to produce them. And with wood, it's the balance of how much does it take to produce it and how much did it sequester while it was growing. So more of this focus on embodied carbon had led people to saying, is there a more sustainable construction material that we can use? And so mass timber really that was also about the same time when mass timber started to see use in Europe. And so people here in the United States and in Canada especially, were very interested in it and it's been a slow starting out slow and then much more rapid adoption process. The supply grows and people aware of it need for lower embodied carbon construction materials, which oh by the way look very nice and have a high strength of weight ratio structurally can do a lot of things flexibly or in a flexible manner.
(09:09):
And also there's low onsite labor requirements at time when there's labor shortages on site. And then one of the reasons that I think is one of the biggest reasons, but it's really not talked about all that much in terms of mass number use is associated with the financial benefits and long-term value that it provides a lot of times with mass number, it's a high initial cost where the materials themselves might carry a cost premium if we were to compare them to what's the alternative, but there's those benefits that we just talked about. But then there's also the long-term benefits of do we have lower tenant turnover in the building because more people like the building and they want to live there or work there and they're going to stay there longer. Tenant turnover is a huge cost to developers. Are they taking better care of the building themselves?
(10:01):
Is there a lower property management fees? Is it if you're looking to exit, if the developer's looking to exit the building three or five years down the line, does the building hold more value? Is there compressed cap rates when they're looking to sell? So there's a lot of ways that we can look at that value. And I kind of make the analogy of when you buy a car, a lot of times people just look at what's the sticker price, but you also have to factor into what is, if you're assessing two cars, right? What's the long-term maintenance of one versus the other? How much do the parts cost? How easy are those parts to get? What is the resale value of this car if I were to sell it five years down the line? So that holistically really paints a better picture of the quote cost or value of one thing compared to the other. And that's one area that really taking this holistic look with mass timber when comparing it to other materials helps paint that picture well. And that's why it's been really a winning solution in a lot of cases.
Adam Jones (11:00):
Yeah, a hundred percent. In terms of the triple bottom line, you've got sustainability, everyone knows all about that biophilia for human health, a lot of people are aware about that. But that third one is it's like the triple whammy. Once you can tick all three boxes, there's a bit of a holy grail and it is that education around the upside. I won't let you quote specific numbers, but you probably get asked all the time, what is the premium? So say if you could put it in a simplistic number like a rental premium or something like this, what is the overall what that is? And then I guess developers can work out a payback period if there is a worst case scenario of what the upfront cost differential is.
Ricky McLain (11:46):
Yeah, I mean it really does vary widely. Number one with the market that you're in, because regional costs vary a lot, meaning so well first of all, the market you're in and then also with the asset class. So multifamily is very different than office is very different than higher ed. But just to go back to the regional variations on cost. So in some areas, and I'm speaking very much through the lens of the US because that's what I know, but in some areas of the US onsite labor costs are extremely high areas like New York City, like San Francisco, like Boston. So in those cases there could be potential value, well, there's always going to be value, but there's scales or degrees of value of being able to do something quickly on site with a small crew. So getting a building up on site with a small crew is going to have a much bigger impact on net costs in a city like those where there's very high on onsite labor costs than it is compared to something where there's low onsite labor costs, there's readily available labor, it has a fairly low rate.
(12:54):
So is mass timber still going to prove a benefit there? Yes, but perhaps not through that vein. Whereas other projects that are built on very poor soils, mass timber can potentially benefit there too because it's a lighter weight structure. So there's a project right now that we're working on that they started out design with heavier construction materials. They're considering moving to mass timber and the savings for them is that they were going to have to drive 150 piles on the site. Now they're looking at potentially reducing that by 50 to 60% of the number of piles and or the depth of the piles. So that's not a savings that you would see in the cost of the finishes or the structural materials, but it's a huge impact on the net overall cost. So that's one area to look at the regional differences in costs. And then there's also really what comes into play is number one, is there demand in the market for it and then what asset class are you using?
(13:57):
So for example, there's a project in Denver that's in design right now. It's a 12 story master project and they're currently designing it and they took an initial pass at the estimate cost feasibility of the 12 story mass timber building. And then they had a parallel 12 story, I believe it was a concrete building. And what they found was that the mass timber, just looking at the structures, just isolating beams, column slabs, the mass timber was, I want to say somewhere in the order of about $62 a square foot. And then the concrete structure was about $10 a square foot less, somewhere around 52 50 $4 a square foot. It's a significant difference in cost, this premium associated with mass timber Timber. However, what they found was that number one, they went back and really looked more closely at the timber design itself and they found that it was basically designed in such a way that really worked with their initial pass at the unit layout, but that wasn't necessarily optimized for how do we make a timber solution most efficient for this building.
(15:02):
So made some tweaks in the grid layout to align or made some tweaks with the unit layout to align with the grid. So number one, they were able to reduce the volume of timber a little bit and then really what they found was that by shaving about 30% off of the construction schedule, they were able to save a lot of money in the construction costs. But really the biggest savings for them, as we all know right now, interest rates are very high interest rates on construction loans are high. And the interest cost alone of compressing that construction schedule took what was a $10 per square foot cost premium for mass timber and flipped it into a net $150 savings for the overall project using mass timber because of the savings on construction schedule and interest. So there's a number of ways like that, and that's not true for all cases.
(15:57):
For example, there's another project in Oakland that's under construction right now that's 19 stories, 16 stories of timber, but 19 stories total. And they looked at, it's being built out of the mass timber, they looked at an alternative concrete system and what they found was that the concrete system was about a hundred million dollars total project cost, and they were able to save about $5 million off the structure of cost by using mass timber and total project costs. They saved about $30 million because using mass timber allowed them to use other systems for mechanical and for exterior facades and those types of things. So the net impact was about $30 million savings on the project. So not always the case, but those are some examples. Usually what we say is that cost comparisons, mass timber to other materials, mass timber can be anywhere from say 10% more expensive to a 5% savings.
(16:58):
And those are generalities. It can be beyond either of those windows, but that's usually about the ballpark that it lands in. Which then kind of leads to your question about how do you make up for that with rent premiums and all that stuff. And that will obviously vary if we're talking about market rate housing versus luxury housing versus affordable housing, there's more or less opportunity to play with those numbers, more opportunity in luxury, very little opportunity with affordable housing to tweak the rent rates if you will. But certain projects like in Milwaukee like Intro and Cleveland, they have definitely found value in being able to increase the rent rates relative to what's going on from a multifamily market perspective in their areas. We've on our website, website on the WoodWorks website, a series of what we call business case studies where we take an in-depth look at, I think right now we have eight of them and Ascent an intro.
(18:00):
The two that I mentioned are part of that, and basically it's kind of looking at the proforma of what was projected as the rent, what are they actually getting as the rent, and how does that compare to the rent in the surrounding neighborhoods? And it does more than just look at rent, it looks like leasing velocity, how quickly did the building lease up? Has it stabilized and what has there been any tenant turnover and a number of other things. But those are some ways to assess and make up for the cost premiums if they are there. And when there is a rent increase, it's been not insignificant more than say 15 or 20% in some cases.
Adam Jones (18:39):
Yeah, that's awesome. And a good segue into the idea of highrise. You mentioned that's something that you are focusing on. What are the opportunities in highrise? Why would you go as timber and how can we unlock it in this sector?
Ricky McLain (18:55):
Yeah, I think there's a lot of interest and there's certainly a lot of barriers and hurdles to wider adoption in tall projects. I mean, I think in general, again, in the US it's important to keep in mind the context of what is the market opportunity for tall timber projects. So looking at how many projects are built in the US on an annual basis and how many of those are actually what we call tall projects, which has a specific definition, but for generality sake, let's say it's buildings that are seven stories or taller. The market is not huge compared to all of the projects. Most projects that are built are in the say two to five story range, two to four story range, but obviously the bigger ones get more of the focus and attention. So the market opportunity is there basically because even though it's not a huge number of projects, it's like how many of those are timber now?
(19:51):
It's essentially none. There's been about a dozen in the US that have been built, but relatively speaking and can basically say what's the percentage? It's almost zero. So the market potential is huge, right? That's a market that really has not been tapped to date, again, with the exception of about 12 projects or so. So I think that there's a couple things going on in the US that will affect that have affected that and will continue to do so. I mean, number one is interest from developers and the design community. Going back to several things we've talked about already, the sustainability benefits. So a lot of that comes from interest from the designers. They want the design in more sustainable ways, and then developers having pain points associated with, there's a flooded, again, this project in Denver, this developer is building and in a neighborhood that has thousands of multifamily units under construction right now.
(20:45):
So it's like how is project any different? Well, mass timber is a differentiator, so we can market it in that manner. So it provides differentiation in the marketplace as a benefit. So that's one of the reasons we're seeing an uptick in it. But both of those things, interest from the development and design communities led to changes within the building code and changes within the building code are hugely impactful in terms of does a project go forward or not? The us our codes are based on the international building code, which is updated every three years. And so in the 2021 version basically went from allowing mass timber buildings up to five stories to now allowing them up to 18 stories. So it's a huge jump in how tall you could go. So having that cookbook method of if you follow these steps, your project will be approved, has really opened a lot of doors.
(21:39):
And even though not every state in the US is on that version of the code, about half of them are, but even though not all of 'em are the ones that aren't, are usually open to a discussion to say, yes, we haven't yet adopted that code, but we know that it's out there and a number of other states have adopted it and a number of projects have leveraged it. As long as you follow that method, we'll approve your project, that type of discussions. So that's led to, like I said, I believe the number's 13 right now of tall mass timber projects that are already built or currently under construction. And then we're assisting on about 210 additional tall mass timber projects that are currently in design. The vast majority of those are in the eight to 12 story range. I really think that's kind of emerged as one of the sweet spots because it allows you to get in excess of what a style of construction that's very popular here is what we call podium or pedestal buildings where you'll have five stories of light wood frame multifamily housing over say two stories, maybe three stories of parking, retail, amenity space, or even multifamily.
(22:50):
So that kind of taps out at that seven to eight story range. And if you're in that range, that's the most cost-effective way to build usually, but it doesn't allow greater density. So if there's a site and because of the cost of land or the cost of work to be done on the land to get it ready to build or whatever is high enough such that an eight story building doesn't provide enough density to get the return to the developer, what do they have to do? Well, they have to either just not build at all or they have to go taller. And so using mass timber provides a way to go taller, again, while getting this market differentiation, potentially some benefit on the things we talked about with leasing velocity and lower tenant turnover. So it really opens a number of doors that prior to this just simply didn't exist.
(23:38):
It's a new way of building at those heights. And now that with the 2024 code, so I mentioned the 21 code the first time that was allowed, now we have the 24 code, which the big change there was up to 12 stories. Now you can have a fully exposed ceiling, whereas the 21 code, if you went to 12 stories, you can only expose 20% of that ceiling. So now you can go 12 stories fully exposed ceilings. And so that's another reason I think that eight to 12 story project has emerged as one of the most common and popular. And then within all of those projects that I mentioned, the 210 under design, it's also been a very, very heavy focus on multifamily. I think they're roughly 80% of all of those projects are multifamily or have multifamily components within them. So I think that's where we'll see the biggest growth really with tall mass timber is that eight pole story range, multifamily projects.
Adam Jones (24:38):
That's awesome. And you've been lucky part of hundreds of projects I assume, as part of your role. So you will have a lot of projects that start and then something stops 'em, they hit a brick wall and we never see it again. What are those brick walls? What are the things stopping these projects more than anything? And how do you think designers should be preparing for what these brick walls might be?
Ricky McLain (25:02):
Yeah, that's a great question because it does happen a lot. WoodWorks as well as the industry as a whole have taken some steps to try to better understand those to apply lessons learned going forward. I mean, I think you could generally categorize the answer to that question, why do some knuckle forward with the word cost? But there's a lot that's packed into that word cost. Cost meaning just literally it did cost more than the alternatives, and so therefore the developer did not choose to go forward with it. Whether they realized the potential savings of all of the other things we've talked about or not, maybe there just was an opportunity for those things. Maybe it was a perceived cost premium that may have not been realistic, whether it was their cost estimator or their contractor has never used mass timber before, and so therefore they apply some contingencies as one does when you're not familiar with something. And so therefore it looked to be more expensive than it actually was, and so therefore the owner at an early design stage says, we can't go forward with this. It's just too expensive.
(26:09):
So that has been I think a lot of it. So what can people do to avoid some, and there's other things too, but what can people do to avoid those types of things? I mean, the way that I look at cost is through a couple of veins, and again, I like to use analogies. So think about when you want to bake something in your kitchen, you have to buy the ingredients for that thing and the ingredients that you use. You determine ahead of time how many ingredients need, what volumes, what quantities of ingredients. Then you go to the grocery store and you shop for those ingredients and you're looking for a specific quantity or volume of ingredients then, but let's say you have four options. Let's say you're making apple pie and you're going to buy apples. You look at the options for apples and maybe they have different unit costs, and so what's a unit cost?
(27:01):
It's for apples, it costs per pounds here in the us. And so maybe one of the apples is just apples on a shelf and you're going to pick 'em out and put 'em in a bag, and then when you get home, you have to peel them, cut them, whatever. Maybe another option is apples that are already peeled and you just have to cut them. I dunno if I've ever seen this, but just making this up. And then maybe the other option is apples that are already cut and peel and ready to put in your apple pie, those are all going to have different costs, unit costs because somebody's taken the steps to do the work for some of them, so therefore you're paying for that by saving your time. So how does that apply to match timber? Well, it's like timber. There's the volume piece, how much do you need?
(27:43):
And so that can be really tweaked through efficient design. I mentioned earlier the project in Denver going through the process of saying not so much this is the unit layout we want. How do we make mass timber fit that unit layout? What's the most efficient timber layout based on the fact that it's 12 stories, it needs a two hour rating. We want these acoustics performance, right? I'm not saying you neglect all those things, but start with those things and then say, based on this criteria, what's the most efficient timber layout spans and grids and member sizes? And then from there, can we accommodate that by changing the layout of the building sizes and spaces and all that stuff? So that's the way to impact the quantity that you need. In this case, it's how much the cubic meters or cubic feed of timber, the net fiber volume, because that has a huge impact on the timber costs. And then the second piece is that how much does it cost per unit?
(28:42):
That really factors into how you're designing in conjunction with a manufacturer. So understanding the manufacturer's capabilities to be able to do certain cuts, notches drilled drill holes and openings and connection details and all that stuff, A lot of that is necessary, but to the maximum extent that you're able to minimize that work, minimize the fabrication side of things. Again, it costs so much to produce a bare CLT panel, but then it costs more to do a bunch of modifications to that panel. So the more that you're able to modify and minimize those things that you're doing after the fact, basically the lower the unit cost is going to be. And this is also true for things like are you requiring sealants on both sides of a panel? Well, that requires a manufacturer to flip the panels over in their facility, which takes time and money and all that stuff.
(29:36):
So I think that's really one of the ways, not the only way, but one of the ways that teams, if you think about it through that perspective, I think it helps people start to understand how it's not just this is the cost of the material and there's nothing we can do about it. In some ways, yes, that's absolutely true, but there's also things that people can do in design that can impact a lot of those costs considerations, as well as bringing on board experienced people from a construction side, from a cost estimating side who can accurately put numbers to those things so that the cost numbers you're seeing are real and accurate. They're not inflated due to contingencies.
Adam Jones (30:17):
Yeah, That's a very thorough, Ricky, I love that. Going towards the end of the podcast now, my final question, what do you see as the future of mass timber construction going ahead 10 years from now? What do we see as the state of the market and the state of play?
Ricky McLain (30:34):
Yeah, I think that not going to be without its challenges, as in some cases we've experienced to date. I think over the next 10 years we'll start to get a better feel for some of those early projects that were done. What are some of the lessons learned and not just lessons learned, meaning how can we design them better, but how they're constructed, how well are they protected from moisture ingress? What is the long-term? Structural performance and fire durability. I think we know a lot of that through testing, but we don't necessarily have a ton of data because of in-service buildings because we've only had in-service buildings for the past decade or so. So I think it'll be interesting to see how a lot of projects, not a lot, but some projects have embedded moisture sensors and some active monitoring systems, which the data that we pull from those is really in and helping us inform what can we learn from those living buildings, existing buildings, and how can that influence how we do things better going forward?
(31:41):
Not to say that there have been a ton of significant issues, but I think there's always room for improvement and opportunity. So I'm looking forward to that process of continual learning and improving as an industry. But I do think in general that we're going to see increased this really upward trajectory of adoption. We talk about, we have a chart on our website, the WoodWorks website that looks at the number of projects that have taken place per year over the past decade or so, and we refer to it as the hockey stick growth curve. The first 3, 4, 5 years was growing, but at a slow rate, and then it's really started to pick up around 2017 or so to where we are now is really rapid increase in number of projects. And it's not just number of projects, it's the size of projects and the scale of projects. So I do think that will continue to accelerate. I do think the number of projects, like I said, in that eight to 12 story range will continue to grow and accelerate rapidly.
(32:38):
The supply chain is also growing with it as well, so which is obviously imperative to see more. There's a lot of focus right now in the industry on the sustainability side, which we talked about, but more so with the metrics that we tie to sustainability. It's one thing to say something is more sustainable than something else. It's another thing to actually be able to tangibly show that. So there's a lot of focus in the industry right now in helping people understand what are those metrics and what do the numbers mean, and how can we actually assess projects side by side through product DPDs, through whole building lifecycle assessments. So I think that side of things is going to accelerate to the point where I think this is already happening. It's going to happen more. It's going to be the norm for projects to have those metrics, kind of like we know the metrics of what a building's operational energy is expected to be. We'll also know what a building's embodied carbon metrics are, and that will become the norm going forward. And then further adoption of codes, modifications, and what we know through testing and research and how those influence future code changes as well.
Adam Jones (33:48):
Unreal, it's been so good. Speaking to you, Ricky, if people want to find out more about yourself, where should they go? And just before you get into that, maybe just a little plug for your podcast. So I was aware of your podcast for a while, and I think I saw it a few years ago when you first started, and since then it's really blown up. You get an awesome traction on there and it's filling a massive educational gap in the market, which is amazing to see. So yeah, if people want to find out more about that yourself, all of the work you're doing with WoodWorks, where should they go? Did that come through then? Oh yeah.
Ricky McLain (34:30):
Website is just WoodWorks org. Yeah. Yeah, just a couple of ideas on places people is. The first one is the WoodWorks website, so just WoodWorks.org. You can find contact information for myself as well as for all of our regional directors, our entire team, I'm fairly active on LinkedIn, so if somebody wants to connect or follow through LinkedIn, I try to post several times a week just on different topics. And then some of those are also the videos which you mentioned. So on YouTube, the YouTube channeling is Mass Timber, how-tos, and I try to post educational videos there related to just different design topics associated with Mass timber. I don't post there as frequently as I would like to, but as time allows, I upload some videos there and hopeful to just provide value to people looking to learn more about mass timber.
Adam Jones (35:22):
Unreal. Thanks so much, Ricky.