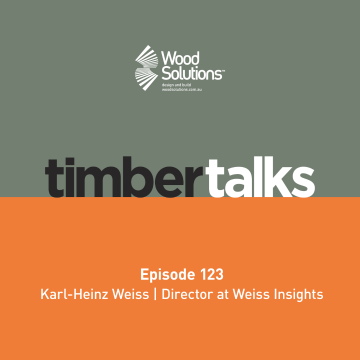
In this episode we speak with Karl-Heinz Weiss from Weiss Insights and WoodSolutions expert advisor.
We delve into the past, present, and future of mass timber. Karl-Heinz, an expert in the field, shares his extensive knowledge and predictions in this comprehensive discussion.
Historical Evolution and Principles: Discover the journey of mass timber, from its early days to modern advancements. Karl-Heinz shares his personal history and background, providing context and insight into the key principles that have driven successful projects in the industry.
Current Innovations: Learn about the most exciting current developments in mass timber. This segment focuses on the latest technologies and innovative approaches that are shaping the industry today.
Future Trends: Look ahead with Karl-Heinz as he forecasts the direction of mass timber over the next decade. His predictions and insights offer a glimpse into the potential transformations and advancements in the field.
This episode offers a unique opportunity to understand mass timber from a holistic perspective, guided by one of the industry's most well-respected experts.
Timber Talks Series 6
Series six of WoodSolutions Timber Talks, provides the latest informative and entertaining information about the best design practices, latest innovations and interesting case studies and interviews with world leading experts in timber design, specification and construction.
Adam Jones (00:30):
Well thank you so much for coming on the podcast, Karl Heinz, I think you were in fact the top, maybe the second or third episode I ever did. We sat down in the Lendlease offices and I think we were talking about Darren W House with Jonathan Evans from sans and yeah, a lot has happened since then. So thanks so much for coming back on the podcast. We'd like to just for you just to go back through your history and your background and maybe whilst you're doing that you can anchor what you've been doing since we last spoke and heard from you.
Karl-Heinz Weiss (01:06):
Thanks Adam. Thanks for having me on your podcast. I have been following your journey as well over the years and again congratulations to what you have been achieving over the last, now nearly seven, eight years when you joined with solutions for a while and went through a few other places on your career and now being with CLT Toolbox and I still remember that podcast we did back then with Thomason Evans about, I think it was actually International House, not the house. So one of Lendlease first mass timber or engineer timber buildings here in Australia. Not the very first was Forte, a library dock, but then followed by international houses as a kind of significant building of scale again and a different building typologies. The first one was residential building, then more public building and then actually a commercial office building. So that goes back quite a few years and over the years I had the pleasure actually being involved in more or less all of the land lease CLT projects here in Australia and had some influence on some of their buildings overseas as well.
(02:50):
That's now was over the last 10 years, nine of the last 10 years I've been with Land, I left the organization more or less a year ago. I think today is the 15th of November and exactly the 15th of November is when I started my last day at Landlease on the first day at Wise Insights. So that's another interesting milestone, but the work with Lendlease started way before actually I joined Lendlease on Forte in Melbourne. I actually sold the timber to Lendlease and not only we sold the timber but provided engineering advice and we trained the in-store crew. And when I say we back then it was KLH UK Limited, so we had been flying people in into the uk, we took them onto our building sites back then out of memory I think must have been some schools or academy buildings somewhere in Norwich and they joined our install crew to learn firsthand.
(04:13):
So that's quite a few years before I joined Landlease. On the second project, the library had the docks. I didn't sell the timber to Landlease but I was involved back then as one of the directors of Timber First Limited because that was in that time when I left KLH UK Limited and we established a consultancy business called Timber First and we provided services to Lendlease. So we got services in the engineering space, the engineering work, and we talk about here the structural engineering. We support the Robert Bird Group as the lead engineer, but we supported Lendees and the whole procurement and the quality quality process. So the whole tender documentation, tender process and then supporting Landlease awarding the contract. And then we did the whole QA procedure overseas because back then Timber first was based in the UK and had a foot in Germany, so it was quite handy to do all the QA work overseas directly. So that's a bit of a summary and you have seen already, there are a few places I mentioned in that summary like the UK, Germany being close to the European market, which is part of my background actually. Yeah,
Adam Jones (06:06):
Well that was planting a seed. I'd say that the Forte building, same with library at the dock, who knows where Australia would be and I guess the world would be because they were world-leading projects at the time and I think you had a bit to do with Stat House as well. So dropping the seeds back then, and I know you had interesting experience even before that, which is related to mass timber, but from there to now, I'd like to just maybe ask an open-ended question in two ways. So in what ways is it growing and there's ways to be optimistic about, and I know Karl Heinz, you're very balanced in your viewpoints. You don't just give roses and daisies all the time, but what are some of the things we need to be really careful about in this space that can risk the growth of the market?
Karl-Heinz Weiss (07:01):
That's a very good question. It will take us a while to work through. So maybe starting off with one thing specifically looking at the Australian market and we recently talked to the FWPA board, so Forest Food Products Australia, we had a short presentation at the Industry Educator workshop last week. Did a short presentation at an event on Wellington Street project in Melbourne, where in reflection I said we can be actually extremely proud here in Australia. So whilst Forte and Library Dog and International House have been probably breaking the ice, you could describe it as such, but they have been actually catalyst projects and very early on we have been saying actually importing timber shipping timber across the oceans is kind of not very sustainable in a way. So if you've got timber resources growing locally, you might want to use these resources. But it became so obvious fairly quickly that there hasn't been any manufacturing capabilities at scale for these kind of products.
(08:38):
And specifically talking about glue laminated timber and cross laminated timber here in Australia, this has kind of completely changed over the last few years. So we've got now in a way three CLT manufacturers, so a smaller setup in Tasmania. We've got next Timber just started up and we have got Heinz xla already in full swing. Plus there's an entity overseas in New Zealand not that far away as well. So you could say in this part of the world we have got already four players in that space, which is fantastic and this in such a short period of time. So we talk about a 10 year time window and not to forget it's not only about CLT, it's about the other parts like glue laminated timber and they're specifically, again, I've got a few players like Ash Timber doing hardwood glue land. I know Caspin Tasmania are doing smaller quantities of hardwood ggl lama and doing softwood glue lamb and hardwood glue lamb.
(10:04):
It's kind of again great to see the local industry has picked it up and is actually providing actually an outstanding product quality I have to say. So I've been looking around these plants. I still remember I went up to Cedar, the he sawmill and Maryborough well before I joined Lendlease got a bit an idea about their capabilities and what they have been doing is really, really grateful for the local industry. At the same time with the growth of engineer timber or mass timber applications, you'll probably take some resources away from the traditional application, which is a standard timber frame housing market.
(11:07):
And we understand that currently into that market as about a 40% imported product already. So it's already competitive and in a way a congested market. So we have to be always conscious and ask the question, how can we do more with less and less in this case refers to actually can we get more out of the fiber we have got to hand. So that's certainly one point. The other aspects did mention that in the past as well I saw actually I've been witnessing and in a way part of it as well, the capabilities in Australia had been really growing fast. It's not only having our supply opportunities but it's the adoption of product in the design stage, the adoption of mass timber in the development space predominantly driven by I would say the customer is quite significant over the last few years. It's really, really great to see.
Adam Jones (12:41):
That's awesome Karl Heinz. And so yeah, the market is obviously growing and I know while I saw you do a presentation in last year or a few times the 30 years and 30 minutes and there are some other things I remember that we got to be careful of maybe from a design point of view as well and certain things we can do to make sure we're actually getting the best solution for the clients as well. So if you can talk a little bit about that, that would be great.
Karl-Heinz Weiss (13:13):
Yeah, obviously we just touched on the fiber and the resource as a material, but there's still a lot of consideration, a lot of work required in actually getting certainty into the whole design and delivery process. I just this morning put together a few slides because I'm presenting at a panel later on this afternoon and one of the final slides is actually titled Fail Fast. Learn fast is not an option.
(14:04):
So we hear a lot about fail fast, learn fast, especially in the software space and you are directly exposed to that and people tend to adopt that to say, okay, we are on a learning journey so let's tap into that in the building environment we just can do. That's what I'm saying, it's not an option because we creating a physical asset and that asset will house people is providing shelter for people, it's creating a workplace for people. So therefore a failure of structures and failure of building performance in order to learn fast. As I said, it's not an option and there's still so many things to consider.
(15:10):
Fire is one aspect. The bigger aspect is obviously moisture and water increase and the more buildings being built now globally, the more you hear and see about failures of certain structures and that's not going to be unrecognized by insurers for example. They pick that up and say actually is engineer mass timber, are we really certain around the long-term performance of these buildings? And from my perspective, having been involved in way over a hundred buildings, and again touch wood, I haven't had a single kind of customer or client coming back and say the building doesn't work or is leaking, et cetera.
(16:10):
But you have to really kind of not threat carefully is the wrong word. I always tend to say if you're an re go slowly, which means you take steps much more considered and understanding building physics for example is such an important part. I know there's standards and standards and codes I can describe them here and there. Dimensional Boris describe standards are always designed towards the standards, a lazy approach because it's compliance driven. You just want to make sure you're compliant with that certain standard, but you can be better as a standard because the standard represents or is the smallest common denominator to ensure that actually everybody executing across the supply chain is somehow in the safe space, which doesn't exclude if you build towards the standard, doesn't exclude failure in other areas. And one of the areas certainly call it in the building physics space is moisture.
(17:44):
Our initial reaction of the industry is say, okay, if moisture is a problem, let's treat timber. My question, subsequent question is always so does actually the treatment of timber solve the moisture problem in the first place. And I used that example with the New Zealand government where actually treated timber is deeply embedded in the standards and the codes. I asked the question, so why you're making treatment mandatory? The response is automatically we have got a leaky arm problem and if you go apply the same principles, it does treatment solve the leaky harm problem. It doesn't, but it just extends the lifespan of the product but it doesn't solve the leak in the first place.
(18:47):
The same is with condensation, et cetera. So that's certainly something where the industry still has to learn a lot. Very similar to fire. So in fire our immediate response and Australia went through that process in encapsulation is the because timber responds to actually fire, it's not the source of the fire. So it's a response mechanism and will eventually start burning always depending on the file, if the file load as well, if the file load lasts long enough for then the structural tempera to catch fire. Our response is kind of again encapsulation. A lot of people are still working on the possibility of treatment. But again taking a bit of an insurers or end of view is why is there a fire in the first place? So what is the root cause of the fire?
(20:01):
And if we look into what's the most common cause of a fire is actually electrical issues, call it short circuits equipment, battery charges, some electrical equipment overheating and that's circa 40% of the fire cases isn't in that space. So again, encapsulation protects the timber from responding, but there is still a dependency on the file load in the structure because even if you encapsulate there's a reaction to high temperature over a certain period of time even behind the encapsulation, which then again causes and creates more questions. So what's happening, is there a jar behind the fire ready cluster board? How is that jar impacting actually the timber? Is there a smoldering happening suddenly which hasn't been deducted? And if you look recently what kind of researchers have been finding there is actually a heat transmission from the outside of the timber exposed to heat to the core of the timber over a long, long period of time. And that's an interesting observation. So we have got potential structural failures long after burnout and that as an example just gives you a bit of an idea of the work still required in that space. We still learning,
Adam Jones (22:03):
Well it's still early and I remember the first time I spoke to you about structural design, how do you do it? And you went into first principles and you are doing it again with fire and moisture and things like that. It's like when you get to a problem finding what's the root get underneath everything and there. So it's a key pattern I've noticed potentially in your thinking to a lot of these things.
Karl-Heinz Weiss (22:28):
That's probably my another
Adam Jones (22:28):
Question,
Karl-Heinz Weiss (22:30):
German genetic, I think it's German.
Adam Jones (22:31):
Yeah, I think you got the German style I think and maybe the hand, you didn't mention your history of back in the cabinetry, but I think when you actually go down to that level and you're used to that and you scale up to the building level, maybe that's what comes with that. And you've been part of a hundred projects Karl Heinz. So you mentioned some of the technical problems there. There might be some advice that you have for anyone else in this space on their projects that make them successful. So from your perspective, what are the keys to make a project successful?
Karl-Heinz Weiss (23:14):
First of all, you have to understand why do you want to build with timber? So you have to ask yourself the question. Then you have to allow yourself to learn to a certain extent and the learning can happen through all sorts of channels. Listening to your podcast as an example of joining seminars, the same time it's actually communicate there is now here in Australia is an active, call it community of practice so people have gathered experience. So tap into that experience. And the other part is certainly look at the project lifecycle. So project lifecycle is not only isolating the design, you have to look into a design, engineering, the whole process around the delivery and understand as well how are components manufactured, how they arrive on site, how they're going to be assembled, how it's timber potentially exposed to weather during that phase and taking tend to say a deep collaborative approach in the industry, in the construction and build industry and in the design industry we used to work more or less in isolation and we see having to engage with a structural engineer as a necessity and not as an opportunity to learn from each other.
(25:18):
And that's actually why it's worse as well. So I'm responsible for the architectural design, the expression of the building. I'm responsible for the numbers and so the structure works and I'm responsible for the delivery and assembly part. There is still too much silo behavior and too much demarcation. So what we have seen in the past is once you really embark on that, what I call the deep collaboration from day one, then actually projects can be very successful. And to my very own surprise, I still hear people talking about early contractor engagement as being a key to success. If I go all the way back to my time at KLH uk, we have done this without naming it as such and you may call it a bit of naivety because we went in and say the architect expressed want to do this in timber, say we are here, we are here to support you.
(26:39):
And we laid out everything on the table where we are on our journey where the architect is on the journey, we'll look together who is a good engineer to support and now we are actually all align on the objective. So Stass Murray growth is a good example where the builder, the architect, the builder was to development at the same time the architect, the engineer and back then in KLH UK Limited had been sitting at the table every single week in that design process. And we went through not only how we solve that structurally, what are the acoustic challenge, how can we really get to that short delivery. The start mar graph, the structure was built in nine weeks.
(27:45):
It's always a funny story around the nine weeks because he had been put together by German carpenters and the German carpenters had been flying in Sunday night and they left Wednesday night because the scaffolder had needed about two and a half days to be another floor ahead of the in-store crew. So they came back, put another floor up, went back home, the store tried to plan, we tried to schedule and we still 2008, we had a lot of unknown. So that building could have been installed in half the dawn at the end it was about 11 months from start on site to completion and people moving in, I think people moving in. We are now mid November, so I think people moved in beginning of December, 2008, so that's about 15 years ago.
(28:53):
So that was even from a builders and developers perspective, quite a success. And I'm still saying we could have been much faster. And this is based on actually understanding not only focusing on the timber structured driving program, but understanding actually it's how do you procure your windows? How much trust do you have in your three D model and can you actually procure material way upfront status? Margrave is such a great example where the window supplier insisted on onsite measurement and they said you've got an Excel spreadsheet, the architect is underwriting that spreadsheet. You've got no risk other than you can say the dimensions are given by, I'm happy to place the order. So that's looking into all the other parts coming with the structure. The same with the facade system. Everything can be procured way upfront. So it's, I've got a real assembly process actually on site. Again, if we look into recent projects, land lease had been building with international house, long waiting time for the facade to arrive, big time loss there. 25 King Street was a great example where actually facade was the building envelope was actually chasing the super structure. So the facade was up actually just below the life deck. And I thought that's actually a great outcome. But again, if we then look into how the services have been procured was in a very traditional way and even the services supplier have been saying, if we would've known that this goes that quickly, we would've taken a different approach to services.
(31:12):
So there is still a lot to learn, but that means you look across or you look into every interface between the different disciplines and different trades, it's probably more intense for the whole project team, but it's so rewarding to see how things go together faster and how you have to struggle less with waterproofing. Again on the T three Collingwood project, a great example as a project, but water management during construction really, really hard. Yeah, really, really hard. The
Adam Jones (32:06):
Same challenge that keeps popping up on a lot of projects, it's always on this podcast. So you've had 15 years ago was Mary Groves house, and where do you see things going in the next 10 to 15 years? I know this might be top of mind, but what are the sort of mega trends and where do you see this industry growing to and what does it look like going forward?
Karl-Heinz Weiss (32:33):
Good question, Adam. I’m just looking around if I've got my crystal somewhere close, there is a huge uncertainty at the moment because we've got the geopolitical situation, which is getting more and more tense every single day. So that's one thing which makes that prediction hard. At the same time, I see regardless of where I look, the financial review, the newspapers, LinkedIn, et cetera, you see more and more companies stepping up and saying we need an ESG manager, which is a big shift just in the last two years because two years ago nobody was talking about ESG requirements. Now all the European suppliers [even here in Australia] businesses taking the ESG compliance requirements very serious. And I think that's where one of the biggest change drivers sit is actually in the incentive which sits behind the ESG compliance and in very simple terms it means it's a requirement coming through the investment world and if you're ESG compliant, you get access to cheaper money, really very simple terms, in ESG, you got environmental, social and governance.
(34:17):
And that's where I think the biggest driver is going to be. We see already decarbonization of construction industry as a direct response to ESG. So why are big companies setting their carbon targets saying by 2025 and we're going to be net zero by 2040 we are going to be absolute zero because they understand the investment incentive - big time. And that's probably one of the big drivers. That's why you see the Atlassian building coming together, where you see even the C6 in Perth has got the strong environmental aspect. People appreciate and want to live in a more sustainable way. People are more carbon conscious and they're happy to even pay more to a certain extent for them.
(35:37):
And that's why we have to look very closely. Again, it will be a question of resource availability and how we satisfied this rapid growing demand in that space. Obviously governments and local communities changing their strategies. That's the other aspect. Obviously circularity, it sits even within these ESG requirements, even to a point where saying natural, natural resources are proven available, full stop. There's no more discussion in that space on circularity is an expectation. So there is, it will be very interesting how the industry as such can respond to these changes not only from a resource perspective, but from a procurement approach, from a design approach, from a collaboration approach, from a thinking in a circular context. What I'm seeing at the moment makes me a bit smile because we think immediately, oh yeah, if we're going to have a timber building, it's all going to screw together and we can unscrew and take it apart and reuse.
(37:19):
I think the bigger opportunity is actually on the two aspects. One aspect, all new builds should be built in a way so they can be repurposed. It's not about a disassembly perspective, it's about the repurpose. So you build ones and you keep it for a long, long time and you can't repurpose so without having to take it entirely down. And that repurpose aspect is certainly something in the what we typically say in Brownfield or the existing housing stock or building stock. So how can the existing stock being repurposed in an interesting way? I think there's a big opportunity there. And then obviously another big opportunity in the market at the moment is solving the housing crisis in the country, which turns into a bit of a race in a way. Who has got the best solution? And sometimes I wish the industry would just pause and think in a very similar fashion. As I said before, if you're in a hurry, go slowly because we want to make sure that we are able to deliver on what we start to promise and we understand actually what are we delivering.
Adam Jones (39:05):
Yeah, there's a lot in that. Well, it's been a phenomenal conversation, Karl Lines, it's been so good to get to speak to you for a second time. If people want to find out more about yourself, what you're up to these days and if they can get in touch to potentially work with you, where should they go?
Karl-Heinz Weiss (39:24):
Let's check out my LinkedIn profile wise insights or go to wise insights.com, my homepage.
Adam Jones (39:35):
Thank you so much, Karl Heinz. We'll leave it there.
Karl-Heinz Weiss (39:38):
Great, great pleasure. Much more to say of course, but maybe another time
Adam Jones (39:45):
We'll get you on again for sure. Cheers.
Karl-Heinz Weiss (39:47):
Perfect. Thanks Adam.