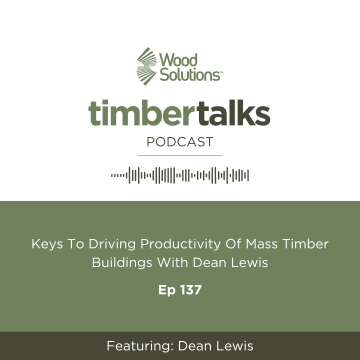
In this episode of Timber Talks, Adam Jones engages with Dean Lewis, Director of Mass Timber at Skanska, who boasts an impressive global portfolio in mass timber construction. Dean shares insights into the evolving landscape of the timber industry, driven by the push for decarbonization. They discuss the pivotal role of productivity in mass timber projects and explore key developments, including the 2024 International Building Code (IBC) changes and their impact on the industry. Dean also highlights several significant projects, the importance of early project involvement, and the promising future of mass timber innovations.
Timber Talks Series 7
WoodSolutions Timber Talks podcast is back for series seven with our host Adam Jones, Australian engineer and founder of CLT Toolbox. This series offers a blend of informative and entertaining content focused on timber design, specification, and construction. The podcast features discussions with leading experts in the field, presenting the latest design practices, innovations, and intriguing case studies.
Introduction (00:07):
Timber Talks is brought to you by WoodSolutions. Stay up to date with the latest in timber, the building material that is strong, safe, and sustainable. Here is your host, Adam Jones.
Adam Jones (00:20):
We're experiencing a time of fast innovation and growth in the timber industry, driven by the mega trend of decarbonization, and today we're lucky to be speaking with Dean Lewis, director of Mass Timber from Skanska, who's got one of the most impressive portfolios in mass timber construction globally. So, in this episode, we explore the potential of Mass Timber program, discuss key conversations needed at the start of projects, and discuss the most exciting developments in the mass timber industry globally. Dean also highlights recent innovations and shares insights on the future of the industry. I had a lot of fun speaking to Dean. He's one of the most knowledgeable people I think I've had on the podcast, so I know you're going to really enjoy this episode. So, without any further ado, here is my conversation with Dean Lewis. Well, thanks so much for coming on the podcast. Dean, can you start by telling us a little bit about yourself and what you do?
Dean Lewis (01:14):
Well, thanks for having me. Been a fan of this podcast for a while. You got a lot of huge names in the Mass Timber community on here, so it's an honor to be on here. Yeah, Dean Lewis, director of Mass Timber for Skanska. Joined Skanska just this past year. Prior to that was a structural engineer for about a decade. Then joined Swinton's self-performed Mass Timber Group, AKA Timber lab, and then from there went to Sidewalk Labs, the offshoot of Google, and then came to scans Scout.
Adam Jones (01:44):
Wow. That's one hell of a resume. So as a director of Mass Timber, what are the things that you are focusing on the most right now to drive?
Dean Lewis (01:53):
Yeah, I mean there's a lot of different aspects to it and really fortunate to be in the position I'm in because we've got a heck of a team supported by hundreds of people that are working on these projects. Everything from the pre-Con early stages, project development, and then in the project operations, and then our own self-performed teams here in the Pacific Northwest. So the duties kind of range as our projects range across the United States because all offices kind of have different markets that we're in as well. But the majority of our projects, public work, civic work, higher ed, K through 12, obviously aviation work is a big one in the Pacific Northwest. Yeah, duties range. Basically, anything that's mass timber and from the beginning, early stages of the project through execution, building closeout, building acclimation, and making sure everything is carried out properly. There's a lot of details that go in between, but yeah, it ranges because in the Pacific Northwest we self-perform the work and so we actually have a composite crews of, we are signatory to both carpenters and ironworkers, and it's amazing to see those teams work together and work side by side and utilize their talents where they're best fit, but then outside the Pacific Northwest still CMGC and manage those projects from inception all the way through execution.
Adam Jones (03:19):
Gotcha. Well, tell us about some of the projects that you've been part of recently and that have been exciting and worth mentioning.
Dean Lewis (03:26):
Yeah, absolutely. I mean, when I came aboard Skanska, I was actually kind of surprised. We had a pretty big portfolio of master projects already, and so now just this past year we've done 22 projects across the United States. The majority of those in the United States, or sorry, in the Pacific Northwest, and eight of those were done last year. Six of those were in the Pacific Northwest, five of those were self-performed and in each one a little bit different. We've got a project out in Princeton where we did NLT with our team out there, and then we did the Cincinnati Public Radio, which was a great project with Nordic with a turnkey operation. And our team that Cincinnati Public Radio, almost 500 individual pieces and it was just a 35,000 square foot building, but almost everything was timber, the stairs, the elevator shafts, the walls, columns, beams, floors and roof were mass timber.
(04:23):
So very unique project there. And then definitely the Center for Deaf and the Heart of Hearing Youth and Vancouver, Washington where our team self-performed that work and completed install in just over three weeks. And so that was a project where the owner was very passionate about utilizing timber and also just kind of a special one. I mean the schools, the K through 12 and the schools like this or the civic centers where you get to see people’s reaction to the timber. Mithune was our project partner there and they did a really good job of involving the students early on to make sure that we designed the building appropriately for deaf and hard of hearing individuals. And so just a really cool story there, and if people want to see that building, they can go to our website. There's links to that project which are pretty unique.
(05:09):
And so that was a really rewarding project. And then probably to top it off just a small one at the eight in Bellevue, so there's a tall steel high rise right next to it, but outside of that high rise, there's a little pavilion building and that was Skanska CD, our development teams first mass timber project in the USA. And so, we were developer, GC and we self-performed the erection of that small pavilion structure. And so small but mighty is a good first step for us as we try and grow our portfolio at Skanska Mass Timber.
Adam Jones (05:47):
Fantastic. One of the topics we want to dive into today is this idea of productivity because it's the one thing that if there is a possibility of a triple bottom line, we all know sustainability is there biophilia, but productivity is the key to driving speed and everything like that. So, start at the high level, what do you see as the keys of productivity and what are some of the horror stories of where it doesn't go? Right.
Dean Lewis (06:11):
Yeah, and I think the key thing that I've learned in doing projects is that the mass timber is important and everybody focuses on that, especially teams that may have not executed a project before and they want to know the nitty gritty of how everything works and that is true to success, but oftentimes more than not, it is actually the items that are adjacent to the timber or ancillary to the timber. Anything that engages, if it's the steel or it's the concrete core or it's the exterior glazing system, the stairs, the elevator, those are the items that typically are not coordinated to the level or depth of the timber, and that's actually what slows us up. And so, it's what I've seen a lot in my career and I'm trying to focus now on Skanska because you can be the hero and top the structure out and mass timber and everything goes great and you're maybe 20%, 30% ahead of schedule depending on the project, but it's really the overall building execution. I feel like that is key to actually pulling a project off and making it successful and making sure that the whole project's successful, not just that one aspect of it.
Adam Jones (07:18):
Yeah, I mean, whose responsibility is this? So, take it to the very start of the project. When plans hit your desk, when are you getting involved and who's driving the responsibility from the very start to the projects successful?
Dean Lewis (07:30):
Yeah, I think it ranges and it ranges from project to project, project teams and then the region of projects. I think the early days it was a lot different. We only had a couple suppliers here in the United States and we're actually utilizing suppliers from Canada. Structural and minority at the time were the only couple suppliers that we had available, and so that was a lot different. We were going to the source and saying, okay, we're going to make this building fit you, and now we're able to be maybe a little bit more ubiquitous and teams are now trying to design and think ahead for success with mass timber, which I think is key because the layout, the grid, all that stuff, getting your cubic footage per square foot down, being conscious of the piece count, those types of things our teams are becoming more educated on.
(08:19):
But still, there's critical choke points for us that are key to getting involved early. And it can be what's the building type, what's the building layout, what are we choosing between the building type? Is it type three, type four, what classification we're going to use because there's implications there, especially when we get into taller timber buildings. You go above 85 feet now in the United States thanks to the new codes and those enhancements, but there's actually a lot of gray area in the code in terms of what we have to do in terms of fire protection as we're erecting the building. That's really critical to pull off, and that goes back to my earlier statement where the timber is one component of it, but if you look into those fire codes, we have to follow the timber up the building. We can only be only four stories ahead of our exterior enclosure and passive fire protection before we can advance another floor in the mass timber. And so, it's like a key point. You can be a hero with the mass timber, but you really need to be the tide that raises all ships and make sure the whole project's successful. So yeah.
Adam Jones (09:22):
Gotcha. And in terms of program savings, so let's say if things do go well and you look at the program holistically and not just the mass timber installation, what are some numbers to strive for in speed? This is something that I hear very varied numbers pretty much everywhere around the world, I'd say.
Dean Lewis (09:42):
Yeah, and I think it depends on the project type. I think early days we were trying to prove that mass timber had speed and it was hard to do that when we were below 85 feet. We were probably three or four stories and we're still in buildings that are 30,000 square feet or 50,000 square feet. Now we're getting into these bigger projects where we're able to acclimate that a little bit better and show, hey, over 150,000 square foot building, we're saving at least two to three months and we're maybe 20% faster on schedule. And that's something that's in the eight to nine story range, and that only can get better potentially as we get up to the 18-storey range. The best example of that, I know woodworks to the great series here in the States on the 1510 Webster project does 18 story point supported, so a little bit different layout, and the one that we were looking at was a nine story 150,000 square feet, and we had a post and beam layout, so a little bit different frame strategy, different height, different piece counts, we had lower piece count than data, but all those types of considerations.
(10:49):
But on average you'll find a lot of literature out there and it'll range from 20% faster to maybe 40 or I've heard some people say 50% faster. But I think it really depends on the building layout, the height of the building and those types of parameters.
Adam Jones (11:05):
What are the sort of conversations did you expect to have at the start of projects? I mean, you mentioned a few times piece count, which is maybe obviously some but may not be for others, why something like that might be important, but yeah, also in general, what's the optimization function that we're going for at the start?
Dean Lewis (11:21):
Definitely, I mean the layout and the grid and getting that cubic footage per square foot down. It's interesting. Been seeing a lot of presentations and numbers flying around and quantifications for that. So, in the states I saw the USDA's latest report, it was saying they're shooting for an average around 0.6 cubic feet per square foot. And again, that depends on the product type because if you're in a type five B where there's no fire rating and you're maybe at a 90 mil three ply, the really efficient layout maybe around like 0.45, 0.47 cubic feet per square foot, you're screaming, you're doing pretty good. If you're in the type four Bs, your 12 stories, which is kind of the hot topic right now here in the states, we got the 2024 IBC where we can now expose it to 12 stories of timber. You're going to be in around 0.8 cubic feet per square foot.
(12:16):
It's hard to have a project be below that because you're trying to expose the timber and maybe you're doing a hybrid like Baker's Place is doing where you got steel mixed in with the timber, so maybe you're reducing your cubic footage per square foot, but now you've got more steel. So I think that's the first aspect of it is to get that cubic foot per square foot down to reasonable level, but not something that's really going to inhibit you from an overall piece count where you've got really small panels and you're having all of a sudden, especially on a tight site, you're looking at how many trucks can you get in per day? What's your loading zone? Are you only going to be able to get in one to two trucks? Can you maximize it? Do you have lay down space you can try to get three to four trucks in because all of a sudden that really starts to be the driver for a project. Then overall building layout too, like the core, are you going to have blindside picks because your crane's going to be on one side of the building, and you got to come across that core to the far side and it's going to slow you down a bit. Those are other things to kind of look for and as you're starting to plan the building out and how you're going to operationally pull it off, I think. Yeah,
Adam Jones (13:26):
Yeah. Tell us a little bit about the 2024 IVC changes, and just for context, I don't know how lucky or not lucky, but how good it is in the US in terms of the codes you've got. Because around the world we look on an envy with when you say 12 stories exposed as a deemed a. Yeah. So, tell us about that code change and what that looks like.
Dean Lewis (13:49):
Yeah, I mean, we are really lucky and we're lucky because it's been a multitude of individuals across not just the United States, even the 2024 provisions was an international collaboration. Obviously even from the early years, the PRG three 20 standard is a binational code committee. It's Canadians and Americans, and they've had other entities internationally come in to give presentations on the adhesives and other fire testing that they've done. And that's from the early 2000 tens up to where we are now. And so, it's really grateful for hundreds of individuals that have put forth the effort, put in the research and are kind of our own little timber craze to get to where we are today. So yeah, 2021, we were granted the access to have a cookbook of like I call it, because you can do a performance-based design, you can do an alternate means of methods, but here in the states, typically we have prescribed design where it's basically a cookbook says now you have an option to go from eight to 18 stories.
(14:54):
I think that's been pretty well documented, but what's going to be changing now is the 2024 IBC, which is part of the challenge for timber I think across the United States is that that's the international building code. That's great, but the rate at which states and cities and jurisdictions adopted is different. So that is a challenge to note, but that 2024 IBC, it's kind of a good coalescence with the code because there's a couple things that may be good to talk about. So first you have up to 12 stories, you can fully expose the structure. There's also another edit to where we used to have to add a non-combustible one-inch layer on top of the timber as we're moving up the structure, which isn't much. But again, we've got so many other requirements on us from a GC perspective that it just added one more layer of things that we have to think about as we're erecting the structure.
(15:45):
And so that was alleviated and that was thanks to testing from Rise out of Sweden. And so yeah, a lot of this stuff though is going to coalesce because a couple other things that are happening. So, the 2024 IBC actually kicks us into the new structural code, the A SCE 7 22, and depending on where you're at in the United States, I mean mostly it's going to affect seismic regions. So East Coast doesn't have to worry about it as much, but you could see here in Seattle where I'm located, you're going to see an increase in seismicity by about 20%. And so, you think about mass timber versus other materials and the lightweight nature of the structure for mass timber having a huge advantage. Now, it also affects the foundations naturally, but from a seismic standpoint on the west coast, that'll be big. The 2024 IBC as it kicks you into the new structural code also kicks you into some new provisions in the concrete code, some which are already in effect, but essentially there's an over strength factor on the shear capacity for concrete shear walls.
(16:45):
So now concrete shear wall cores, which we've commonly seen across the United States for high rises are becoming a little bit more inhibitive. And actually, a lot of structural engineers are starting to do performance-based design to get those cores back down to a reasonable size. So that's going to be coming into effect. You're going to start to see more of that. And then some other cool features is obviously with the new structural code, there's the allowance for CT share walls, that'll be in a SE seven, some states, some jurisdictions already allow it, but now it's going to be cut and dry in there for teams to use. And so yeah, a lot of exciting developments that are going to kind of help mass timber get a couple more advantages to where back in 2015 IBC, I think CLT was first introduced into the code, so municipalities could actually say, oh, it is right there across the May timber. Okay, we can use it to know all these other advantages that we have to put us at a level playing field.
Adam Jones (17:46):
A hundred percent. That's phenomenal, man. And what about from a fire point of view? How is fire treated in this cookbook approach as you go taller?
Dean Lewis (17:54):
So, as we go taller, the fire ratings get more restrictive. And so, in 2021, we could only expose 20% of the ceiling or 40% of the walls. Now we can expose a hundred percent of it, but we have to have a two-hour fire rating. And so that'll be key for these type four Bs. And that's kind of the game that we're seeing where we're looking a lot at residential structures. And in residential structures, you have your drop ceilings and your bathrooms, closets, kitchens, portions of the kitchen just to facilitate ducting. And so really you're not going to expose a hundred percent of the structure. And with that, not only the ceilings, but also maybe the columns or the beam elements. And so, we're kind of seeing an interesting trade off of where the timber makes sense to expose it and accentuate it, and maybe other areas where I've seen steel being mixed in. And so yeah, that's kind of the tradeoff that we're seeing as we're moving into these type four Bs in a residential setting at least. Yeah,
Adam Jones (18:58):
I'm keen to hear your thoughts on, I mean, because going from Sidewalk Labs where it's very, I guess trying to invent a future, not putting words in your mouth, so correct me on that, but that's like the outward looking, you're on the ground, you're doing practical, you're driving real as a general contract, what practically needs to get done. So, one of the things we've heard on a lot of podcasts is like the whole industry knows it needs to change, but there's also this practicalities of what's the reality on projects and you need to drive, you know what I mean? So, there's this dichotomy it seems. Yeah. So, what do you see as the keys to that next Big Leap innovation from your perspective of where you are sitting right now? What does that look like?
Dean Lewis (19:39):
Yeah, I think just to maybe touch on the Sidewalk Labs thing, I mean, our team at Sidewalk that was focused on master buildings was actually called Canopy and Canopy, if you want to know the origination of that name, just to, you can get a feeling of how forward thinking these individuals were. They had big ideas. So, Canopy, the original idea was to actually build a canopy or a dome over an entire city, and that way you could actually create an internal climate and control not having to worry about rain coming in and windstorms and all these other events that would happen to buildings. And so overall, you'd make your buildings more durable for a longer period of time. Again, a very outlandish thing to think about, but that's actually the origination of the company was Canopy. So that's pretty wild. And so very fortunate to have that experience and actually be able to stop and ask the of why, but also have the resources to ask why and work with some very talented consultants and do a lot of testing.
(20:55):
I mean, we did 26 different tests on our kit of parts. We built our two-storey mockup of three bays of our cassettes, and we tested that to some of the most robust tests that are out there and disassembled it and rebuilt it twice, or sorry, rebuilt it three times, disassembled it twice. And so, when people think about where the industry is going and where the advancements are, I definitely think that's one thing that mass timbers maybe not get enough credit for is the design for disassembly aspect. People kind of think, well, that's not reality. It doesn't work like that. I mean, does, there's another project actually in the states that red brick did with structure craft, and I'm trying to remember the team that put that together, but that structure is designed for disassembly, and I believe it is temporary. And so, there's other examples with homes and Hilti and their connection systems, and there's all these other proprietary connections that are being developed.
(21:55):
And so I think that's something that as the industry develops, that's going to be a great resource for us because especially when you think about the LCA analysis and the carbon story, for a lot of these ESG investors, there's a question about biogenic carbon, and at the end of that building's lifecycle, how much of this material are you going to be able to reuse? And there's cases out there where potentially almost a hundred percent of it can be reused depending on its application. So, I think that's one big innovation that the industry can look forward to. I still think with builders risk insurance being a premium here in the states, we face about a four x to five x premium over stealing concrete. So, we need to do a better job of education. And there's already great efforts underway both between the US and Canada on trying to educate the builder's, risk insurance, the carriers, insurance carriers, and mostly the concerns there are water and fire.
(22:51):
But just on the PRG three 20 committee where we had the incident at PV Hall, basically we put in measures that were better QA and QC on the overall product and made it more robust in the end and gave us better quality assurance and quality control so that we could make sure that things were being manufactured properly. And so, I believe it's kind of like you're forming this pearl, and you got the carbon and you're just putting more and more intense pressure until you're going to make overall a better product. And I think that's what's going to happen with mass timber. I mean, we're still very early in the industry and developing the codes are still developing. And so, I think, yeah, those are maybe a couple of the top things I think we need to work on.
Adam Jones (23:33):
Yeah, that's phenomenal. Was that an analogy? Pressure makes diamonds sort of thing. Was that
Dean Lewis (23:39):
That's where I was going with that. Yeah, yeah,
Adam Jones (23:40):
Yeah. No, that's a great analogy where it's like, you're right, it's like early days and all these challenges and problems that come up, but a lot of the time, I'm sure the high-rise concrete buildings had the same problems when they were just starting out some problems, and over time it just becomes a mature industry, and the cost curves improve. And is that also what you're seeing? You're seeing sort the green shoots of the stories of a cost point of view, and I mean, is that still the major driver of the industry? It's like sustainability is one of those things that everyone says they want and it's good at the start of the project, but then when the reality is like the QS comes back with a price sometimes. So yeah. How is that dynamic playing? Yeah, it's
Dean Lewis (24:20):
A good question. I think you're right on. In the very early days, people were paying a premium to do these timber projects because they were kind of the first to market. They were getting maybe a premium for rents or they were getting kind of the marketing off of that project. That's definitely gone, right? I mean, it's rare to see a project now these days being able to claim they're the first of something because almost in every state, in every city or major municipality, there is a mastermind project. So that's kind of done and gone. And so, then it was, now it's mostly price of why people are trying to figure out how to do these projects. Is it faster? Are we saving on foundations or are we able to get to market faster than some of these other projects? But I do notice that the sustainability story is starting to pick up more momentum.
(25:09):
And just the Portland expansion that we were doing where we've got a huge collaboration with a number of industry partners that Portland Airport is going to stand the test of time, I mean 2.6 million board feet and all of it traced and sourced locally within 300 miles. That's an amazing feat that when teams really start to look at that, that is a tough statistic to beat, especially for a project to that scale. But now that story is starting to be replicated over the six 19 ponds project over in Atlanta. That team did a great job kind of locally sourcing the timber and getting the manufacturers there to hold the trucks over the weekend so that they could process the timber and track that from force to frame. I mean, that's a great story as well. And so, I think there's more stories where people are taking pride in knowing and being able to trace the material from its source. And so yeah, I think it's changing a little bit.
Adam Jones (26:07):
Phenomenal. And looking forward into the future, what do you see as the future of the industry just being fully open-ended with the question. Take it as you like.
Dean Lewis (26:16):
Yeah. Well, you're asking this at a good time because I think we are going through a change. I think in the beginning, yeah, there were a lot of smaller projects and then definitely the hot product type for mass timber for a while has been office, a lot of mass timber offices. And it was great, and it pushed the industry forward, but now obviously with the market the way it is, offices maybe not as hot of a product for a lot of projects in general. And so, I've seen a lot of inquiries come across my desk for a lot of different product types, police stations, aquatic centers, rehabilitation buildings for young youth. We did our Center for Death and Heart of Hearing out of Vancouver, Washington. That was a very unique building, which we're proud of. And so, I think you're going to see a lot of different types of buildings be utilizing mass timber, which is exciting because I remember when I took a trip up to Canada over a decade ago, and that was kind of the story that I saw up there.
(27:16):
They were just doing all types of buildings out of mass timber. And I feel like if we can get to that point in the states where we've got all different types of structures out of mass timber, there's not a certain, oh, your building needs to be 12-storeys, residential type four B, that's the hotspot. And that might be, and maybe that becomes a growing methodology of building, and I hope we do get to a point where we can home in on that and just make that almost a standard where it's not even being thought about. It's just, oh, your 12 stories, you're residential, you're in a seismic region, boom, that's a master timber building. That's kind of where we should go to. But I feel like we should also be expanding into all these other different types of projects and not the whole building will be matched timber.
(27:58):
I think there's a lot of hybrids out there, but we still got a lot of projects to do. I mean, in the United States, I think we've got over 2200 projects now, and we're somewhere around two to 300 projects a year. I think the research that woodworks Bill Parsons and his team did, I think there's around 17,000 multi-story projects a year, and that comes from Dodge Analytics. And so, we're still one to 2% of the market, so we've got a lot more to go. So, in the next few years, it's really just about doing more projects, like there's more opportunity out there and just more projects at all scales need to be done.
Adam Jones (28:38):
Yeah, phenomenal. What an exciting future with gobbles. Thanks so much for coming on the podcast, Dean. If people want to find out more about yourself and Skanska and get in touch for any projects, where should they go?
Dean Lewis (28:48):
Yeah, if you want just Google Skanska Mass Timber, it'll take you to our Mass Timber website where we got a couple tools there. We've got our mass timber trivia if you want to check that out, feel free to connect.
Adam Jones (29:01):
Amazing. I never heard of Mass Timber trivia. I might jump in there as well, but thanks so much, Dean. That was absolutely amazing.
Dean Lewis (29:07):
You're welcome. Yeah, thanks for having me.
Adam Jones (29:23):
The world is definitely moving towards sustainability, and if you want to measure it, then the best practice way of course is EPDs environmental product declarations and wood solutions has industry-wide EPDs for GLT, glulam for just simply saw, and timber for hardwoods for CLT. So, these EPDs are an immensely important resource, so I highly recommend going to check 'em out and using 'em for your projects.