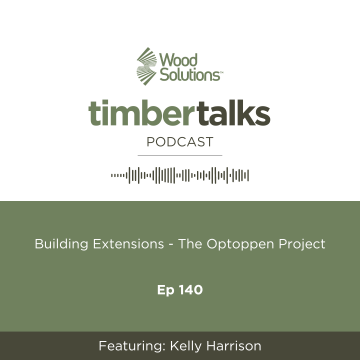
In this period of rapid innovation in urban development that is driven by the need for sustainable use of space, we're chatting with Kelly Harrison from Whitby Wood. Kelly tells Adam all about the Optoppen Project's mission to transform urban spaces using rooftop extensions. The Optoppen project by Whitby Wood is an initiative focused on sustainable urban development through lightweight roof extensions using timber and other bio-materials. These extensions increase the floor area of existing buildings, contributing to urban decarbonization and better utilization of infrastructure. The project highlights the potential for rooftop spaces to support city-scale carbon sinks, while also enabling energy retrofits. Optoppen serves as a low embodied carbon solution that aligns with circular economy principles.
Adam and Kelly discuss the untapped value on rooftops and address concerns about the structural integrity of existing buildings, examining the reliability of data and drawings. Kelly also shares insights into the growing appetite for mass timber in the UK and her vision for the future of timber construction.
Timber Talks Series 7
WoodSolutions Timber Talks podcast is back for series seven with our host Adam Jones, Australian engineer and founder of CLT Toolbox. This series offers a blend of informative and entertaining content focused on timber design, specification, and construction. The podcast features discussions with leading experts in the field, presenting the latest design practices, innovations, and intriguing case studies.
Adam Jones (00:00):
Well, thanks so much for coming on the podcast, Kelly. Can you start by telling us a little bit about yourself and what you do?
Kelly Harrison (00:10):
Sure. So, I'm Kelly Harrison. I am a director at Whitby Wood Structural Engineer, and I am also on the board of directors for Timber Development UK. And that's through working on lots of projects as a structural engineer that have included timber, whether that be churches or schools or commercial offices or lots of things. So yeah, through doing those, got very excited about talking about them because I was never taught about timber at university and so did that and then sort of got introduced to the whole Timber Development UK and what used to be TRADA and yeah, so that's what I do.
Adam Jones (01:02):
Amazing. And now we're here and we're talking a bit today about the top and project. We're both getting a bit excited, so we thought we better hit record before we just squeeze all the juicy out of the excitement. So, tell us a little bit about what is this Optoppen project?
Kelly Harrison (01:19):
So Optoppen is Dutch for topping up or rooftop extension, which is just when I heard love the word. And a lot of my projects throughout my career have been adding CLT or glued on top of existing buildings. And just when you do those projects, there's lots of challenges, there's lots of barriers. Normally it is quite expensive. Normally it's only done in very sort of dense, high value city center areas where there's lots of conservation areas and listed buildings and reasons why you can't demolish. But just having done them for at least 10, 12 years, you can really see as the engineers that when you start looking at your embodied carbon, those projects are a fraction of the embodied carbon in terms of the structure in any case than other projects. And obviously that then translates up into the whole life carbon of the projects as well.
(02:32):
And so, we were sort of talking about this a lot and saying why is it so hard to do it? Why do so many other where the values aren't there? Why can't we make this work? And what we really felt was that the system needs to change, there needs to be incentives to do it financial time-wise that some bigger system needs to change. And so, talking with built by nature, this Joe Giddings there who's the UK representative, he was like, yeah, I don't understand this either. And then he went back and started talking to his other built by nature colleagues in the rest of Europe and they were getting the same ideas from the Netherlands, from Spain. And so, he came back, and he asked us to project manage a pan-European project to see how we might be able to influence the system. So, we got on a big call with lots of people from the Netherlands and Spain and we brainstormed what we could do, and we decided to create Optoppen, which is a web platform.
(03:45):
It's going to be a web platform at the moment. It's a web holding page, which you are welcome to visit Optoppen.org and it's going to, going to have a tool on there. The way you can put your building in, you can choose which city it is in out of or which country it's in out of the UK, Netherlands, or Spain. You can choose what decade it was built in, what its grid is, what its cladding is, and how many stories high it is at the moment. And it will automatically calculate how much mass timber you can put on top in terms of floor area, number of stories, embodied carbon and stored carbon. So that will give you, show you the potential for one building, but then we want to expand that to see what's the potential for a whole city. So at the same time we're doing a piece of research and we're not saying it is a good idea to add several timber floors to every single building in the city, but we are just showing the opportunity or the technical possibility if you did, how much floor area could you add to a city using this method and how much carbon could you store at the same time?
(05:00):
Could it be that we make our city's carbon sinks and perhaps just by showing that possibility you can start to make decision makers change the way of thinking. Perhaps we could influence policy like some system change we were Optoppen to get out of it. We're also going to have about three – four hundred case studies where it's been done all over. Well, we started off thinking that just from the three countries we're based in, but people have now been getting in touch with us from all over the world. So, we are going to have some from North America, from Canada, from Sweden, from Germany, so everywhere really. And we will want to encourage more of those. So, if any listeners would like to, if you go on the website, there's a link to submit your case study. And also we are going to look at policy and try and pick out all of the exemplar policies from North America and Europe that enable adding on top just so that if we do inspire someone somewhere to want to do something about it, they can see what other people have done and maybe that'll give them some ideas of what would be suitable for their city or borough or council.
Adam Jones (06:19):
Yeah, yeah. Wow, that's so exciting and amazing. It seems like it's already got some legs. So, embedded in that, if you're going into some sort of calculator and you're working out late in capacity, what's the assumptions of how much capacity does a concrete building have? Where does that come from? Do you need to rectify buildings or is there the engineers push? What is there, what's in those assumptions from your lots of experience in this space about what value could be unlocked essentially?
Kelly Harrison (06:53):
Yeah, great question. So, I just want to caveat that the tool is not
Adam Jones (06:58):
Of course it's not structural engineers full design, but there might be a rougher the back of the envelope.
Kelly Harrison (07:08):
Absolutely, yeah, there is. So basically, when a building's built or designed, first off, its foundations are designed for the soil they're going to sit on to settle or sink or move. And that's the limiting factor that drives the design of the foundations. More often than not, as soon as the building is built and the full weight of it and load of it is put onto those foundations, the soil around those foundations consolidates and gets more strength. So, buildings automatically have some latent capacity in them. Now that might not mean that the structure above has the capacity, and I caveat perhaps some of that will need strengthening, but that's a lot easier than strengthening foundations and a lot more cost effective than strengthening foundations. So, we're basing it on assumptions around the foundations basically. But there are especially concrete buildings, the concrete especially, it depends which decade it was built in, but the codes have changed.
(08:20):
There's been inherent overdesign in the past. There could have been a change of use, it could have been a warehouse before or something with much heavier loading could go from an office building to a residential building and also concrete gain strength over time as well. So, there's a bit of later capacity in that too. So, most buildings have whole chunk of capacity in them to add to and to verify it fully, you need to have a proper design team, a suite of investigations and all those things. But we're basing it on a rough 10% increased possibility without unloading anything. But then in the tool there will be options where you can demolish the roof because perhaps the roof isn't good enough to be a floor, so we have to demolish it anyway. And that removes weight and allows more lightweight floors to be added. There might be reeds on each floor that you can remove and if there's a long span in the building, perhaps you can even add another column into the building that might give you a smaller spans inside, but enables you to add much more on top by having one more column row in the middle.
(09:36):
So, we're going to have all those options within the tool as well. And then we potentially also, we're just debating this at the moment, we're going to have a series of round tables to see if it's useful or not, but we're thinking as well because the majority of buildings I've worked on in London and talking to some of our friends in other countries as well, you normally get a lot more than 10% up to 30, 35% extra without any foundation strengthening before. So, we may sort of add that as a, what if it's 30% number as well, just so you get the two to compare a sort of range of best case, worst case.
Adam Jones (10:19):
Wow. So correct. We might just do a guess of factor design load. So, say if you've got a 10-storey concrete building, if you get 10%, which is one story of concrete, which might be two stories of timber. So, if you've got 10 stories, could you get two stories of timber? Is that sort of what we're looking at? And I
Kelly Harrison (10:38):
Think it'd actually be a bit more than that. It depends on the column grid as well and how heavy the facade is and if the facades being changed. So, there's always lots of factors, but the taller building, the more floors you can put on, obviously because your 10% is of a bigger number, the bigger it is to start.
Adam Jones (11:02):
So, who are we unlocking value for here? Is it a new market? So, I guess is it the people who are looking to knock down like, oh, rather than knock down let's just whack on an extension, or they're just latent building owners who just, you can knock on their door and say, did you know you've got all this value on top? So how are you approaching it?
Kelly Harrison (11:24):
I mean for everyone really. I mean what's been really nice is through this project one building in London, a group of residents who lived there got in touch with us and they decided they wanted to club together to do a retrofit of their block, but they needed to get some value to be able to pay for that. So, they asked us to put their building into our tool and see if they could add one or two stories on top to unlock basically the residence as a whole would own and then sell to pay for the retrofit of the rest of the block. So that was a really nice story and now we've already started design work on that for them. They're one of our clients now and they're going to be featured on the website, which is very nice. So, there's kind of a housing thing, and I think retrofit and energy efficiency of existing buildings is a big issue and we're Optoppen that it can help create value that pays for those retrofit upgrades and m and e system upgrades.
(12:38):
So that's very much for existing building owners to make the most of what they've got. But we also have a housing crisis across the whole of Europe, probably the world. And we're also very much in the Netherlands, they are looking at this to unlock the potential for additional housing. In the UK it's a bit more difficult because we have more strict fire regulation around timber at height, so that only works on very low rise buildings rather than the taller ones. It's a bit more possible in Barcelona and in Rotterdam with the other two cities we're looking at. And they're very much looking at how many houses they can provide by adding on top for local housing associations and things like that. Yeah,
Adam Jones (13:33):
That's cool. Well g, you probably, because you focus on this, there's not many people around the world who have done multiple timber extensions, right? It's like a niche that is out there and there's probably a lot of people listening right now who haven't had their first yet. So, what are some of the lessons learned you've had on the projects? And if you can feel free to speak to any specific projects that people should be thinking about if they're looking to take undertake one of these?
Kelly Harrison (14:02):
Yeah, mean there are a lot of lessons. I can't say it's rosy. There are a lot of lessons to be learned. There are barriers and I feel like there's a lot of things I'd love to do to sort unlock those barriers. A big one, particularly in the UK is that we don't have our own forestry and mass timber production industry at scale. And so, the main contractors doing these types of projects they don't have direct contact generally with the CLT suppliers or installers or fabricators. There's only a few that do. So, there's quite a lot of reluctance by main contractors to want to use the material. So quite often you have an extension project, and you'll design it all the way to getting to site and then the contractor will want to change it to a different material. And so, we are Optoppen that Optimum can be a vehicle to make some introductions as well so that they can start working with each other better.
(15:16):
And a bit of lessons learned from those relationships as well on projects that I've had is CLT and Blue Lamb is offsite very precise, hardly any tolerance and an existing brick building from the 1930s with concrete columns inside is anything but precise. It's all over the place and you have to really, really, really think about your detailing of how the two connect, especially if it's going to be exposed because you're going to see it, it has to be fire protected and perform in fire. It has to deal with a lot of tolerances. You don't know exactly where the floor slabs going to be or the wall's going to be or the column's going to be that you're trying to connect into. You don't know what reinforcement's going to be behind the concrete that you're trying to anchor into either. And so thinking about all those things in the design stage and the procurement of the design team and early engagement with the contractor from the client side is super, super important because if you realize all that as I have done several times now when you hit site and the CLT has been made and it arrives, then there's a whole load of panic and delay and everyone's running around trying to work out what the best detail is best.
(16:43):
So that is my biggest lesson learned from working on these projects is you need to do very good survey data, you need to think about all the tolerances and the connection details before you order your CLT and you have to be ready and aware for making any alterations when you get there as well.
Adam Jones (17:04):
Yeah. What about the drawings and the building information modeling and how does that process work? So, I'd imagine 1930s we're looking at like man, a lot of hand drawings maybe. Yeah,
Kelly Harrison (17:19):
Beautiful.
Adam Jones (17:20):
Yeah, they're beautiful and they're probably like, yeah, someone's got to really think about it when they're, because you're not just hitting a computer mouse and hitting delete. You're like got to be bloody sure when you're doing it right.
Kelly Harrison (17:32):
Yeah, absolutely. Yeah. I mean you have to start by, well, it is a complicated process because it very much depends on the existing building who's in there at the moment, is it an office building, is it a residential building? Are the tenants going to be in there when you are adding on top or not? It's very difficult if they are, but it's not impossible. And yeah, basically there's a whole process. You have to get very good survey information, you have to do investigations resurvey, once you've got it stripped out and you can see all of the structure, that's super, super important. And that might mean that you have to do two models. You might have to work off an assumed model for the majority of the design and then remodel once you get the final survey information from the strip out and that will then be the one that they use for all the fabrication detailing and things like that. Yeah, because normally when you resurvey at that point you find everything's just, even if it's not 0.3 of a degree out, it changes all your details. Yeah, that's definitely something I recommend, but I think it is almost impossible when working with Mass Timber to not have a model at all. We need to have some sort of model.
Adam Jones (19:02):
Absolutely. That's great. It's been wonderful talking about the up top and then moving on to just the current appetite of the industry in the UK right now, how is it, what's the general sentiment? What are the biggest talking points, the biggest blockers to the industry in general at the moment, and what are the most recent enablers?
Kelly Harrison (19:23):
Yeah, so we've been through a bit of a journey in the UK for the last few years, I'd say. So, I'm sure people on the podcast may have mentioned in the past, but obviously we would probably one of the front runners in terms of CLT for a while, very large scale CLT buildings. And that's when I was doing a lot of the CLT on top projects. But when we had the Grenfell tragedy, there was all of sudden a lot of nervousness just because a lot of confidence in the whole industry in the UK was lost. What happened there was just kind of crazy, really a failure of the system in terms of people knowing what they were doing with fire. And so unfortunately as timber is combustible that timber construction got brought into that discussion. Now, my experience working with Timber is that we already, because we knew the risk, we were already going through a lot of those checks and understanding the test data and knowing that the third-party certifications were there and understanding the ets, that's been the norm when you design with mass timber for a long time.
(20:47):
And so a lot of it's already there, but we did need to recognize that particularly mass timber reacts differently in a fire and brings a different energy to a fire. So, we can't be using our standard ways of calculating or engineering what's going to happen in the fire. And so, since then a lot of testing's been being done. A lot of guidance risk-based guidance has come out from the Structural Timber Association recently from a, then also we did a part of TD UK with Swedish Wood and the Structural Timber Association. We did a fire safety website, which is great. And so, there's a lot more information out there now and I'd like to think we're getting to a point where we've done so much thinking around that that other countries will start to come to us for that knowledge and hopefully that will soon start to unlock more timber projects.
(21:55):
Again here, know the barrier has been insurance, but we've done a lot of work around that too. The Mass Timber Insurance Playbook by Bill Callow and Jim Glock King has really been interesting. It was part of the reviewers of that. And we were working on a project at the same time where we sort of adopted some of their thinking and then managed to get a sort of stage two, which is the planning stage of a project. We got a meeting with the insurers, and they agreed to no extra premium because of the way that we'd approached the risks. They felt that there was competency and the design team, and they knew that we were going to speak to the right suppliers and installers at the right time. And so, when the Mass Timber Insurance Playbook was released, we sort of presented that project alongside it to show how it could be done.
(22:54):
And really going through all of that is everyone really wanted the same things, just we were talking a slightly different language. A lot of the details and thinking that the designers were doing was exactly what the insurers wanted, but they're just not put together in a report at the right stage or they're not spoken to at the right stage in the project for them to appreciate it. And so, the playbook really spells that out. And so, I think that that's starting to unlock the insurance issue a little. I know that it's not as big a frustration in the industry with it at the moment as there was a couple of years ago. So yeah, I'm hoping that that starts to turn things around too.
Adam Jones (23:39):
Yeah, yeah, definitely a common theme on the podcast, the insurance side of things. So yeah, Kelly, it's been amazing chatting to you. So, looking ahead now, what is the future of construction? What is the future of the mass timber industry? What are the things that are going to drive change and what does our blue sky look like?
Kelly Harrison (24:02):
Hard question
Adam Jones (24:04):
Ask. You've got six slightly nuanced different questions then, so just take any one of 'em
Kelly Harrison (24:10):
For me. Okay. So back in 2020, as Whitby would, we looked at our business and Scope three carbon and we wanted to plot a route to zero. By 2035, we realized that we're too insignificant to actually know what that's going to look like because we have no control over the technological advancements of all the materials, particularly concrete and steel timber's almost there already. And so, we realized that if we really we're not saying we're going to do this because we don't want to bury our heads in the sand, but thought experiment. We want to be there at 2035. By 2033, we're going to have to stop working on anything but refurbishment projects and timber projects. And so, joining those together into an op is the kind of ideal project. And looking at the structural embodied carbon of some of those projects, we are meeting the Institute of Structural Engineers targets for 19, 20 40 already today. So, what we need to be doing is really rather than just carrying on a normal and Optoppen someone's going to make a technological advancement to decarbonize concrete, at some point we need to start, we're on an exponential curve in terms of temperature. We need to be doing the best with the low carbon materials we've got right now. And then when that innovation happens, embrace it. But I feel like the future is using what we've got to its best ability right now until we've got at scale other options.
Adam Jones (26:01):
Beautifully said. Kelly, if people want to find out more about yourself, whitby wood up and Optoppen project, where should we send our listeners?
Kelly Harrison (26:11):
Yeah, well you can check out our website at whitbywood.com. Also, Optoppen is Optoppen.org and I'm on LinkedIn, so please connect.
Adam Jones (26:22):
Thank you so much. We'll end the podcast there. Thank you.