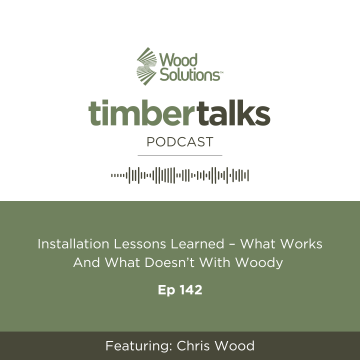
Chris Wood is GM at StandStruct and one of the most experienced influencer installers of timber buildings globally. In this episode, we learn from the range of projects that he's been part of. We discuss the things that have made projects successful, but also the things that make a project a challenge. Woody is an industry legend so listen in to learn from his experience.
Timber Talks Series 7
WoodSolutions Timber Talks podcast is back for series seven with our host Adam Jones, Australian engineer and founder of CLT Toolbox. This series offers a blend of informative and entertaining content focused on timber design, specification, and construction. The podcast features discussions with leading experts in the field, presenting the latest design practices, innovations, and intriguing case studies.
Adam Jones:
We just had Chris Wood the GM of StandStruck on the Timber Talks podcast for one of the final episodes so he’s one of the most experienced influencer installers in timber buildings globally. So, in this episode, we do a lot of things. We talk about the range of timber projects he’s been a part of, there’s been a few absolute success stories so we drill down into what has made the project successful, but also what made other projects absolute disasters because they certainly happen also and there’s things we can learn there. So, it is a wide-ranging convo. I have a lot of fun talking to Woody. He is an industry legend. So without further adoo, here’s my conversation with Woody.
Adam Jones (00:02):
Thanks so much for coming on the podcast, Woody. I think this is number two or three or four, I don't know.
Chris Wood (00:22):
Yeah, something like that. Hard to keep track.
Adam Jones (00:25):
It's hard to keep track. Yeah. Well, so good to have you back and as we're coming toward the end of the podcast. So, since we last spoke, what have been some of the more exciting buildings and projects that you've been a part of? So just give us an update on how that's been progressing.
Chris Wood (00:41):
Yeah, sure thing mate. So again, not really recalling the last time we met up on the podcast, but I know it's been a little bit between drinks, but obviously Bendigo Gov hub was a big one for us and a big one for Victoria coming off that one. A lot of learnings coming out of that. And then really, we've been sort of flat stick over the last couple of years. We've gone, we're local and interstate as well. So, Cowes community hub, Westfield Knox, Melbourne Racing Club, the Decjuba headquarters in Cremorne, St. Kilda Eco Center, Nash Cap offices and Charter Hall with Vaughan Constructions, a big VSBA bundle that ran for about six months. Fitzroy Sports Center. And we're currently working on Flinders Uni in the Factory of the Future in South Wales and a large educational project at St. Francis Xavier College in Barwick, which is about two and a half thousand CLT panels coming out of KLH. It's flat stick at the moment. It's good to see.
Adam Jones (01:58):
Yeah, that's so good, man. And at that very high level, how have things been evolving? That's a lot of projects, there's a lot of meetings, and there's probably patterns and maybe the things, same things pop up like whack-a-mole, but some things sort of get fixed. How are things evolving at that level?
Chris Wood (02:18):
Yeah, I mean it's probably only the last, I reckon the last sort of 12 months, we've seen a pretty significant shift in what we're doing and how we're being and early we're being brought on. I mean, going back a year and a half, two years ago, it was always really late in the pace we'd come onto a job or later in the pace when most things have been resolved. So, we're seeing a massive shift now where we're getting the call up at really early design development stage, like concept stage for install input. And mate, it's been so successful, I mean we've been able to just leave your ego at the door, all the consultants and just say, right, what works, what doesn't work. A design comes through, we can somewhat offer some opinions around rationalisation and it goes back through the system and then comes out,
(03:20):
and as it progresses, it's really about bringing all the other disciplines into the room as well and giving them the opportunity to have their say and educate them about the whole timber system. And I think I probably spoke about this at the Timber conference. It was a shining example of that was at the Tonsley project we're currently on in South Australia and it's just, we were on from about 25% DD and we've, we've been part of the journey the whole way through, and it's been an absolute success story, one of the best jobs I've been involved with. And even from the reports back from the guys on the ground, this has just been an absolute dream. So, it really goes to show that early, the emphasis around the early contractor involvement that everyone preaches, when it's done right, it's a really successful outcome for the project as a whole.
(04:20):
So, I'm seeing that shift now and I think there's a little bit of freedom in the industry now where there's a lot of cohesiveness and a lot of cooperation. I mean, you go back again those six, seven years ago when a lot of the IP was wrapped up in these bigger sorta tier one guys and it was all sort of hush, hush. And I think now that everyone's collaborating a bit more and there's a bit of cross-pollination across suppliers on big jobs, it's so much better for everyone involved now, because it’s not so secretive. And of course, there's always going to be a slight amount of IP wrapped up in things, but I think it's just a really collaborative environment at the moment. And that's the way I'm seeing the whole timber construction shift at the moment, everyone's willing to put in that upfront work for a better outcome
Adam Jones (05:21):
And that IP stuff. Yeah, you're right. There wasn't long ago that people weren't even allowed to speak at conferences in some tier one firms, and they'd have to get approval and get declined and then yeah, everything's hidden.
Chris Wood (05:35):
Yeah, it's bananas. I mean at the end of the day we were a bit cagey at the start, I suppose, around some of our IP, but I mean if people are doing it correctly, then it's going to be a better outcome for industry. So, the more collaborative you can be even with your competitors, the better.
Adam Jones (05:56):
If there's any, the worst thing that can happen is some projects getting burnt from it and then you've got bad stories, you've got a team of consultants and then you've got a team of people who are going to be ‘doctor knows’ next time it comes up. It didn't go well. And like you said, I'm keen to learn more about that project you mentioned, I think you said it was Adelaide.
Chris Wood (06:17):
Was Adelaide,
Adam Jones (06:18):
Yeah,
Chris Wood (06:20):
Yeah, Factory of the Future, in Adelaide.
Adam Jones (06:22):
And that's the one that was the killer, was it? As in go and went. Amazing. Yeah,
Chris Wood (06:27):
That's an absolute dream. But yeah. Yeah.
Adam Jones (06:29):
So, you were coming on it 25% and then tell us about that. So, what are some of the things that, how those engagements and those moments that you got?
Chris Wood (06:39):
Yeah, so we don't mean, we don't get too wrapped up in the technical aspect of it, like the grid set outs and the architectural and structural grids and things like that. I mean that's discussions for manufacturers and architects and structural engineers about what system works best to suit the project as a whole and the manufacturer's capabilities. But certainly, when we get down to connections and things like that and we get into the nitty gritty of beam to column connections, column to column to concrete, beam to concrete, steel, steel to timber, all those different proprietary connections as well and what works and what doesn't, rationalise spacings and typologies of screws and the CLT, all those sort of things. I mean it's easy to get caught up in a bit of paper sometimes and just, I pluck a few things out of a catalog that works brilliantly there,
(07:34):
but I suppose having a holistic view or a buildability point of view, it comes with a whole lot of rationalisation around that and thinking like a fellow would on the ground who's looking at the plans, at the end of the day, for the first time, it's like it changes things a little bit and just having that, I suppose, historical knowledge about all the different connections and how they work and how efficient they are. I mean that's the number one goal today is to make these projects efficient and go up really quickly so we can get a building envelope on them. And it's just, yeah, I mean we found the biggest, I suppose the most thing that we didn't expect the most was, the manufacturing, we would catch up to manufacturing. So, we're actually going that quick on site, quicker than our anticipated program, which meant we were sort of nipping at the heels of manufacturing. So, I mean that's a real good problem to have.
Adam Jones (08:42):
Yeah, that's so good, man. Yeah, I mean connections without you in the room or an installer in the room, you got material price you got, how easy is it to design for an engineer? Just look up a catalog and
Chris Wood (08:57):
Yeah, that's
Adam Jones (08:58):
Right. But without yourself there then do you have any bad stories? You don't have to name the project, but you get the drawings, it's too late, and then you've got this same connection detail, which is a shocker, and you got three months of install, you know what I mean? Is there anything like that?
Chris Wood (09:16):
Probably what you'd typically see is all of these KBrace arrangements and some of the doweling arrangements that go into these things. And that I suppose you can probably simplify a lot. It requires a lot of you know CNC time, a lot of time on site. We're kind of caught up with, there's a lot of European designs still floating around I think in the Australian market. So using smooth dowels in lieu of bolts and things like that and the sheer amount or the sheer number of dowels required in some connections and probably not having the, I suppose the insight into how difficult they are to install in real life. One or two connections is fine, but when you're talking about thousands of connections over a huge site, it can be very problematic even from a health and safety perspective as well. You are asking someone to execute thousands of dowels utilising even tooling or whatever. There's got to be a rotational system involved. So that RSI sort of stuff. So, there's a few different factors that go into our perspective of how connections work from not just buildability but from a safety perspective as well.
Adam Jones (10:47):
Yeah, and I mean if we're going for typical details, which everyone should be going, it's all the advantage there. You could just go hard on one connection detail and scale that out rather than just have everything chopping and changing everywhere, which never seems to work out, right. Yeah?
Chris Wood (11:06):
Yep. And I think where we're seeing a huge benefit at the moment is just bearing connections, bearing connections with an incline pin connection at the top of a beam-column interface. And it's insane. I think we're just
Adam Jones (11:22):
Drop it in.
Chris Wood (11:22):
We sort of down about 11 minutes of beam or something on top of a column, so it's an insane speed that we can assemble.
Adam Jones (11:33):
What is the swing on installation speeds on some of the projects you've been a part of? And it's probably hard to do a comparison with concrete. It's probably a question I might've asked you previously. Something I'm always interested in is if we're driving down the costs and trying to claw back material price, it does come down to stuff like that, where your speed is everything. What is the swing on speeds you get from a really good design, which you might be involved at the start versus something that doesn't work really well?
Chris Wood (12:03):
A hundred percent. We could be anywhere from an 11 minute per element up to half an hour, 40 minutes per element. So, there's a huge swing there, massive swing saying you're talking, we're sort of
Adam Jones (12:19):
Just from one, it could have be the same, just the connection chain is like three x?
Chris Wood (12:23):
Three x. Exactly, correct. Exactly right. And even when you're talking about international supply versus an Australian supply, there's a whole swing there as well. At a quantity of members required to make up one wall run. For instance, in CLT you might have two elements that might make 12 meters of wall in Australia, but if it's coming containerised overseas, that wall might be made up of 10 elements to get the 12 meters. So, that all needs to be considered as well when you're talking about efficiency in the build because there's a huge discrepancy there.
Adam Jones (13:03):
Yeah, and I guess is that question, do you want suppliers in the room? Well, I guess they've got a lot of value to add early, but there’s always that competitive tension. But in your role you'd be independent of suppliers, so you could probably provide that advice. And because
Chris Wood (13:21):
I suppose
Adam Jones (13:21):
Every local supplier is going to go hard on the shipping containers then. So yeah,
Chris Wood (13:27):
And it's all, I suppose a spreadsheet analysis at the end of the day, it might be cheaper fiber coming out of Europe, but or the labour required to put the additional panels in may be cost neutral, may not be cost neutral. So, it's all a bit of a balancing act really.
Adam Jones (13:48):
Yeah. One of the things that I guess people maybe just starting out, and maybe it is a risk that we're all going to keep on top of is… well risk in general. So rather than just shoehorn you down the whole moisture path, but what are the major risks to be aware of and what are the sort of things we can do to mitigate these risks and problems that might happen?
Chris Wood (14:13):
Yeah, I mean moisture is inherently a big problem. Not only a problem in timber building, it's a problem in conventional builds as well. I mean the reality is the performance of the building is reliant on the performance of the envelope and how well that's been executed at the end of the day. And I think it's a combination of all parties having a responsibility from design all the way through to the build all the way through to the passive sort of preventative measures that are implemented down the path in the life of the building. So, I just don't think there's a clear-cut answer to moisture mitigation. I mean, everyone knows that it's: get the building envelope on as quick as possible.
(15:07):
That's a golden rule of any building really. But I think we're seeing a lot, I suppose a lot, of products coming on the market now where we can monitor the moisture level and a building post envelope being enclosed. So, I think there's a responsibility that we look after our timber buildings for the life of the building and maybe it's a little bit smarter design as well. And it's not just a timber panel on a balcony, maybe it's a composite design or maybe it's something else to consider. So, I think from an installation perspective as well, it's important to really have those conversations, those strategies upfront before you even step foot on-site and making provision even within the design development or the manufacturing development of certain provisions within the building that we can use as water mitigation. So, we talk pretty heavily at the start of buildings about how we are going to dissipate the water in a rain event and how we're going to keep the timber dry somewhat.
(16:25):
So, I think it's an important discussion to have, but it's important to have those discussions early. I mean, we've always come undone when it's a last minute, how are we going to mitigate these issues? And then it becomes just a series of events of a trial and failure until you try and get something right. And you're trying to do that in conjunction with building a structure as well. So, I think that those early conversations and the early moisture strategies, especially during assembly, is really important. But then continuing that strategy down through the remainder of the build and then into its usable life.
Adam Jones (17:06):
Yeah. Yeah, that's great. It's probably one of those: every builder has to learn from experience or something had that first one because when I was at XLam was just like everyone on their first time would, moisture would just be a bit of an issue. But then you go to other sites and it's well managed.
Chris Wood (17:24):
100%, Like you say, I think even manufacturers have a responsibility. It's their product that they're promoting and bringing to a market. So there needs to be some buying and input quite heavily from the manufacturing side of things as to how we're keeping the timber safe and educating the consumers on how that's done.
Adam Jones (17:48):
Shooting from the hip here, but there's a lot of new projects going around. I saw another Highrise building going up in Milwaukee in USA, obviously you got Atlassian Tower, you got C6 in Perth. Do you get excited by high-rise buildings and stuff like that? Do you think there's a big future in it? And do you see, I guess the benefits of scale in the industry like that?
Chris Wood (18:12):
I think I do…you know particularly with Atlassian. I think that the strategy for the timber portion of the build is quite probably inefficient, somewhat. I think that when we talk about high-rise, I think that there's a lot more to the story than just assembling the timber. It's quite high-rise is a quite challenging projects at the best of times. So, I think that we're going to see a lot of learnings come out of the space when we're talking about high-rise timber construction. And some of those lessons may not come out for five or 10 years, but certainly it's exciting. But I think that we've got a little way to go first before we are taking the leap into these massive timber buildings. I think master the craft before we shoot for the stars. And not saying that we're not there. I think that we are, and certain people are, but I think that, yeah, I'm a little bit trepidatious about the future there. But yeah, baby steps I
Adam Jones (19:30):
Yeah, well said. And I guess it's good to have innovators in the sense of having ROs to get those learnings, but then yeah, there's levels of what the step forward is, so yeah.
Chris Wood (19:47):
A hundred percent.
Adam Jones (19:48):
Yeah. So Woody, I mean looking forward into the future, what do you see as the future of our industry? Where do you see things heading over the coming 5, 10, 15 years?
Chris Wood (20:00):
I think we've pretty much just touched on, I think we're just going to keep pushing the boundaries really. And I think mean Australia as a nation are probably pretty good at that anyway, taking what we need from overseas and making it our own and pushing the boundaries here. I think we're going to see a lot more in the Glulam space. I think that that's probably something that we really haven't unlocked in Australia yet. That's sort of the best like Glulam and the ability of what Glulam can create. I think that that's going to be the next real trend in Australia. And we're seeing some structures come across our desk now that are really pushing the limits of Glulam and design and architectural design. So, pretty exciting there. And I think we're going to see a massive shift in industrial and industrial movement into timber as well. So, we've got a couple of, we've been involved in a couple of projects now with some large multinational sort of battery building property groups, and I think that's probably the next big ship for that industry is to move into a more sustainable way of building.
Adam Jones (21:21):
Yeah, it's funny, the Goodman's project in Moorabbin, you know and the warehouse there, I've been in this space for a while now and my family and mates from back at high school, they don't really know what I'm doing. But then, because that's in our area, even CLTToolbox, they're like, oh, there's this software thing. They're like, what the hell? Everyone knows it from that building going up. It's like everyone's blowing me up all the time by how good it looks and all that.
Chris Wood (21:48):
Insane. I sort of don't tell people when I go out what I do anymore because
Chris Wood (21:53):
It’s almost like every person you meet, you've got to start at ground zero again and explain to 'em what CLT is or engineered timber is and they sort of look at you with a vague look and so you just build frames commercially. Yeah, they're just thinking
Adam Jones (22:06):
About something else with their eyes glazed over a lot of the time. And that's just how it works.
Chris Wood (22:10):
That’s what I say, yeah, I'm in construction.
Adam Jones (22:14):
That's great mate. If people want to find out more about yourself, where should they go
Chris Wood (22:20):
Mate. You can go to our website, www.standstruct.com.au. We're also on the socials as well, or reach out directly to me, mate. So, my number's plastered all over the website, so always happy to have a chat or catch up for a beer with someone.
Adam Jones (22:41):
Yeah, absolutely. Yeah, StandStruct, you're in good form there. So, I'll second that. Good stuff, man. Well thanks so much for coming on the podcast so many times and we'll leave it there. And yeah, appreciate your time and that was a great chat,
Chris Wood (22:56):
Really appreciate you, mate.
Adam Jones (22:58):
Cheers mate. Cheers brother.