
Overview
The Archiblox Carbon Positive House (CPH) brings together a multitude of eco-friendly design features in their space efficient, highly adaptable prefabricated housing range. To mention just a few of the innovative features:
- Modular furniture allowing room layouts to be adapted to suit the changing requirements of occupants' activity through the day
- Sliding internal and external green walls allowing the easy adjustment of light filtration with changing seasons
- Green roof and earth berm for carbon storage and thermal mass
- Grey water sustainably treated and recycled on site for toilet flushing
- Surplus solar power generation
- Sustainability focussed selection of suppliers including consideration to material transport costs (maximising the use of locally sourced, Australian made products)
- Maximising the use of sustainably sourced timber due to its naturally low embodied energy
- Prefabricated construction minimising construction time and associated costs (including carbon footprint)
The findings of a life cycle assessment of carbon (by eTool) include an impressive 71% saving in the design embodied energy compared with structures providing similar functionality. This saving, achieved through rigorous analysis of the materials combines with the operational carbon positive features resulting in an overall 116% saving in carbon per occupant per year considered over the life of the house - reducing global emissions by 659kgCO2e/occupant/yr.
Structure
A few simple but thoughtful rooms make up the single story house, the framing of which supports an earth berm wall and green roof. Even with these extra loads, Archiblox have kept the structure straightforward and economical. Timber framing was the clear choice for Archiblox director, Bill McCorkell, because 'timber is a much more sustainable material and carries a smaller carbon footprint than steel'. The walls are framed with MGP (pine) studs while the modest roof and floor spans are supported by LVL rafters, joists and roof beams. These timber members are common in residential construction and cheaper than steel - an important factor for Archiblox's concept of a small reproducible house that is architecturally designed, sustainable to the highest standard, yet affordable.
As MGP studs and LVL's are made from softwood, the timber is grown in plantations and to ensure the plantations are ethical they are FSC certified. FSC certification ensures the plantation was not established via forest conversion (post 1994), does not use pesticides, does not introduce exotic species, uses a planting methodology that preserves soil structure, and is on land that was obtained without negatively impacting indigenous communities. The layout of the plantation must also take into account the surrounding ecosystem by promoting the restoration and conservation of existing natural forests and preserving adjacent wildlife corridors.
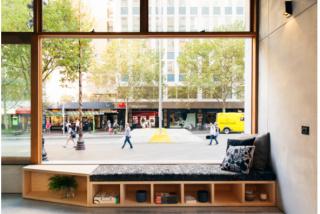
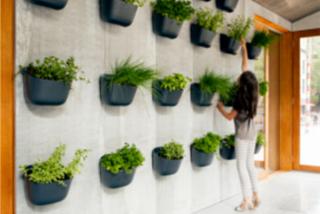
Exterior
The external façade is a mix of materials, including earth, hardwood slats and UBIQ panels, each of which uniquely contributes to the sustainable design vision. The earth berm wall is an optional feature that envelops the back wall at an angle of 30-45 degrees, and wraps over the roof, resulting in a green roof. It is stabilised by rock gravity loads as well as vegetation. The overall mass acts as a heat sink, regulating internal temperatures during the day and night as well as insulating the house during winter and summer.
Sawn Silvertop Ash slats clad portions of the house to provide a beautiful, hardy finish. The hardwood has high natural durability (class 2) and is left uncoated, with the intention to silver naturally in the weather. Radial Timber Sales (Victoria) was enlisted to grow and mill the timber as their ethical innovative approach melded well with the CPH design philosophy. The company saws logs into wedges (like a pizza) which allows them to produce more boards with the same amount of timber when compared to conventional methods. This is an important area for innovation as only 30% of a timber log is turned into floorboards following conventional saw patterns.
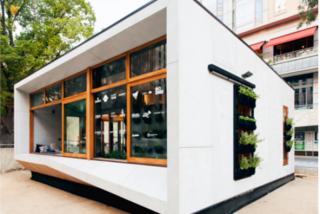
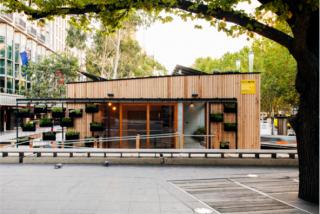
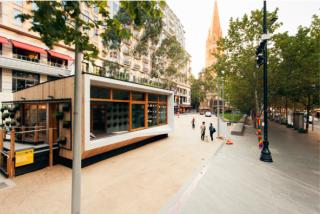
Interior
A well honed collection of innovative products make up the internal linings and joinery. The materials are each architectural, hardwearing and sustainable in unique ways. For example, the kitchen benchtops, joinery, and modular cabinetry are supplied by Crafted Green, a family owned business that makes joinery from sustainably forested hardwood plywood with no added urea formaldehyde adhesive. UBIQ created an alternative to fiber cement boards called the INEX panel, which is made of low carbon fiber reinforced cement composite, and contains 60% recycled materials. They are non combustible and an ideal material for the flooring and walls of this house, making it suitable for high fire-risk zones. Lastly, the house is insulated with Earthwool, a non toxic product that regulates internal temperature and reduces energy consumption.
The internal layout is dynamic, with generous ceiling heights and moldable spaces. A wall of high windows promote cross ventilation by encouraging natural convection and circulation. Moving joinery allows spaces to expand and contract to suit different activities and times of the day. The benefit of designing a modular house is that it will be made over and over again. This has meant that considerable time and thought could be afforded to refining material choices and the layout - all while targeting a friendly price point.

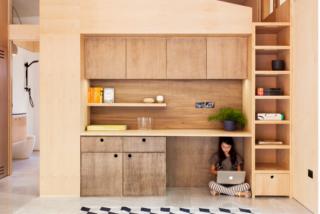
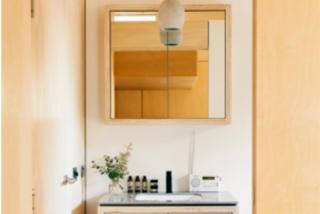