752 High Street
Thornbury VIC 3071
Australia
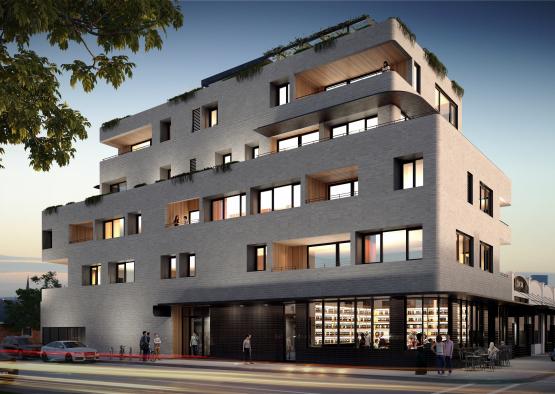
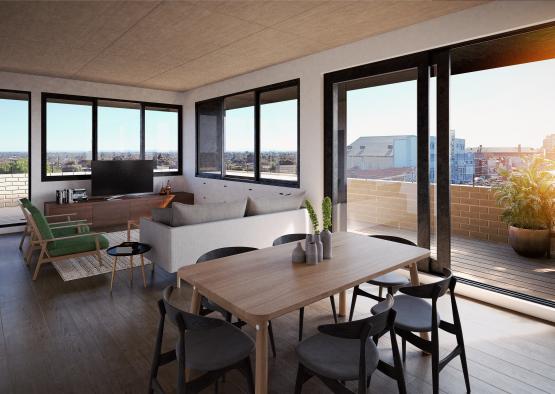
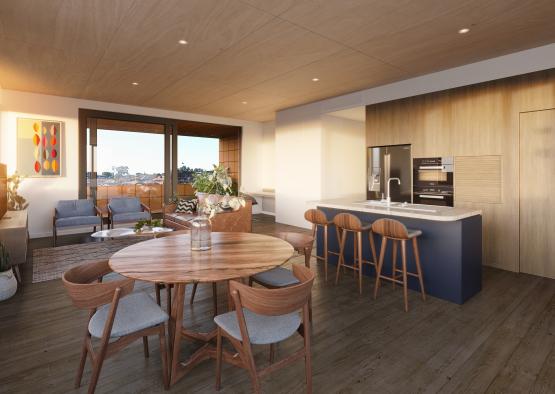
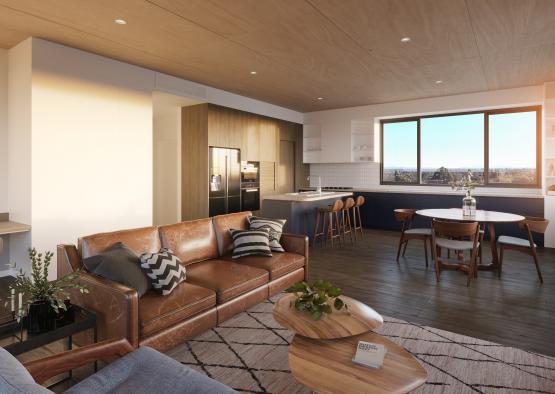
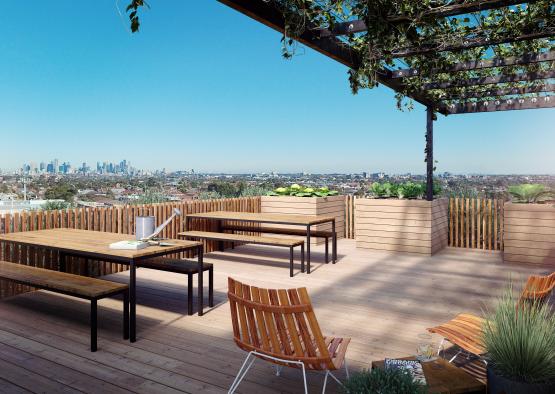
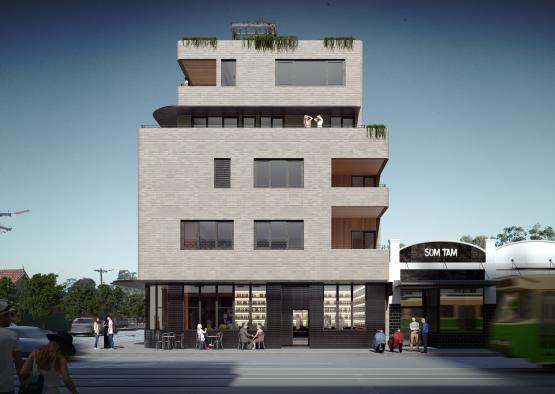
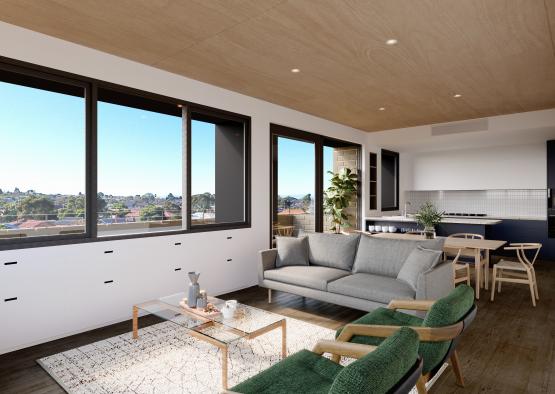
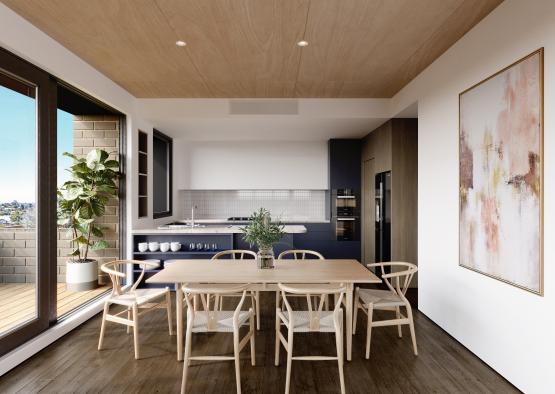
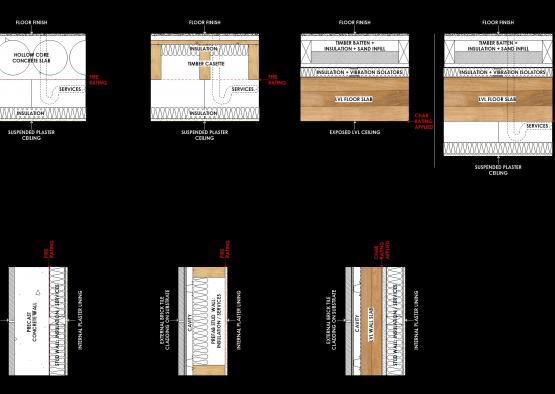
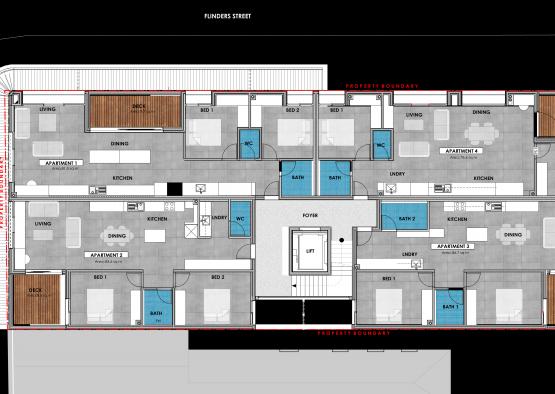
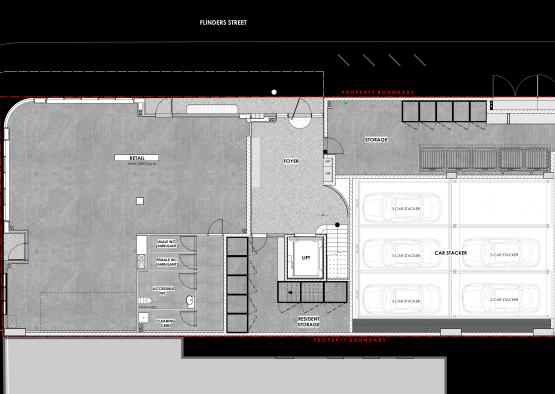
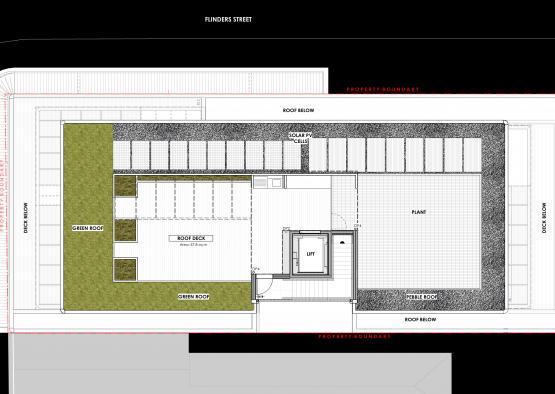
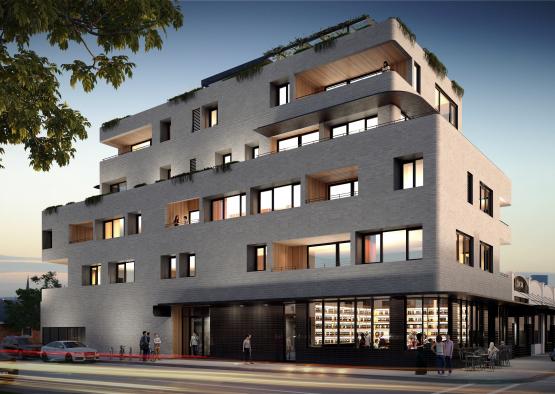
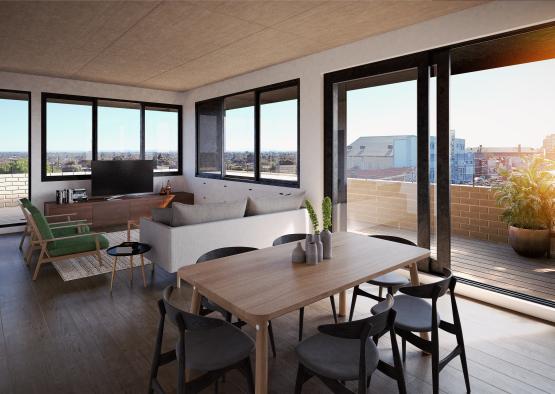
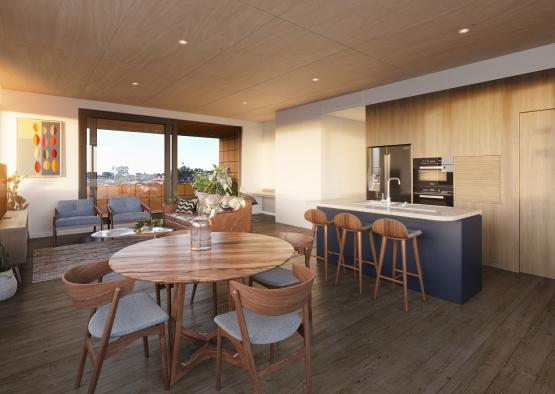
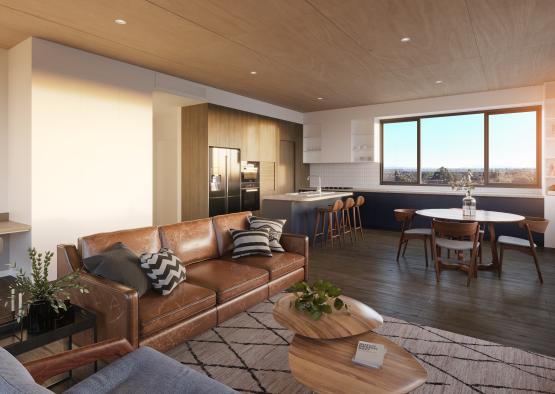
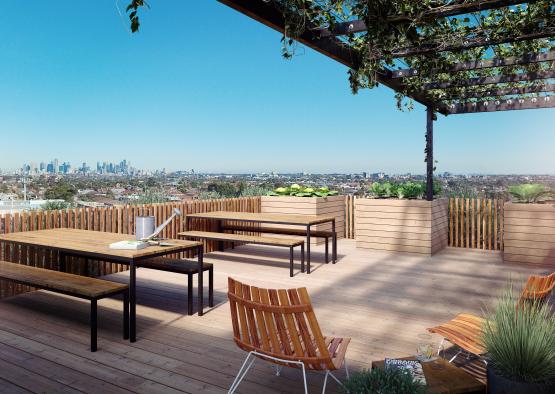

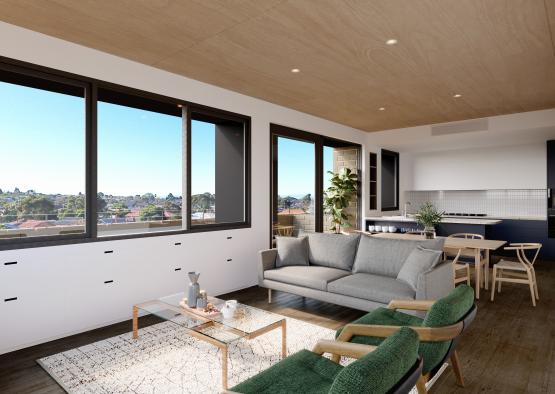


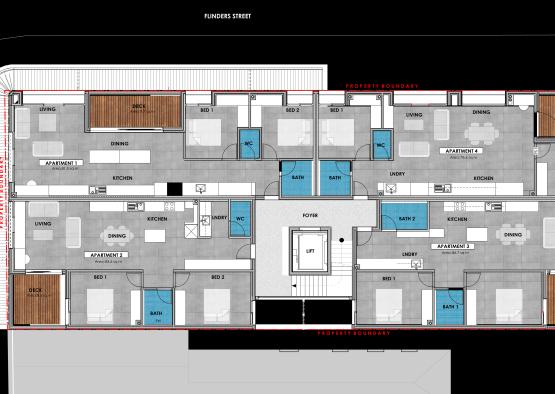
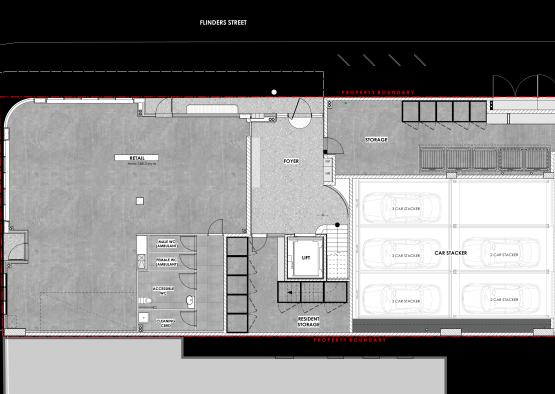
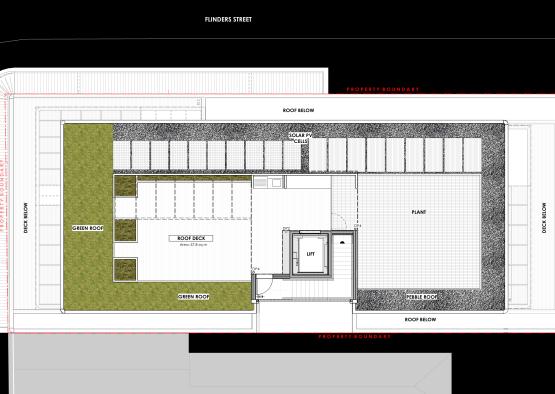
Overview
Scheduled for completion in 2021, the imperative for the High Street apartment project is to produce an environmentally sustainable building that explores ways to reduce the carbon footprint of a multi-residential building project.
-37.7557313, 145.0013537
Structure
The main structural system of the High Street apartments is the Cross Laminated Timber (CLT) system. The structure is however, a composite system. The ground floor retail space is made from traditional in-situ concrete and concrete block work, while the remaining four residential levels and rooftop deck are made from CLT, with some additional structural steel as a necessity for longer spans.
Although the CLT material differs in many ways to concrete, in the end it is still just a structural way of putting a building together. It looks very different when being installed, but it gets clad and lined like any other building. The final product is no different in appearance, even though there are many different and improved performance outcomes. Moving forward as fire performance is innovated, there should be more options available for exposing the CLT.
The CLT was all prepared beforehand in the XLAM factory in Albury, NSW. There it is cut to size, and any openings and service requirements are cut in using a CNC machine. Prefabrication is often synonymous with standardisation, and is therefore often deemed boring. While kit houses are all the same, what engineered timber allows, due to the improving technology in CNC machines, is essentially any building can be manufactured with less limiting parameters due to the prefabrication system. All the panels can be cut to different sizes and shapes. It’s a much more exciting way of looking at a prefab building, and it’s a process that is constantly advancing. Ultimately the CLT becomes a means of building, rather than a means of designing. Every apartment in the High Street project is unique, with a mixture of sizes and shapes. Using CLT didn’t limit the architecture, but informed the decision making and process.
Improvements range from decreased construction time, to how easy it is for the builders and subcontractors to work with the material. CLT is about 30% of the weight of concrete, so footings are reduced in size and therefore cheaper due to the decreased load. For the High Street project, the site had contaminated soil that needed removal, so the reduced excavation meant less contaminated soil to remove. The prefab nature of CLT eradicates the need for formwork and props that are required with concrete, which hold up the building on each floor until the concrete sets. Savings are also often found due to the reduced need for scaffolding. The panels are brought in and assembled on site, the product becomes the barriers. The timber can also be clad in the factory so that the external walls can go up fully finished.
All these measures save money, so at this stage the project is looking to be 5-10% cheaper than concrete. Even if there were no cost reductions, the use of engineered timber will still give a better quality, and more sustainable outcome.
When CLT is prefabricated in a factory, all other elements of the building that have an impact on the CLT need to be understood and planned for in advance, such as whether a services duct is penetrating through a wall. It’s expensive and difficult to make big modifications to CLT on site -making a small cut for a GPO is fine, but forgetting an exhaust duct could be a big problem later. It is not always easy to coordinate these elements of a building, but detailed planning is essential to a streamlined and efficient use of CLT as a structural system.
The regulatory environment is becoming much more accommodating to the emerging construction method. The Building Code of Australia (BCA) has undergone some major changes recently, which has made laminated timber much easier to use.
Exterior
The brick cladding for the building was put to council during the planning stages, before CLT was employed as the structural material.
Gardiner also saw the brick as a sensitive response to the building fabric in the immediate context, as the northern suburbs of Melbourne are famous for their brick buildings. A system to allow for the brick cladding was incorporated into the CLT, with a light grey brick chosen. Terracotta tiles will be used to line the recessed balcony walls and soffits.
There is no limit to what materials a CLT building can be finished with. Although a timber building is a new typology, it does not need to look that way. For Gardiner Architects, the brick tile cladding was representative of the inner north patchwork vernacular.
Interior
Current Australian building codes meant that for the High Street project, Gardiner Architects weren’t able to expose the timber structure. While this affected the visual appeal of having the timber exposed, the benefits of incorporating the structural system went far beyond the aesthetic result and potential attractiveness to apartment buyers.
The material selections for the interiors of the apartments were chosen for the warmth and texture that timber provides, while having a paired back colour palette to allow for individual residents to infuse their own style. The apartments feature timber floors and joinery throughout, plaster walls and ceilings, with some apartments featuring plywood ceilings.